An unlikely partnership
Endress+Hauser works closely with promonta, a disability-inclusive operation in Reinach. The employees there prepare electronics housings for Endress+Hauser flowmeters ready for assembly. It’s a long-standing partnership spanning over 30 years and a success story for all concerned.

Sometimes mainstream employment and supported employment are very closely integrated. That’s true in a very physical sense in Reinach, Switzerland, where the Endress+Hauser Flow company campus is barely a minute’s walk from promonta. Operating as part of the Eingliederungsstätte Baselland (ESB) social and vocational integration service, promonta is located on the second floor of a building just across the road from Endress+Hauser. It employs people with physical, intellectual and psychological disabilities. The two organizations are united by a shared interest in flowmeters. Endress+Hauser manufactures them, and promonta prepares components for them – most notably assembly-ready electronics housings.
“Our purpose is to enable people with special needs to develop their skills, have agency in their lives and participate in meaningful work,” explains long-time promonta plant manager Nikola Kafadar. Endress+Hauser has been supporting this valuable social mission for over 30 years. The partnership in its present-day form was initiated by Manfred Bieli. Back then, ESB employees were already performing various simple tasks for Endress+Hauser, such as packaging promotional gifts. “ESB asked me if we had any more challenging work on offer, and I was instantly sold on the idea. We shook hands on it there and then,” the long-serving Endress+Hauser Flow plant manager recalls.
“In terms of quality, on-time delivery and costs, promonta can hold its own with any other partner.”
Manfred Bieli
former plant manager at Endress+Hauser Flow
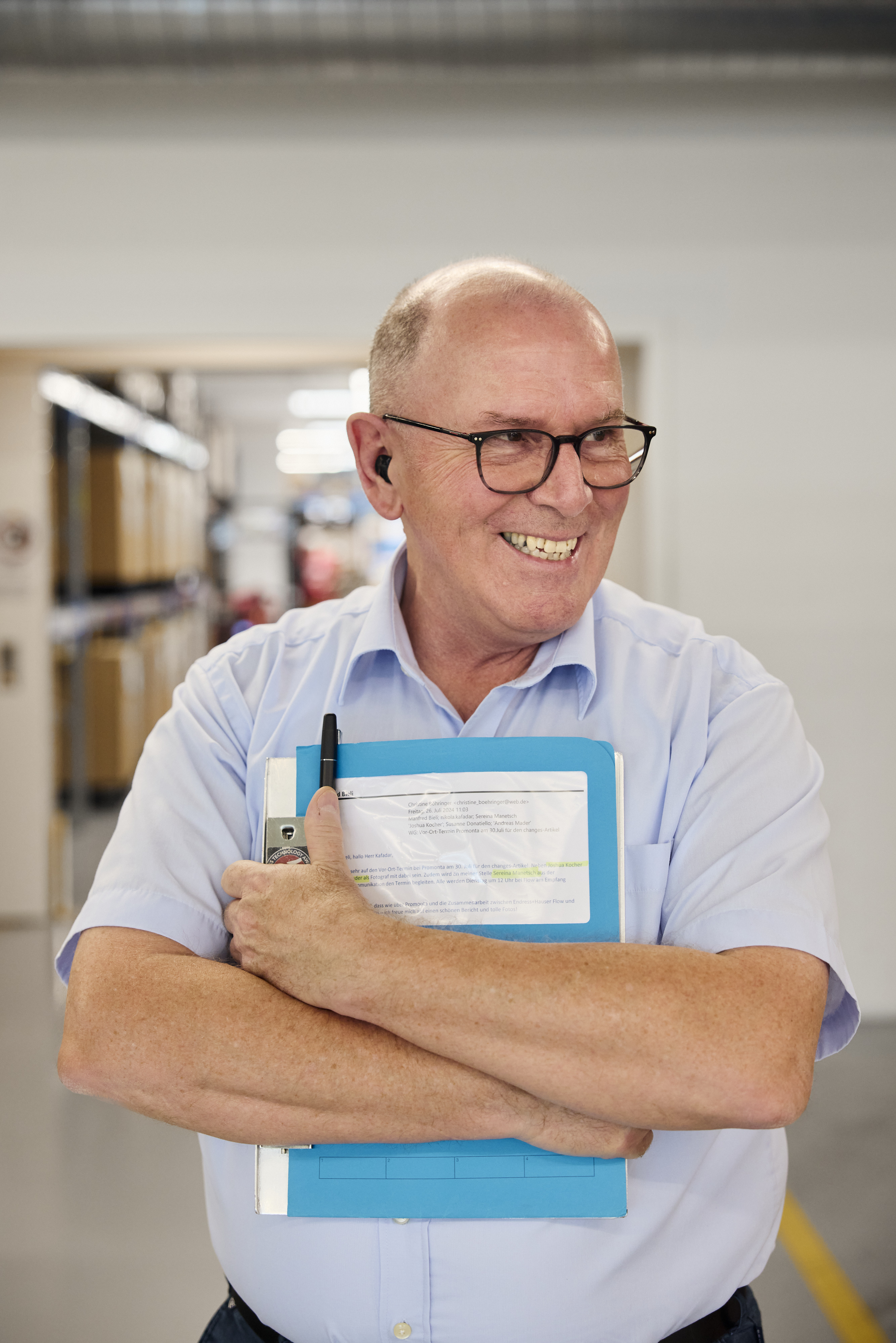
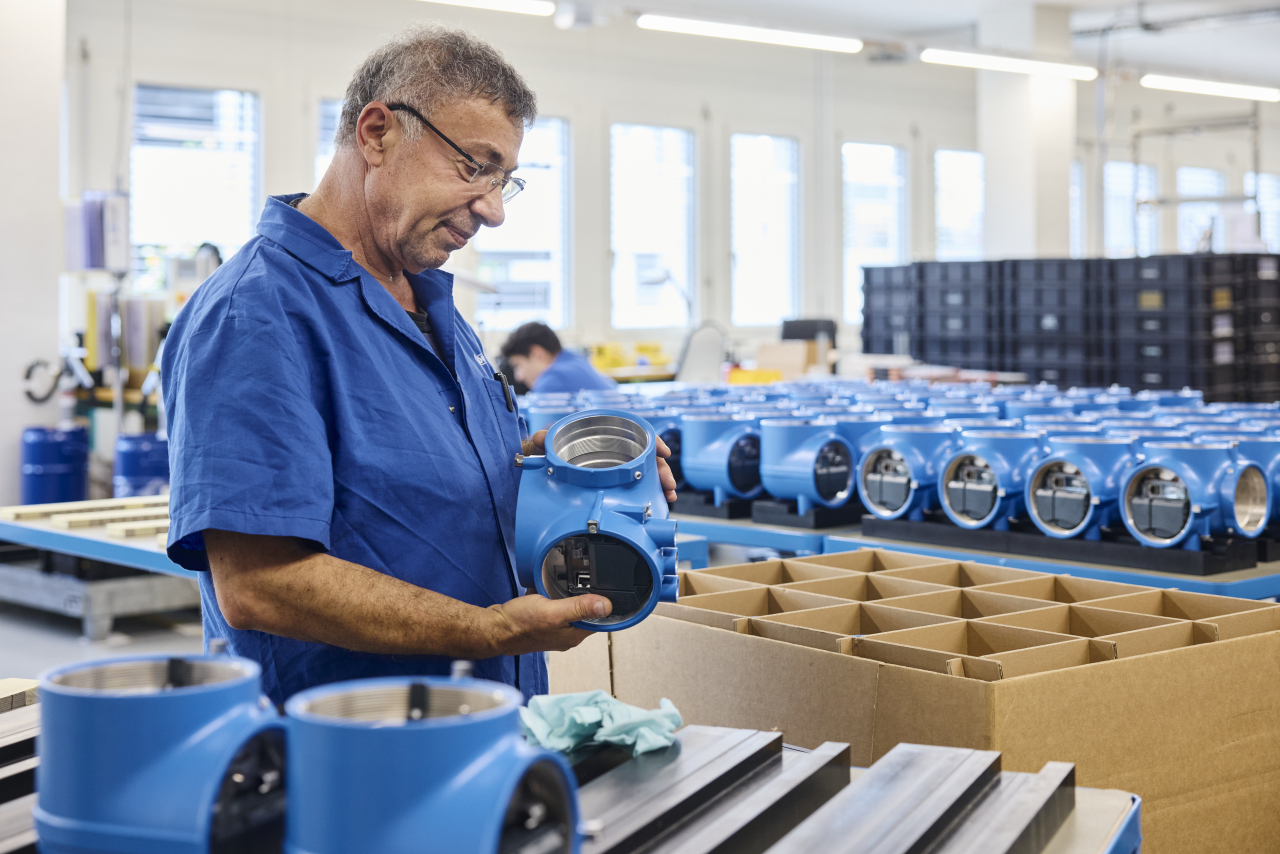
Quality: promonta is now one of Endress+Hauser’s A-list suppliers.
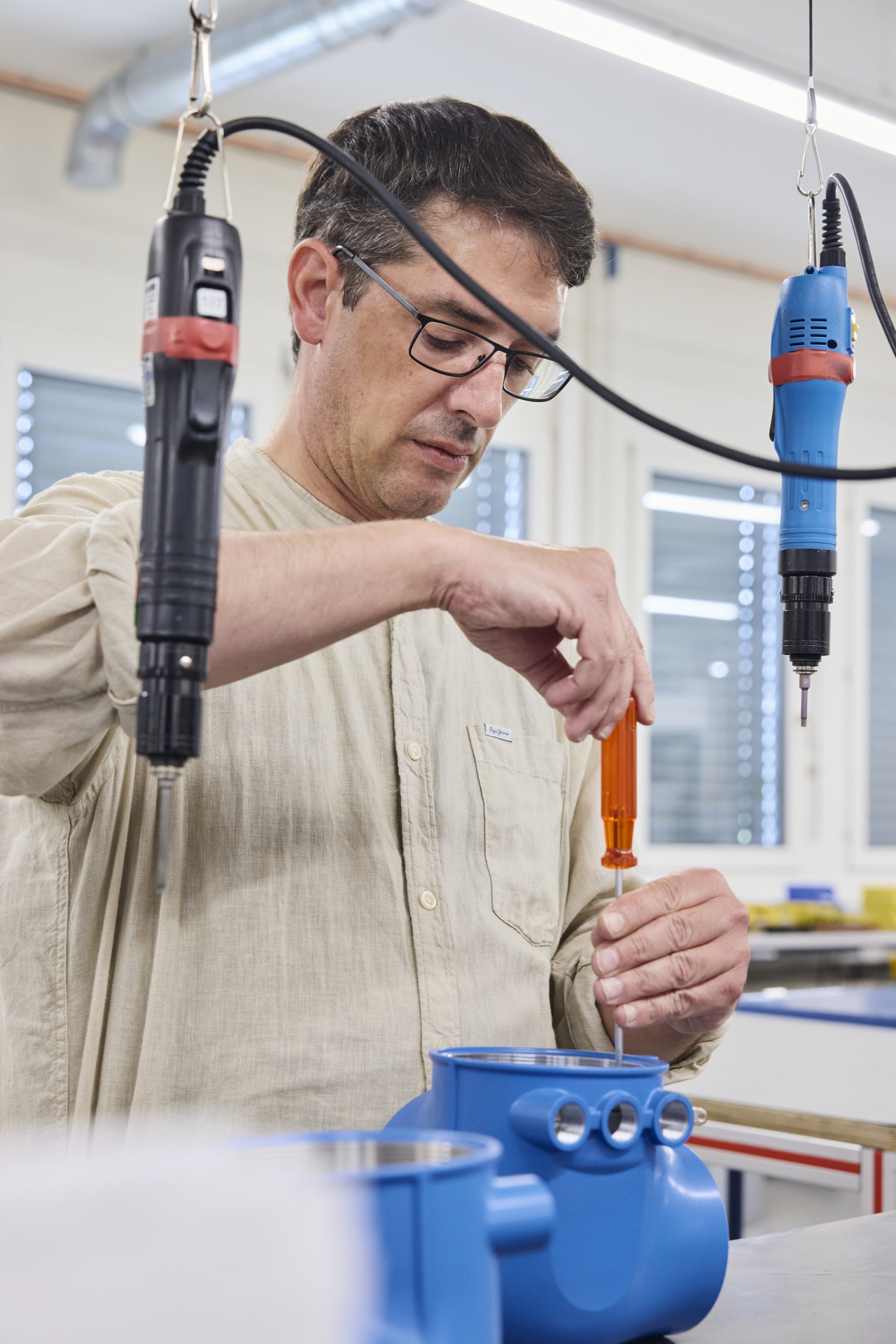
Concentration: promonta employees prepare electronics housings ready for assembly.
Growing together
The partnership first began with a series of discrete orders. Then came the contract for pre-assembly of housings. From there, Endress+Hauser’s flowmeter production grew steadily over the years, ultimately putting enough work ESB’s way to warrant setting up a dedicated plant. And so promonta was born. That was in 2007. Today, promonta has around 90 employees, who supply 750,000 components annually to Endress+Hauser Flow production sites worldwide. They take care of everything: assembly, quality control and logistics. The workstations at promonta are state of the art, and the entire operation is closely integrated into Endress+Hauser’s production systems. Equally importantly, the employees get to work in a safe, supported environment.
Christian Oser is one such employee. He has been working at promonta for 19 years. Some days, he’s folding shipping cartons for electronics. Other days, he’s working on housing covers or fastening them in place with screws. He loves his job. “It’s all a lot of fun,” he says. Today, he’s sitting in front of a bin of housing covers, sticking adhesive labels on one after the other. Everyone else around him is hard at work too – the room is a hive of concentration, rattling machines and whirring screwdrivers. In the room next door, Roberto Zicaro positions his driver over a housing and drives in a screw. The housing will be used to hold the electronics for a flowmeter that will be used in the food & beverage industry. “I find this kind of precision work really exciting,” he says. He has to make sure that the screwdriver is positioned correctly and that the screw is properly seated. “My work always gets checked at the end, which is another important part of quality.” He feels good knowing he’s making a valuable contribution.
“Our employees are proud to be working so closely with industry.”
Nikola Kafadar
long-serving promonta plant manager
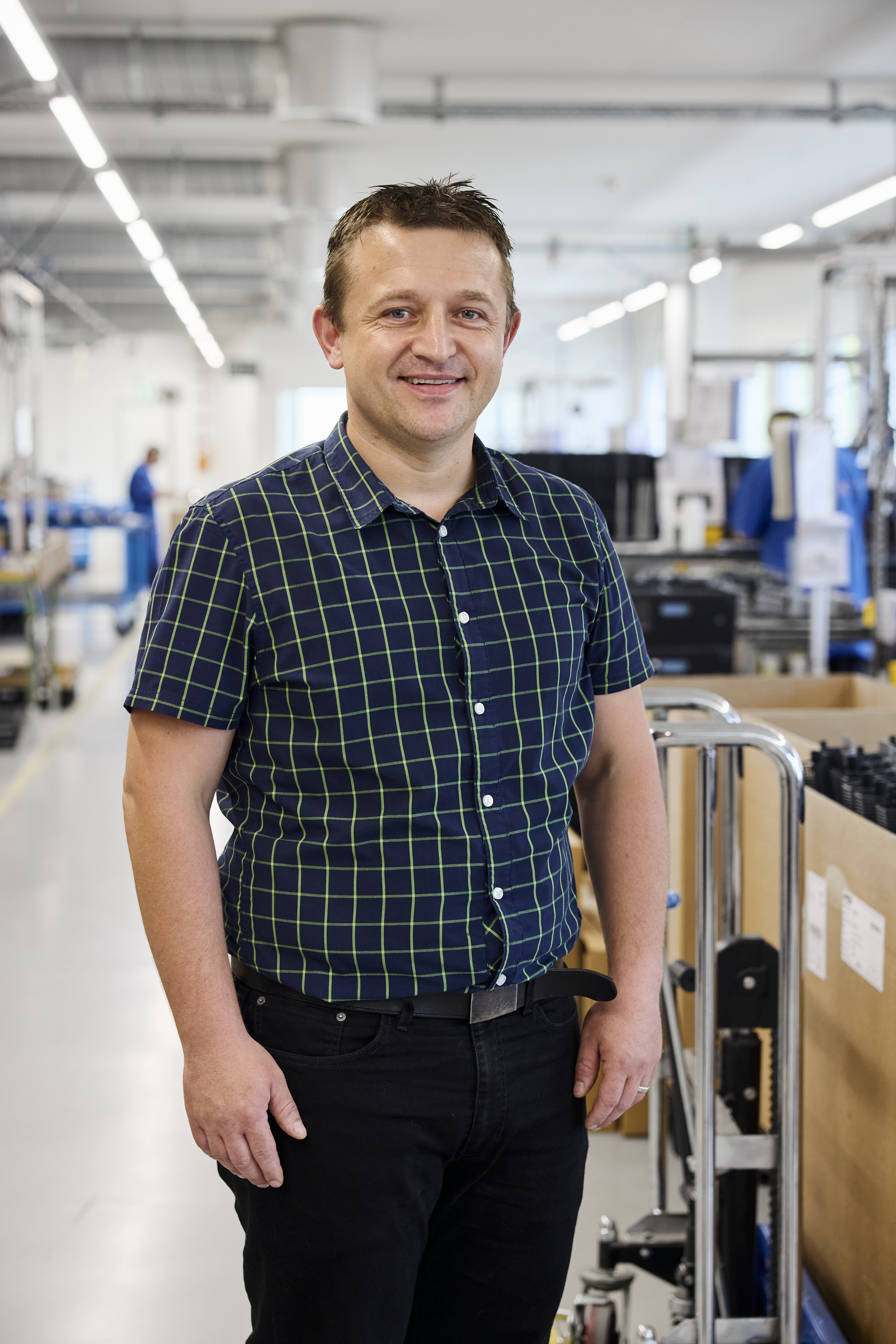
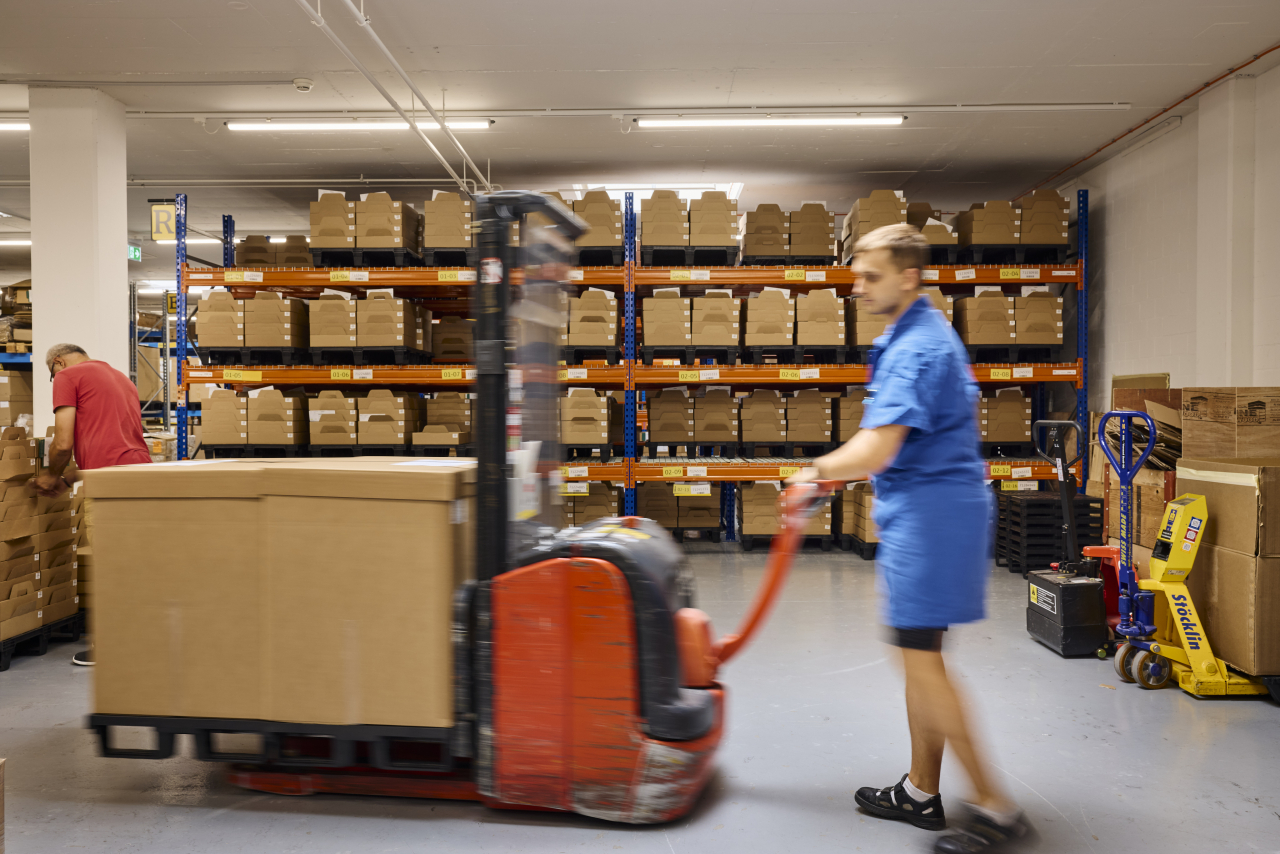
Shipping: promonta also takes care of the distribution logistics involved in getting the assemblies to production plants all around the world.
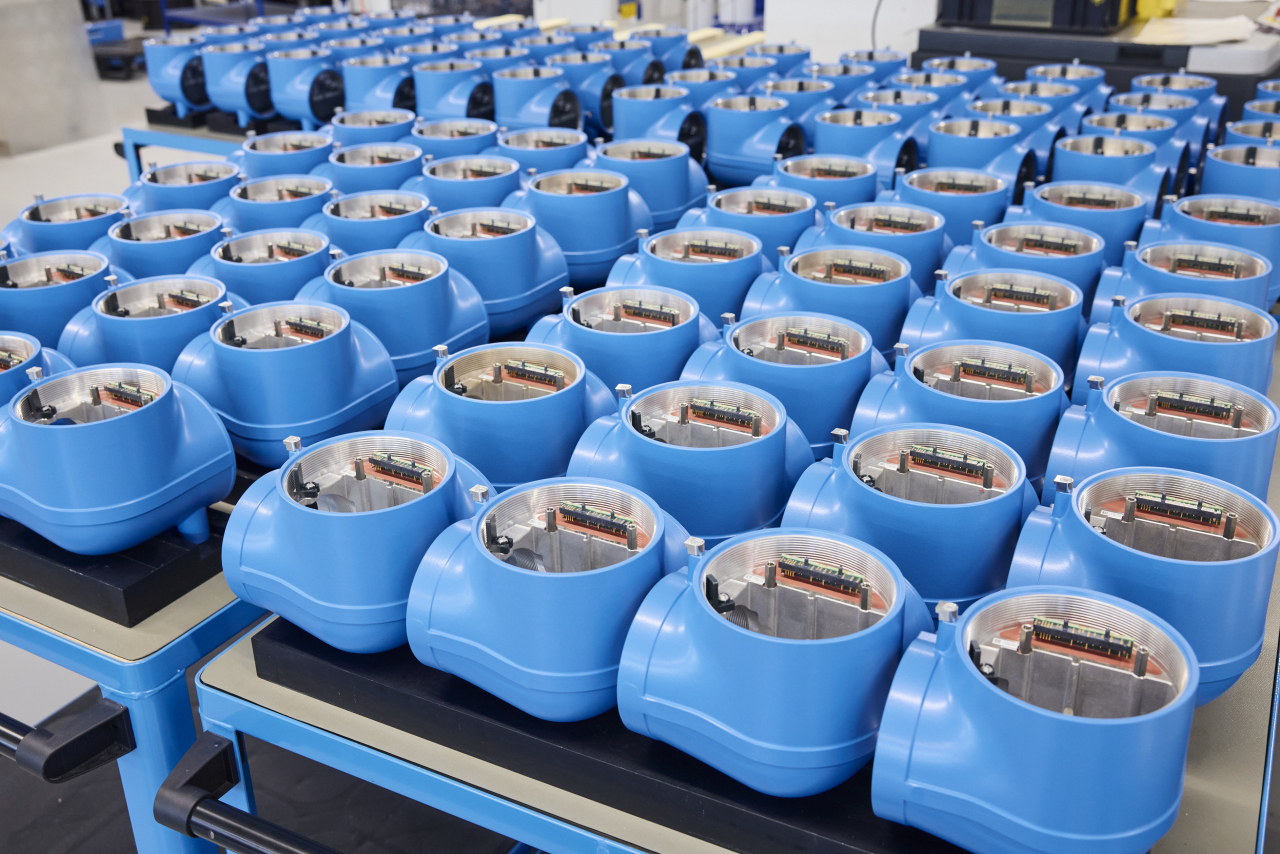
Growth: promonta now supplies 750,000 components annually.
Fostering potential
“Because the tasks here are diverse and involve varying degrees of difficulty, we can provide individualized work for people with special needs and hence help them participate in the labor force and realize their potential,” says Nikola Kafadar. This approach also ensures that the components supplied by promonta meet Endress+Hauser’s expectations. “We may be a social enterprise, but we still have to deliver to world-class standards and be flexible,” he explains. And on that score, promonta has consistently done an excellent job over the years. It has successfully adapted to all the changes and new products Endress+Hauser has put its way.
“In terms of quality, on-time delivery and cost, promonta can hold its own with any other partner,” comments Manfred Bieli. He points to a cowbell in the lobby at promonta – a badge of honor that Endress+Hauser awards to suppliers for outstanding service. promonta has won it multiple times. Even better: the disability-inclusive contract partner now ranks among Endress+Hauser’s A-list suppliers and enjoys preferred-vendor status.
“Our employees are proud to be working so closely with industry,” says Nikola Kafadar. promonta employees are regularly deployed on-site at Endress+Hauser Flow, and it’s not uncommon for a permanent position there to be their gateway into the mainstream labor market. Kafadar: “It’s a model that brings us a step closer to inclusion.” Like him, Manfred Bieli has never regretted that pivotal handshake all those years ago. On the contrary, it was the start of something wonderful, both professionally and personally: “promonta has taught me a valuable lesson: never define people by what they can’t do. Always focus on, harness and foster their potential.”
Published 29.11.2024.
Dive into the world of the process industry through new exciting stories every month with our «changes» newsletter!
Subscribe to newsletter