Total transparency
For supply chains, transparency is key, and it starts with effective inventory management. Here, digitalization is driving solutions for a wealth of new applications – such as level monitoring in mobile, decentralized storage tanks and silos. The customer benefits range from efficiency gains to completely new business models.
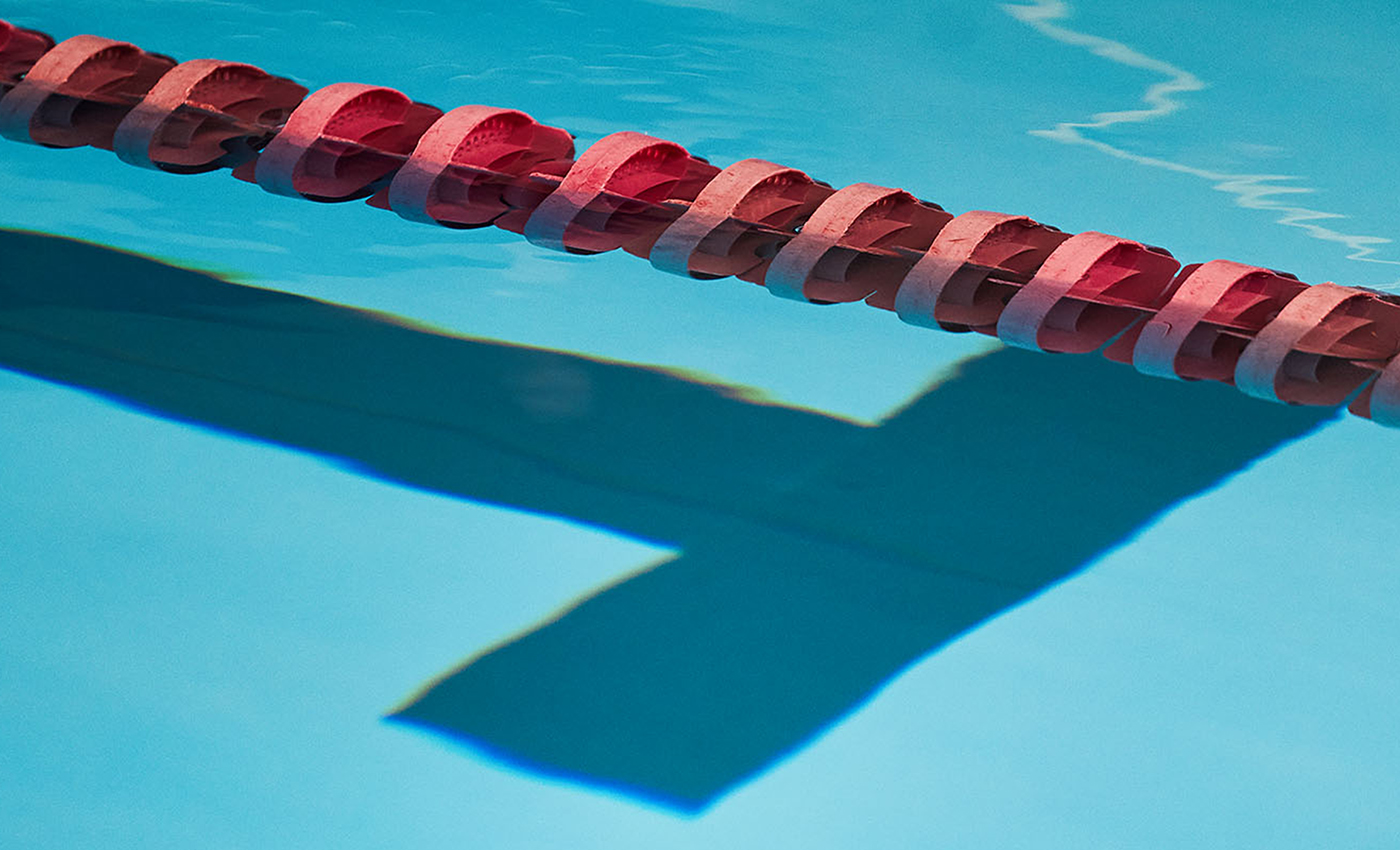
The skies are clear but for the occasional puff of cloud, and the outdoor water slide at the Vestbadet aquatic center in the Danish town of Viborg sparkles blue in the sunshine. On this perfect summer’s day, three children are racing each other down the slide’s triple lanes, reveling in the 25°C warmth of the pristine water. If it were up to him, Kenneth Laursen would be cooling off in the pool, too. A dip would be just the thing – provided, of course, that the water is the right temperature, has a pH of between 7.0 and 7.6 and contains at least 1 mg of free available chlorine per liter.

1 Clean swimming pool water is a question of the right chemistry.
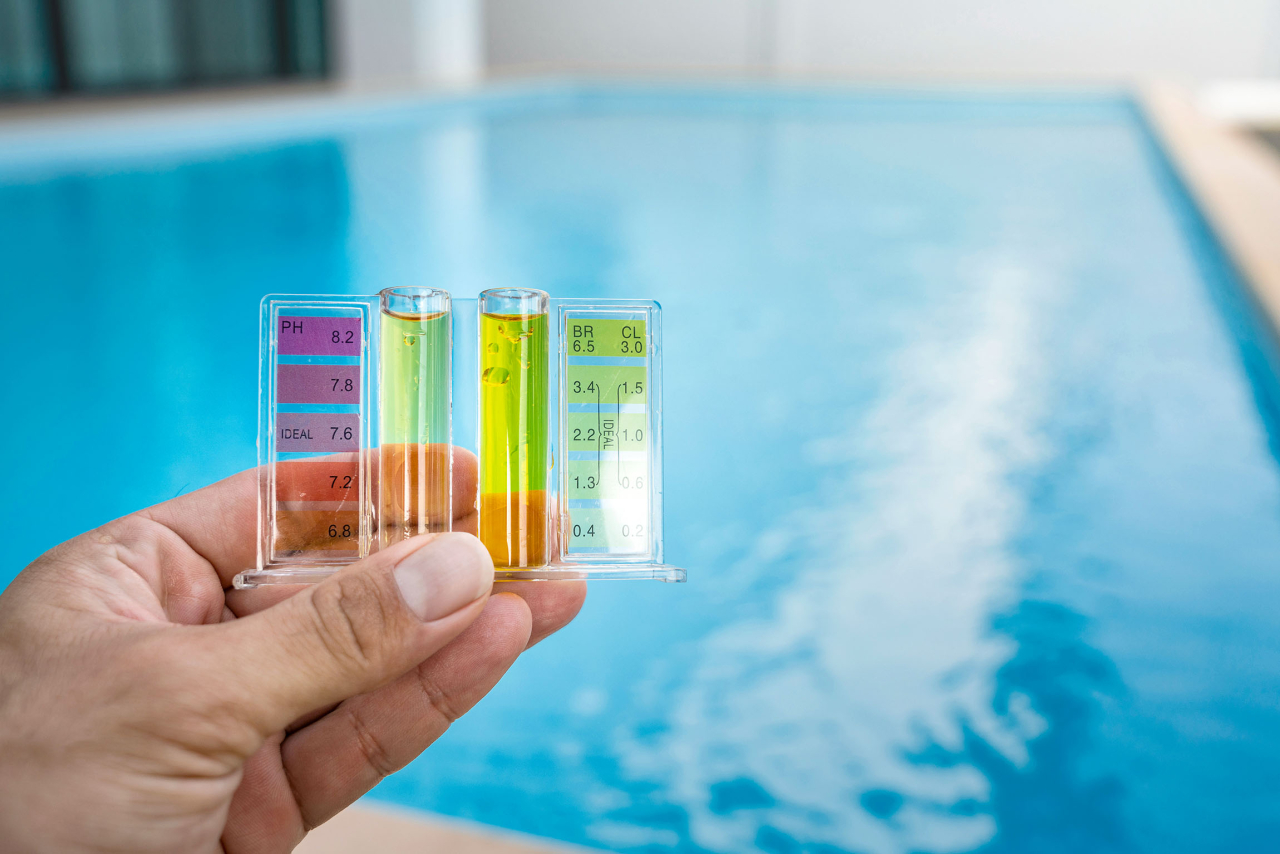
3 Color indicators show whether the water has the optimal pH and sufficient free available chlorine.
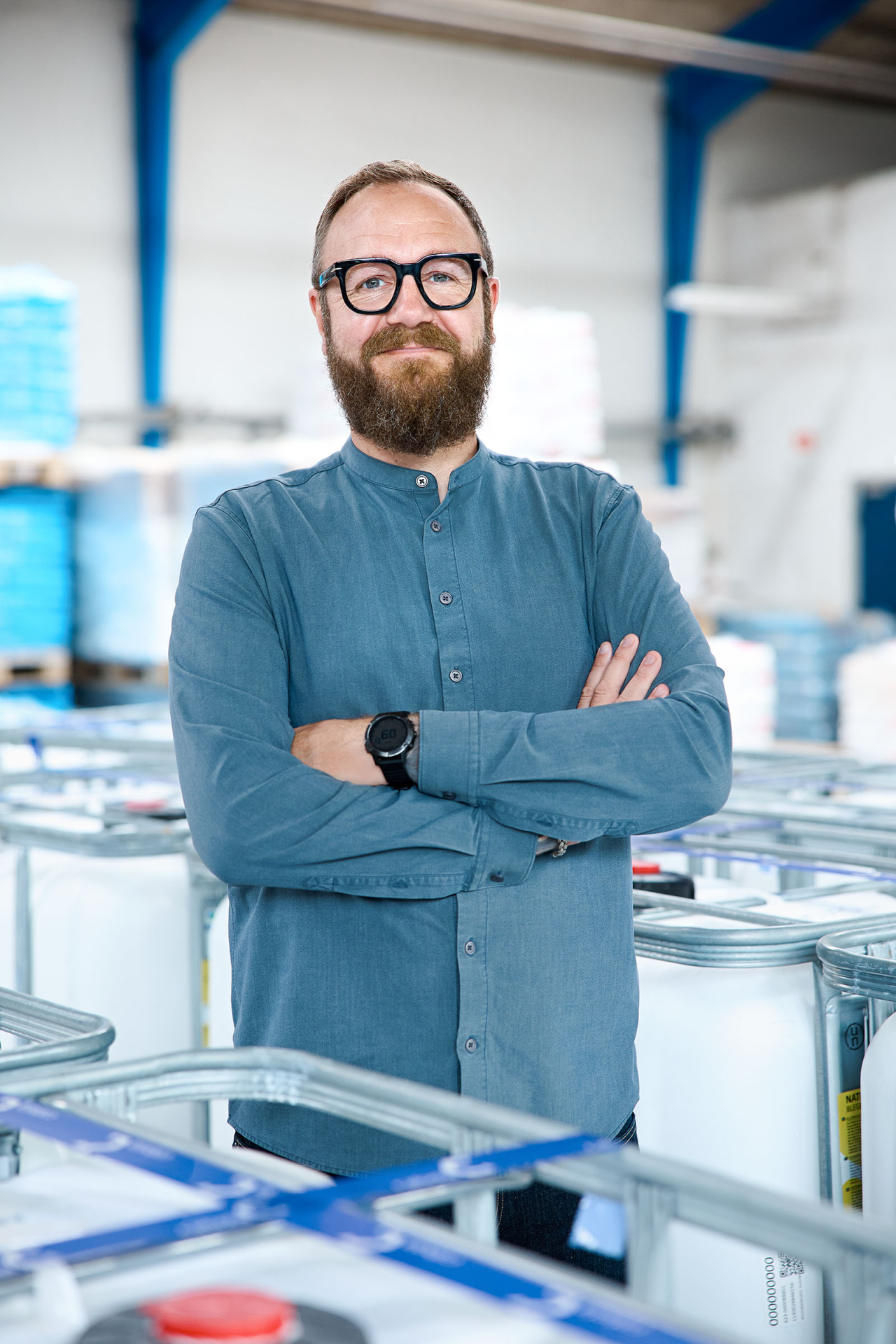
2 For Kenneth Laursen, providing customers with top-notch service is a key benefit that comes from deploying Micropilot FWR30.
A CLEAN POOL IS A SAFE POOL
Kenneth Laursen knows all about swimming pool water. His company, Cabola ApS, supplies close to 300 sites all over Denmark with the chemicals they need to provide clean swimming conditions for several hundred bathers at a time: primarily sodium hypochlorite solution and sulfuric acid, along with hydrochloric acid and cleaning agents. In water, sodium hypochlorite dissociates into hydroxide ions and free available chlorine. The latter not only inhibits algal growth but also oxidizes the dead skin cells, sweat and sunscreen washed from swimmers’ bodies – a chemical reaction that produces chloramines, the compounds that give swimming pools their characteristic ‘chlorine’ odor.
How frequently these chemicals need replenishing depends on multiple variables: temperature, the level of solar radiation and the number of people in the pool. Kenneth Laursen: “It also makes a big difference to chlorine consumption whether swimmers shower before entering the water.” That means the daily amount of sodium hypochlorite added may vary between 10 and 20 ml per cubic meter of pool water. As a result, Cabola’s customer resupply intervals are rather variable, which can lead to logistical inefficiencies. “Whenever the Vestbadet pool used to order from us, we’d phone around our other customers in the Viborg area to see if they needed anything,” Laursen explains. “But even then, our delivery truck
would often leave the depot half full. That’s something I wanted to change.”
Kenneth Laursen initially sought a solution by fitting his customers’ storage tanks with remotely monitored gauges. But this proved too expensive, and the immersion probes they used couldn’t withstand the corrosive chemicals. In the end, he found the solution to his problems at Endress+Hauser. Now there is a dashboard that gives Cabola employees 24/7 visibility into their 300 customers’ chemical inventories and consumption rates, providing the key to tailored replenishment.
“Having good, long-term relationships with my customers matters more than short-term sales.”
Kenneth Laursen,
director, Cabola ApS
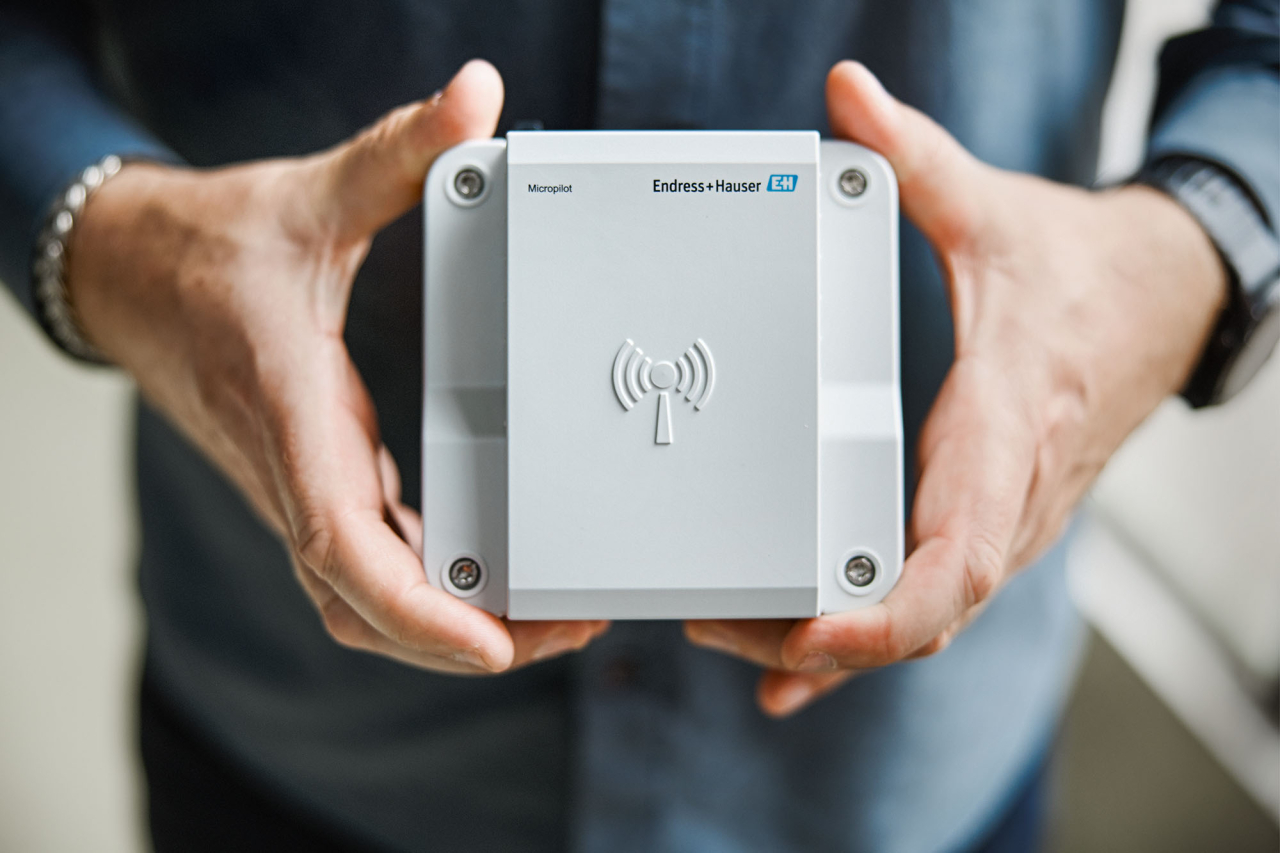
1 Micropilot FWR30 is batterypowered, compact and ready for action in mere minutes.
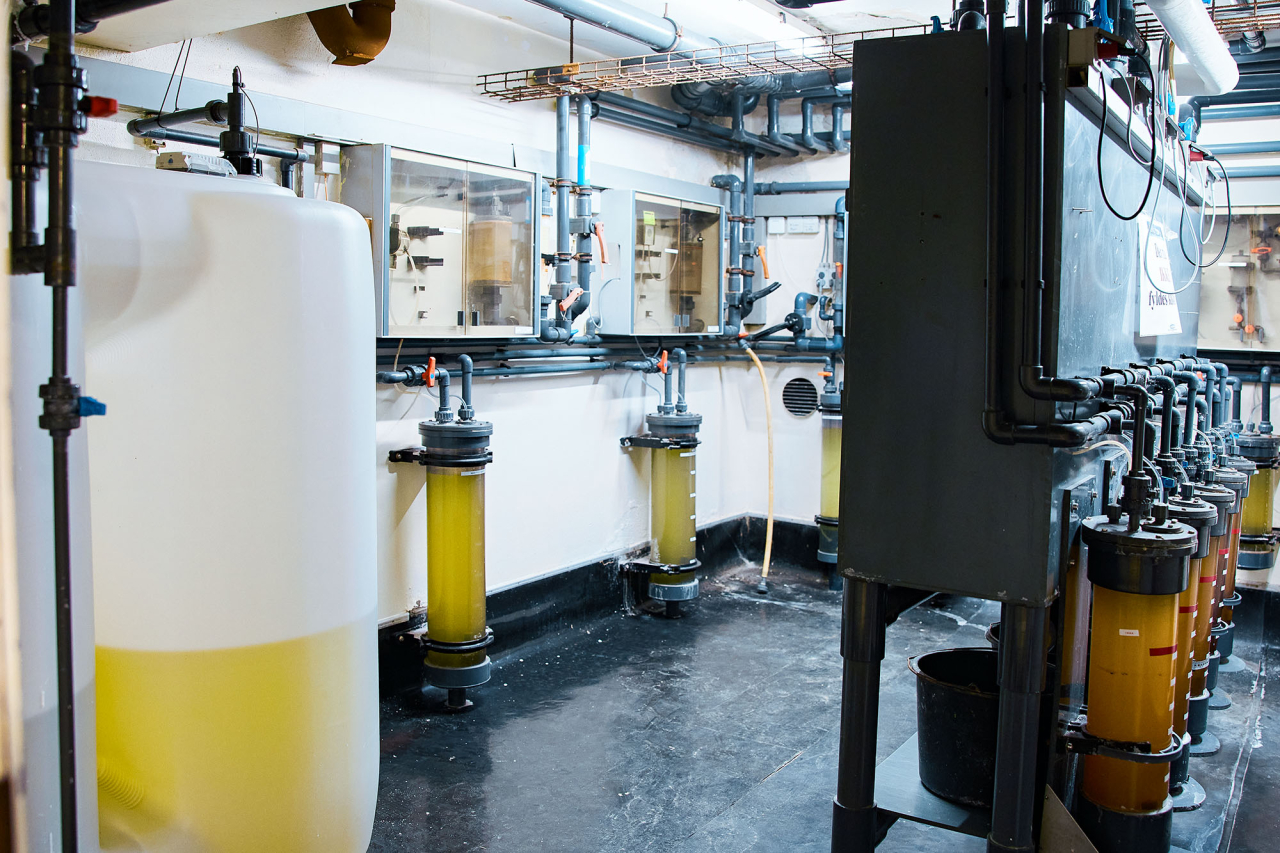
3 The sensor is mounted on the tank and measures level contactlessly by sending radar waves through its plastic wall.
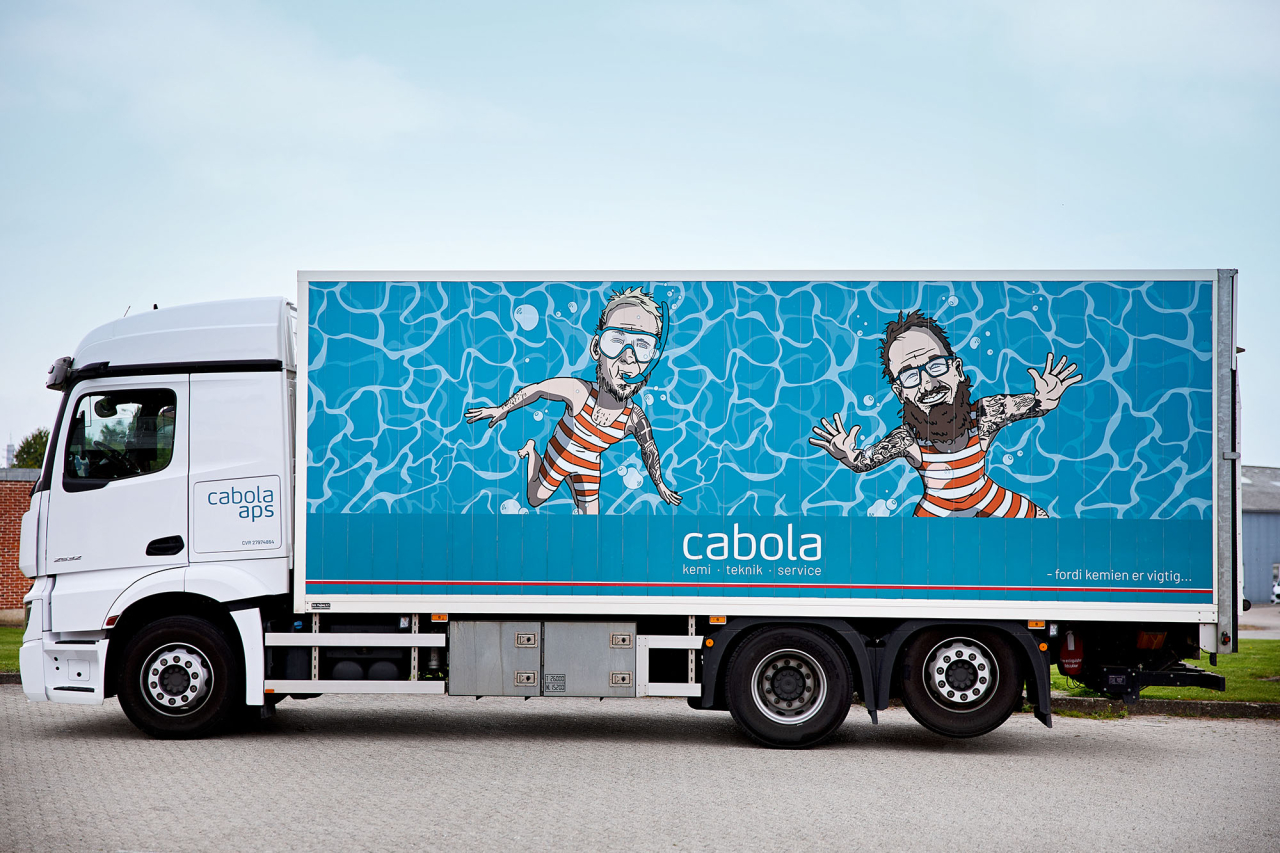
2 Cabola’s trucks use almost 10 percent less fuel thanks to optimized route planning.
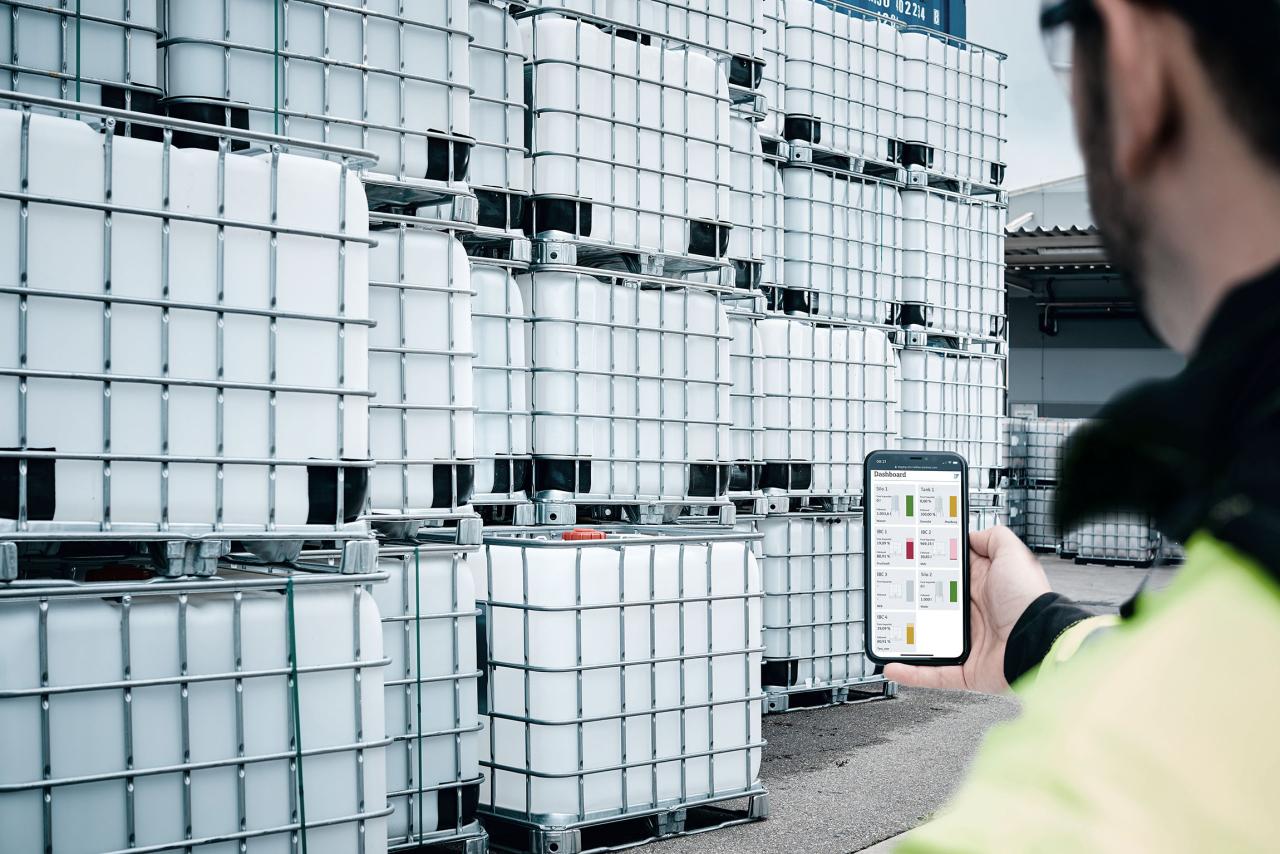
4 Intermediate bulk carriers (IBCs) are widely used in industry as an efficient way of transporting and storing liquids.
VALUABLE INSIGHTS
“The Cabola example shows how transparency can optimize logistics and inventory processes,” explains Christian Reichert, director of engineered solutions at Endress+Hauser. Transparency-enhancing solutions have indeed been widely used for many decades. “Financial performance and competitiveness in the process manufacturing industry are highly related to effective inventory management around materials storage, transfer and distribution,” Reichert says. High inventory levels improve suppliers’ ability to meet demand but tie up a lot of capital. Lean inventory levels, on the other hand, cut costs at the expense of the ability to deliver on demand. “That’s why companies use inventory management solutions: to find the right balance. It’s about making their processes more efficient and boosting productivity.”
For a long time, though, such solutions were not an option for operators like Cabola where the storage units are intermediate bulk carriers (IBCs) – stackable plastic containers with capacities ranging from 300 to 3,000 liters. Used in many industries for transporting and storing liquids, IBCs tend to be relocated frequently, often in quite far-flung places. “Conventional wired measuring systems are generally too complex and pricey for small installations or applications that don’t have overly stringent safety requirements,” explains Christian Reichert. “So, there was no cost-effective way to automate their measuring processes.” Gauging fill levels in smaller IBCs that move around basically meant making do with visual checks, periodic sampling or estimates.
But now, electronics miniaturization and cloud technology have come to the rescue. In 2019, Endress+Hauser launched its Micropilot FWR30 – a compact level sensor that sits on the tank’s exterior and sends radar waves through the plastic wall into its interior. The technology determines the level contactlessly using time-of-flight measurement. Power for the sensor comes from a lithium-ion battery that can last up to 15 years depending on measurement interval. The instrument has an inbuilt SIM card enabling access to the cellular network, which is used to transmit measurement data to the Endress+Hauser Netilion cloud – no gateway involved. From there, digital services visualize the data, so authorized users can monitor fill levels from any tank gauge out in the field.
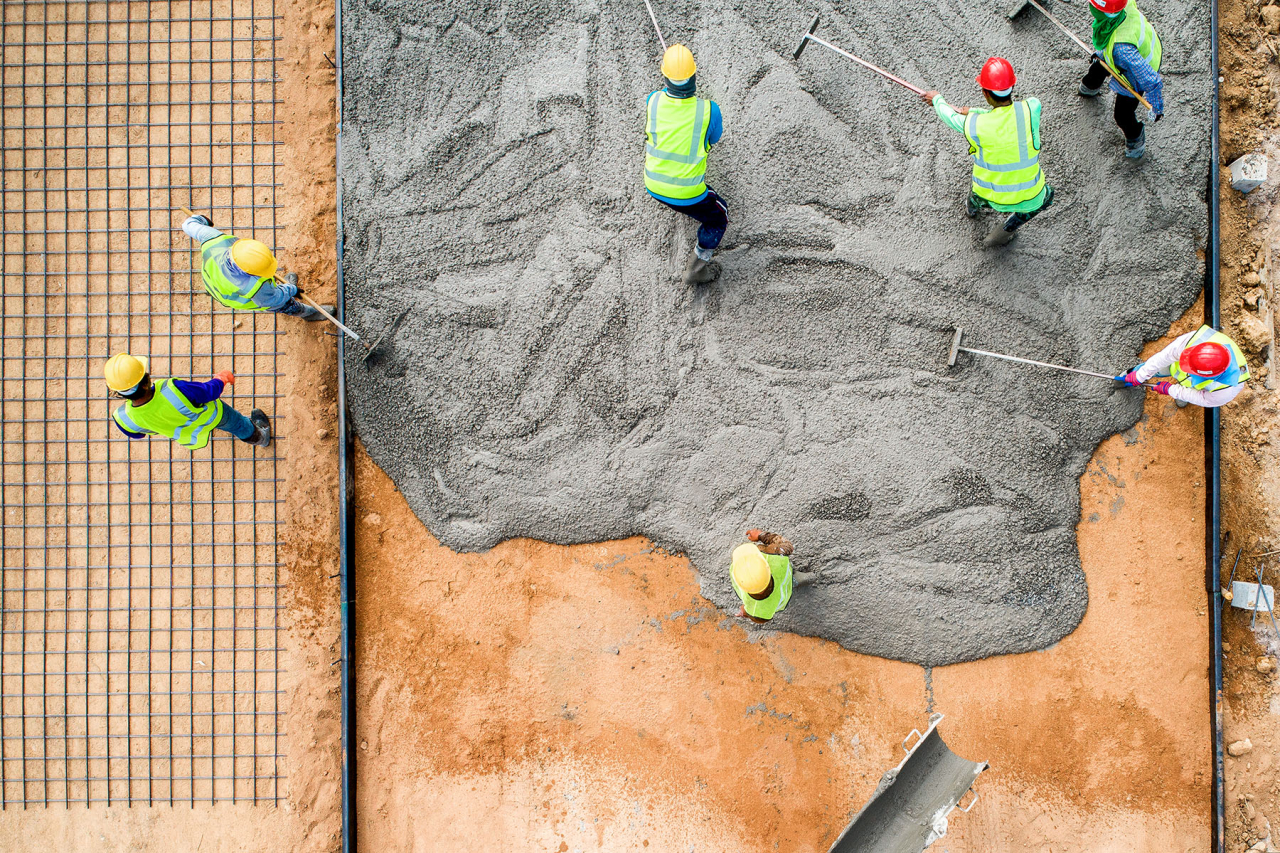
1 Construction sites need sufficient stocks of concrete plasticizer on hand at all times, otherwise work grinds to a halt.
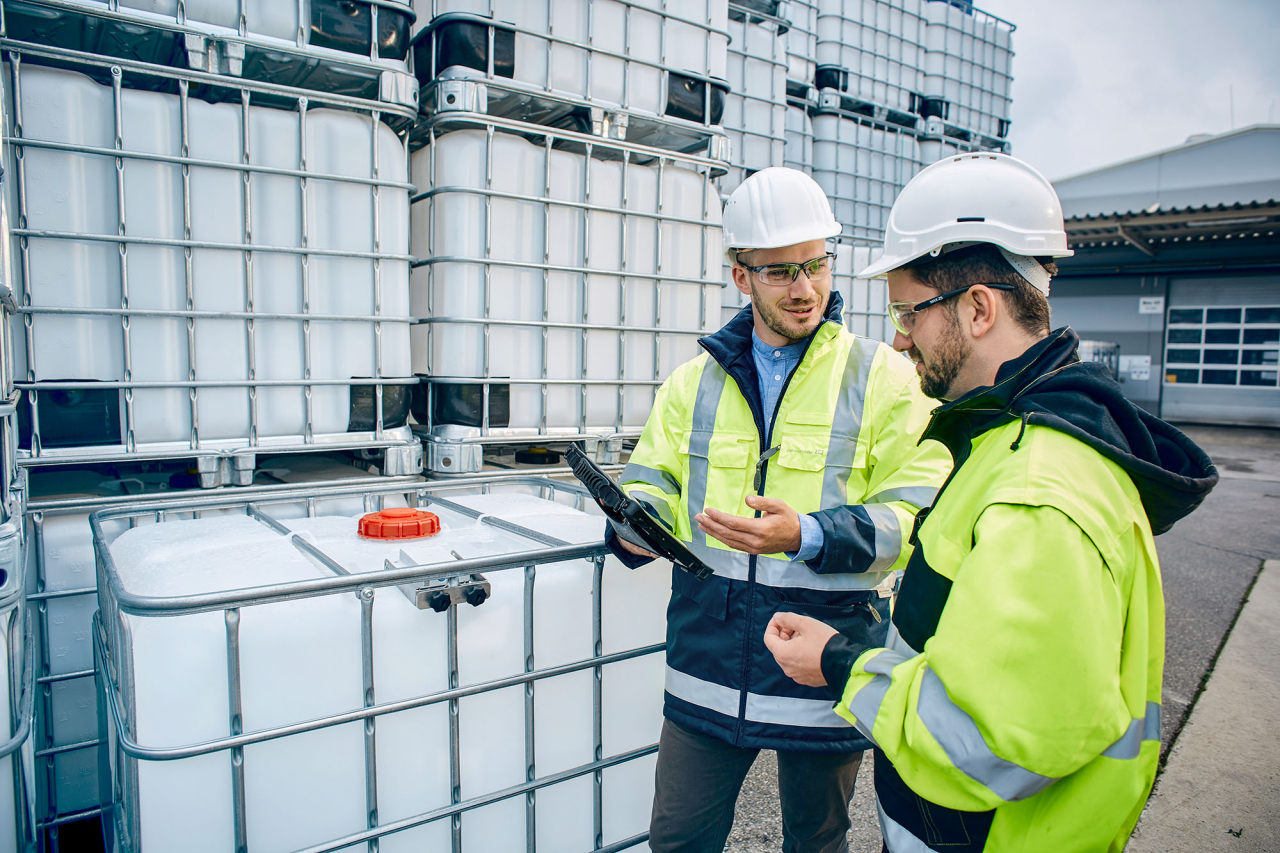
2 SupplyCare gives customers visibility into their inventory levels from anywhere, at anytime.
DATA FROM THE OUTBACK
This same solution also works in remote locations like the vast countryside that Australians call the outback, as Endress+Hauser international business development manager Volker Schulz explains. The customers he supports on this sparsely populated continent include a company that produces and supplies concrete additives to construction sites. The logistics of this can be quite challenging. “If the concrete plasticizer runs out, the building site grinds to a halt until fresh supplies arrive from a thousand kilometers away.” On the other hand, early reordering just to be sure can be equally problematic, because every truck trip into the outback for anything less than a full tanker load of chemicals is bad for profitability and sustainability.
The company now has several hundred FWR30 sensors in use across various countries and uses the Endress+Hauser SupplyCare cloud-based inventory management platform to give its customers 24/7 access to dashboard maps revealing information about each of their tanks. This digital service does more than monitor tank levels; it also tells the customer whether the stored product has been withdrawn from a tank and processed at the right temperature – an important parameter in places where temperatures can rise to 50°C. Additionally, the system generates short-term forecasts based on monitored changes in tank levels. “Any fall below a set level will trigger an alert or automatically initiate a replenishment order,” Schulz explains. This eliminates the risk of empty tanks and stop-start construction work.
“Micropilot FWR30 brings transparency to a whole host of new applications and improves decision-making.”
Volker Schulz,
international business development manager for inventory management solutions, Endress+Hauser
THE PANDEMIC AS A CATALYST
The pandemic has driven further refinements to this technology. Christian Reichert: “The delivery problems encountered during the pandemic and growing expectations around sustainability have made companies even more aware of transparency as a factor. Customers now also want the ability to monitor their supply chains, from small segments to the entire thing. We’re seeing strong demand here, particularly in the construction materials sector.” Endress+Hauser responded by working closely with users to extend Micropilot FWR30’s functionality. The instrument now has a process connection for metal tanks and silos – to allow for the fact that radar beams can’t penetrate metal walls. In addition, it can now measure bulk solids and has locationtracking capability.
One of the customers involved in developing all these innovations was Profibaustoffe Austria GmbH, a company that processes limestone from its own quarry into cement, mortar and render for walls, floors, facades, gardens and road construction. Supplies of these materials leave the company base in Ernstbrunn, Austria, destined for construction sites around the country and across the border in Eastern Europe from its base in Ernstbrunn, Lower Austria. The transport containers are cylindrical steel silos that can be swapped out or refilled as required. Even empty, the silos are quite valuable, so it’s worth knowing their location at any given time. And that’s where Micropilot FWR30’s GPS function comes in. The technology also helps with route planning.
15years
– Micropilot FWR30 level sensor’s maximum battery life, depending on measurement interval.
FROM LIQUID TO SOLID
But first things first: before the cloud-based sensor could be any use at all to Profibaustoffe, it had to be adapted for solid construction materials. While radar technology is ideal for gauging the level of liquids, it doesn’t work so well with solids like dry building mixes because the reflected signal is weaker. Measuring values can be further skewed if the silo contents form a crater when material is removed, or a cone when material is topped up. So, using measurement data from field tests, the Endress+Hauser team linearized the signal and optimized the sensor for measuring bulk solids. Using material-specific conversion factors, the system’s software automatically processes the resulting level data to calculate how many tonnes of mortar or mix are in the silo.
Christian Kreitzer, shipping director and deputy sales manager at Profibaustoffe Austria GmbH, is delighted with the outcome: “Together with Endress+Hauser we developed and implemented the perfect solution for level monitoring in silos. The cooperation worked really well, and we are very satisfied with the result.” Thanks to the solution’s web-based inventory management software, the company always has total transparency across all stages of its supply chain, from production and distribution through to storage on construction sites. This makes for optimized delivery routes, which in turn lower operating costs and reduce the company’s carbon footprint. The FWR30 has a further function that the team at Profibaustoffe Austria really likes: a sensor that can track changes in silo orientation. This is useful because the silos are transported horizontally and tipped to vertical on arrival at the construction site. In effect, the sensor provides definitive documentation of the company’s on-time delivery performance.
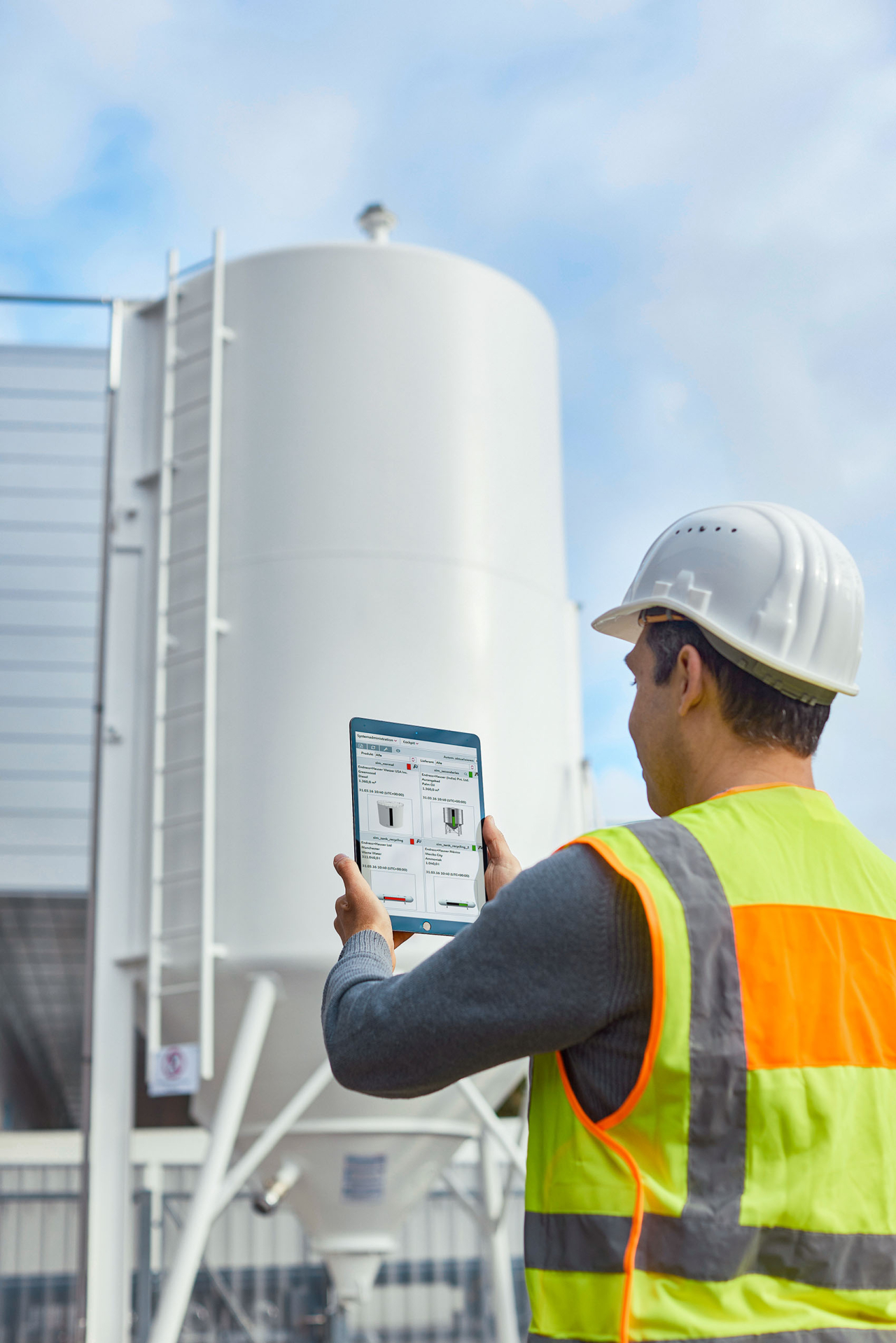
1 Measurement data is uploaded via cellular network to the cloud, where it is available 24/7 even to people on the go.
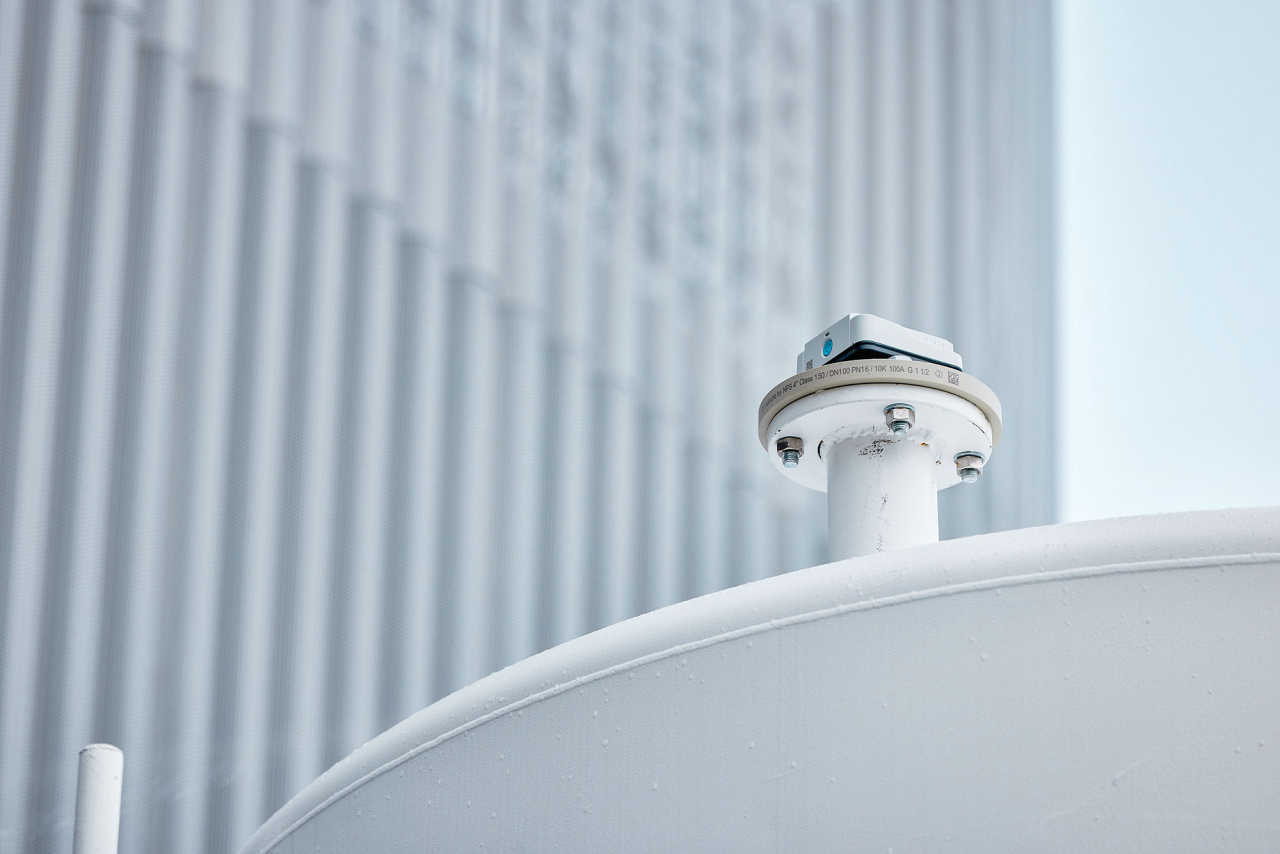
2 For metal silos, the sensor attaches using a process connection.
IMPROVED RELATIONSHIPS WITH CUSTOMERS
Thanks to Micropilot FWR30, the producer and supplier of concrete additives in Australia has even developed a new business model. The company now manages its customers’ inventory, guaranteeing that they will always have enough plasticizer in their storage tanks. And in Denmark? Kenneth Laursen has achieved his goal of optimizing truck capacity utilization, cutting fuel consumption by almost 10 percent. And he, too, is leveraging this new technology to strengthen relationships with his customers: “If outdoor swimming pool operators contact me to order replenishment chemicals in late summer, I’ll gladly advise them against that if their current usage patterns indicate that existing stocks will last through to the end of the season,” he explains. “My customers really value that. For me, having good, long-term relationships with them matters more than short-term sales.”
15meters
– the sensor’s maximum measuring distance.
Published 03.12.2024, last updated 09.12.2024.
Dive into the world of the process industry through new exciting stories every month with our «changes» newsletter!
Subscribe to newsletter