A solid bond
Raffinerie Heide and Endress+Hauser have been business partners for more than 20 years. What unites the companies is the resolve to continuously develop themselves and find ever-better solutions for even the most complex processes.
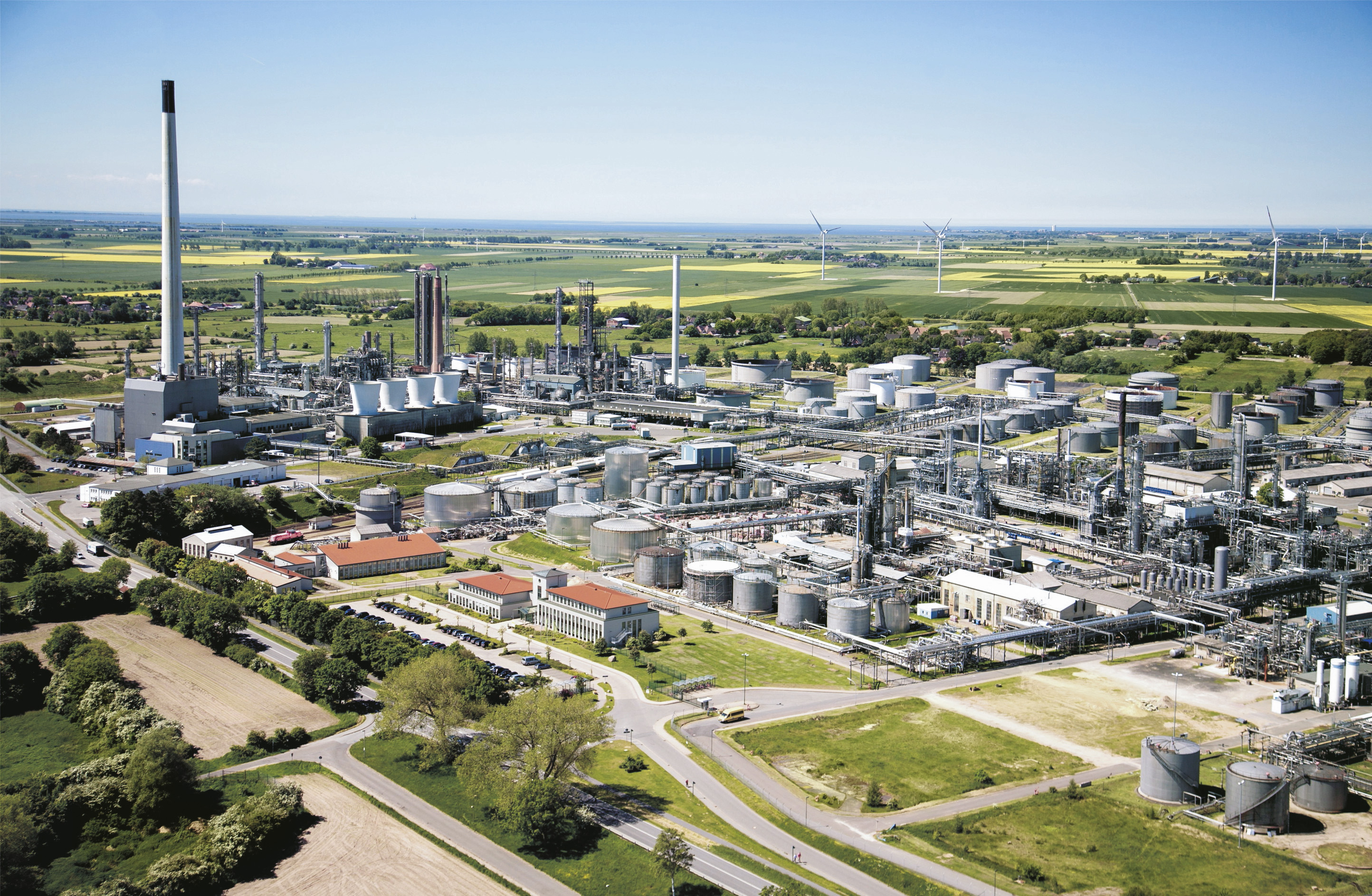
PARTNERSHIP
Board a plane in Hamburg and you can be fairly confident that it will take off with kerosene produced by Raffinerie Heide. Based not far away in Hemmingstedt on the North Sea coast, each year the company converts four million tonnes of crude oil into fuels and petrochemical products for customers across northern Germany. Although the refinery site is more than 80 years old, it is one of the most advanced and flexible in Germany today. “We keep investing heavily in plants and processes as we adapt to innovations, plus we continuously improve our processes,” say Klaus Behrens, Head of Engineering at the refinery.
Raffinerie Heide set a course for the future in 2000 by completely modernizing the site and installing a new hydrocracker, which is the heart of the refinery. The hydrocracker converts crude oil into intermediate fuel products, helped by hydrogen and catalysts under pressures of up to 200 bar and temperatures as high as 430 degrees Celsius. Compared to other European refineries, the process used in Hemmingstedt achieves an especially high product yield.
Some of that achievement comes down to Endress+Hauser. “As part of the modernization project we installed several thousand measuring points, in particular for flow, pressure and level,” says Torsten Hoppe, a technical sales representative for Endress+Hauser who manages the Raffinerie Heide account. In 2010 Endress+Hauser played a further part in the hydrocracker by supplying multipoint thermometers. “Endress+Hauser was still new to the temperature measurement business at the time the hydrocracker was installed,” says Sönke Lahann, instrumentation engineer for the hydrocracker. “That’s why we didn’t get them involved until later. Another decisive factor was that Endress+Hauser offers support in our region.”
DUAL-PROTECTED SENSORS
Multipoints use individual thermo elements integrated into cable probes to perform three-dimensional temperature measurements in the hydrocracker’s reactor beds. This permits monitoring and optimal control of the process. But one year after installation, a problem arose: in one of the systems, process gas had seeped into the diagnostic chamber. “We were quickly on site,” recalls Peter Prokesch, Head of Marketing Technology Division at Endress+Hauser.
The two companies put their heads together to find an immediate solution, but they didn’t stop there. “We went on to develop another sensor design together with the refinery and installed the new system during the hydrocracker’s next scheduled downtime,” says Peter Prokesch. Close collaboration in this area continues to this day. Raffinerie Heide recently started using innovative iTherm ProfileSens technology after a field test lasting more than two and a half years. “The technology allows us to combine multiple thermo elements in a single cable probe and also provides them with a second protective layer,” explains Pietro Miceli, Product Manager at Endress+Hauser. Not only is there more space in the reactors for the catalytic converter, most importantly it improves sensor reliability.
Why is the refinery heading down this path with Endress+Hauser? “We joined together because Endress+Hauser was very interested in tackling the issues and finding solutions,” explains Sönke Lahann. “Measurements inside the hydrocracker are especially demanding given the difficult process conditions.” The partners are a well-coordinated team in other areas too. “Endress+Hauser is attentive, and we are always in close communication,” says Steffen Raabe, the instrumentation engineer responsible for tank storage and loading. “If a new or general question arises, we inquire as to whether a solution can be offered or jointly developed.” In addition, the salespeople are intimately familiar with the site and approach the refinery with ideas for further innovations. “We achieve the goals together,” says Steffen Raabe.
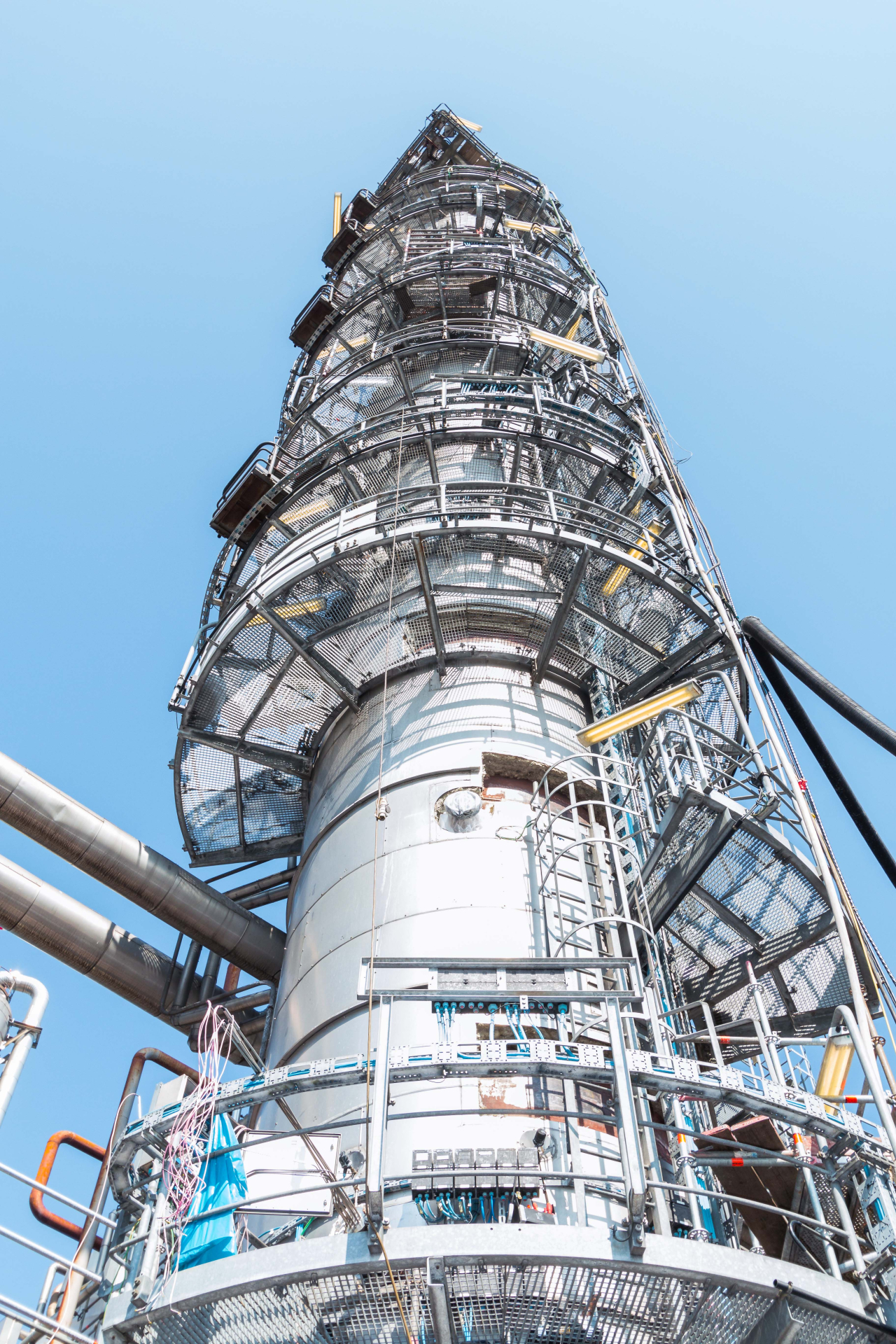
The heart of the facility is an ultramodern hydrocracker.

Endress+Hauser and the refinery jointly enhanced the multipoint thermometers in order to improve the process inside the hydrocracker. The system was installed during scheduled downtime.
THE RIGHT SPIRIT
For Klaus Behrens, partnerships like the one with Endress+Hauser are crucial in helping to shape a successful future for the refinery. “Since our plants run continuously for years without downtime, the technology’s quality, durability, reliability and availability matter greatly. But there also has to be a good fit at a personal level. We expect our suppliers to provide us with expert advice regarding what is possible in terms of innovations – not only today, but in the future as well,” adds Behrens.
Digitalization and the energy transformation are the major issues currently occupying the minds of management at the refinery. “We want to make greater use of data from the field for further automation. To include more remote areas of the facility, we use field multiplexers and technologies such as Wireless HART to transmit information from the existing installation,” says Steffen Raabe. The location is also participating in Westküste 100, a project directed at establishing a regional hydrogen economy and financed by the German Federal Ministry for Economic Affairs and Climate Action. The plan is to set up a 30-megawatt electrolyzer powered by renewable energy on the refinery site to produce green hydrogen, which will then feed directly into the hydrocracker and take decarbonization of the heart of the refinery a step further. “Endress+Hauser understands our needs in this area too, and can provide optimal on-site support,” says Steffen Raabe with confidence.
Published 25.07.2023, last updated 14.08.2023.
Dive into the world of the process industry through new exciting stories every month with our «changes» newsletter!
Subscribe to newsletter