Smart Water
Supplying water is a mammoth task in the Philippine mega-metropolis of Manila. Maynilad tackles this challenge with intelligent data models and steady digitalization of its infrastructure.
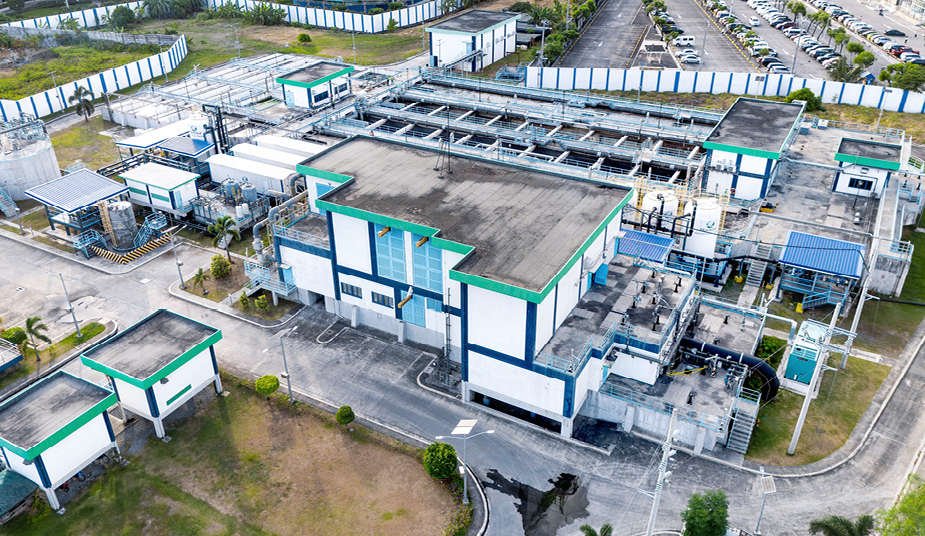

1
Clean water for Manila: The Parañaque water treatment plant is Maynilad’s largest water reclamation facility.

3
Ivan Louie Villar (left) is the first point of contact for Maynilad at Endress+Hauser.

2
Maynilad’s area of responsibility is growing just like the megacity of Manila.
Dr Francisco Castillo looks at his laptop, skimming over a couple of figures on the dashboard. “It will be drizzling in Quezon City around noon tomorrow.” At first glance it might be surprising to discover that the senior vice president and chief information officer of the largest water provider in the Philippines is occupied with weather forecasts. But data like this is in fact part of the business model at Maynilad Water Services Inc. (Maynilad). “We began to pay more attention to the weather two years ago. Now we can precisely predict the water levels in our reservoirs or determine if we can draw water from them,” explains Dr Castillo. The company draws its raw water primarily from Angat Dam and the country’s largest lake located in southeast Manila.
Francisco Castillo and his team even installed their own weather stations to create more precise forecasts. Each station features a solar panel, wind vane, rain gauge, temperature sensor and an anemometer, which transmit their information via a satellite link. The reason is simple, as Francisco Castillo explains: “No one collects weather data at our water sources in the mountains.” Finding its own solutions, even far removed from the company’s own plants, is just part of the Maynilad way of doing things. The company has consistently pursued a strategy for 10 years that involves digitalizing the operational technology (OT) at all plants and connecting it with the information technology (IT). Maynilad thus wants to fulfill its mission even more efficiently: managing the water and wastewater for 10.3 million residents in the cities and communities of the western Manila metropolitan area.
“If we can solve a problem faster with AI and remain within the cost framework, we will use it.”
Francisco Castillo,
senior vice president and chief information officer at Maynilad
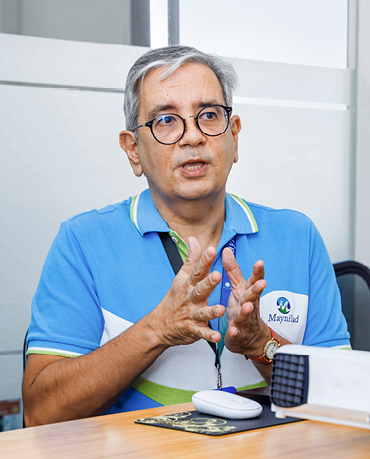
186million
liters of water are treated every day in the Maynilad plants
Everything under control
A visit to the Maynilad control center in Quezon City, which belongs to the Manila Metropolitan Region, reveals just how valuable this work is. The room is filled with silent concentration. With ergonomic chairs in front of large monitors displaying a wealth of information, it feels like a command bridge. Small red warning lights blink occasionally on digital maps. From this room employees monitor the entire Maynilad network around the clock. The system encompasses five water treatment plants, dozens of pumping stations, wastewater plants, reservoirs and over 7,500 kilometers of pipes. The entire operation is highly automated. The employees intervene only if there’s a malfunction or if action is required, such as when an area experiences a loss of pressure and water has to be diverted from another area.
Pointing to a monitor, Francisco Castillo says: “We must be able to analyze where we are losing water because of leaks or illegal water connections. The data collection is an enormous help.” The impact of the continuously advancing digitalization is even greater, however. “We’re in a position to view the status of all assets in our plants, nearly all of which are online in real time: pumps, drives, valves and of course the measurement devices that include sensors for flow, level, pressure, temperature and liquid analysis. They generate a lot of data, often every second or millisecond. We can access this information from any smartphone as needed.”
Pandemic as a catalyst
The reason the company chose this path early on has a lot to do with Francisco Castillo and also with the measurement technology from Endress+Hauser. The catalyst for change can be traced back to 2011. “The term Industrial Internet of Things was barely established at that time. There was no integration of the IT and OT platforms. That made it difficult to obtain information from the operating systems in the plants,” recalls Dr Castillo. In those days Maynilad engineers drove from plant to plant, collecting data with USB sticks. That caused delays in detecting problems.
After Maynilad took over a plant from a contract partner with incomplete documentation, Castillo’s team made a decision to manually digitalize all of the important technical information and create a central storage location in the process. “Our thinking was, why not collect all of the technical data in one place? We developed our own IIoT platform from this idea.” In terms of implementation this meant equipping each plant step by step with edge devices, which forward data that is as clean as possible. All told, it adds up to more than 300,000 individual data points that provide measurement values, status notifications and much more. According to Castillo, the majority of the platform users are engineers. “We make the technical platform available, including the data. Users then create their own dashboards because they know best what they need.” The platform supplies data that is used in the control center and facilitates operations.

1
Via an IIoT platform, Maynilad presents plant and process data on dashboards. Here in the central control room, a team monitors all plants around the clock.

3
Many Maynilad systems run completely automatically and send data to the system in real time.
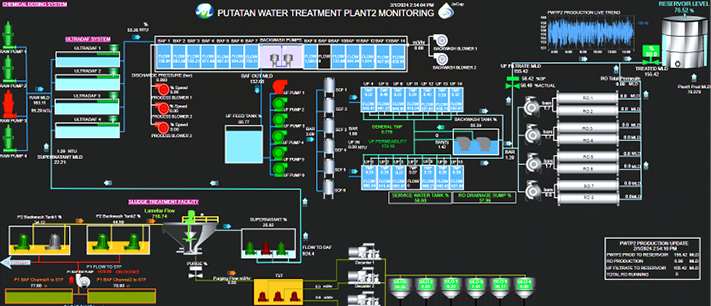
2
Users receive relevant information on their dashboard, e.g. water quantities or status data of individual instruments.
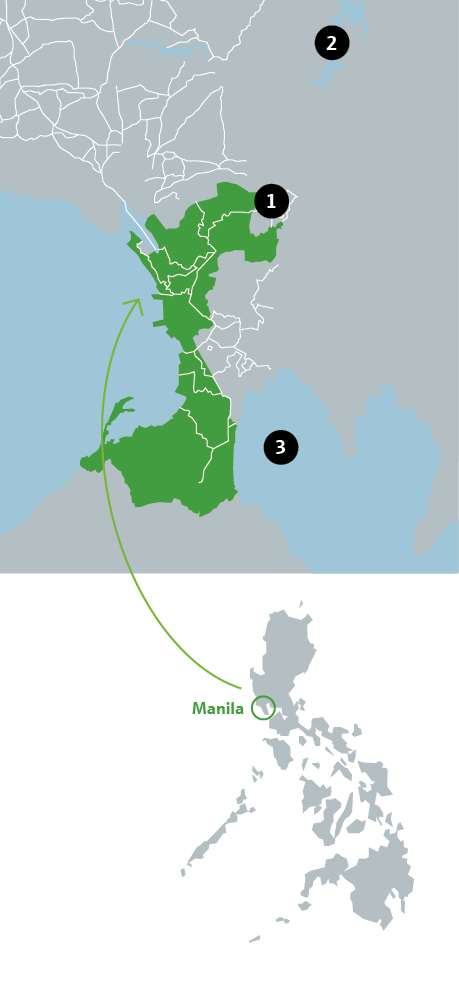
Green = Maynilad area of responsibility
1 Ipo Dam
2 Angat Dam
3 Laguna Lake (largest water resource)
Measurement technology creates solid data basis
Reliable, high-quality data serves as an indispensable source of information for the analysis, which in turn calls for reliable measurement technology. Kim Rean Estrada, head of facilities maintenance for wastewater at Maynilad, explains: “Our plan consists of automating and digitalizing all plants, from north to south, and connecting them with our control center.” Endress+Hauser plays an important role here because the company’s devices are reliable, consistently supply precise measurement values and thus create no data leaks, an enormously important foundation for the water supply system.
Malfunctions have to be resolved quickly. “Electrical and measurement equipment that lack local support are currently the cause of the biggest issues. But in the case of Endress+Hauser, support and spare components are always available,” explains Estrada. This is why Maynilad has already installed around 1,000 Endress+Hauser devices across the entire product portfolio: flow, pressure, level, temperature and liquid analysis technology.
This also applies to the Parañaque water reclamation facility, Maynilad’s largest sewage treatment plant. It bundles several wastewater streams, which undergo a series of purification processes before being discharged into the environment.
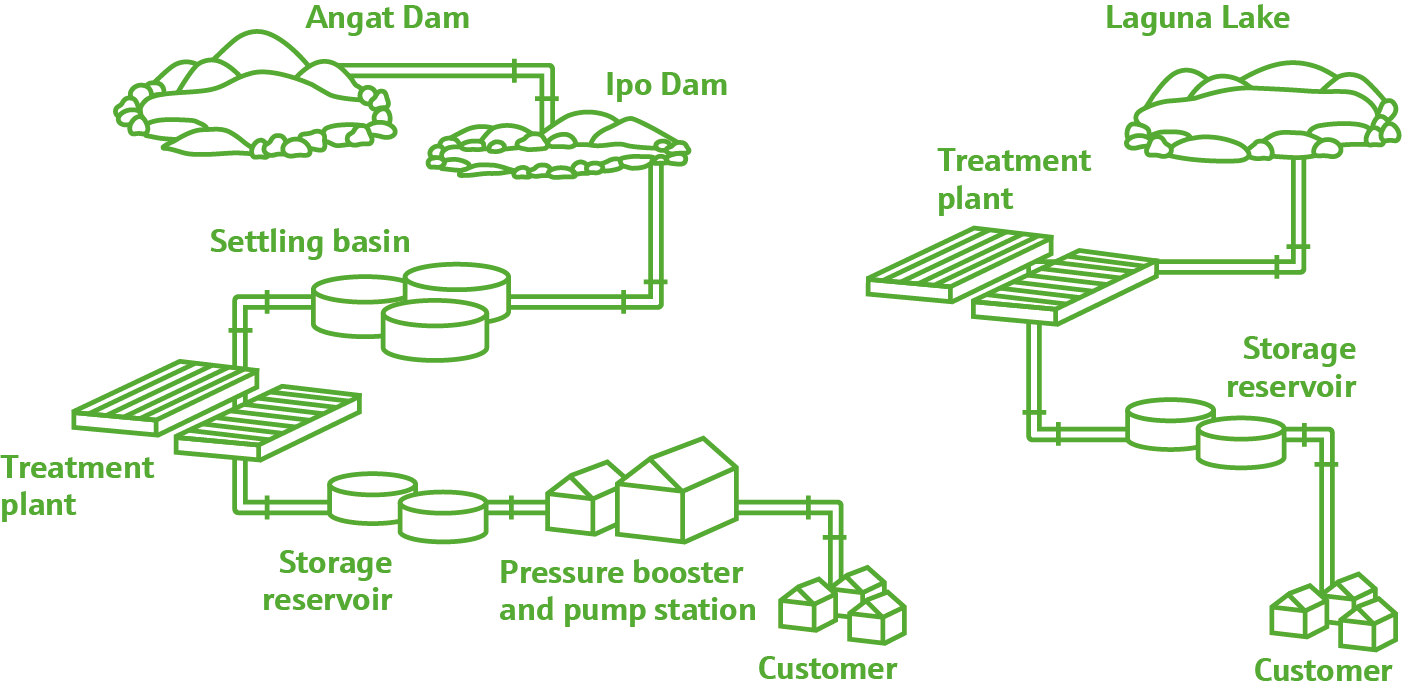
“In the case of Endress+Hauser, support and spare components are always available.”
Kim Rean Estrada,
head of facilities maintenance for wastewater at Maynilad

The measuring devices from Endress+Hauser run reliably, generate an abundance of data and can communicate digitally
Jerahmeel Andrew Layco, head of automation and instrumentation design, stands on a metal bridge above one of the treatment tanks in the midday sun and talks about how much he values Endress+Hauser’s innovative strength. “Most of our measurement parameters are covered, plus Endress+Hauser is constantly working on new developments.” He cites the ‘0 x DN full bore’ technology as one example. This innovation enables the installation of electromagnetic flowmeters in extremely tight spaces where the instruments do not require the usual distance to the next pipe bend. “It’s the perfect solution for our tightly spaced plants,” says Jerahmeel Andrew Layco. Since all of the instruments feature digital communications, Endress+Hauser is the partner of choice, especially for all new Maynilad plants.
If Jerahmeel Andrew Layco wants to discuss new developments or services, he gets in touch with Ivan Louie Villar, the first point of contact for Maynilad at Endress+Hauser in Manila. The business development manager believes Endress+Hauser’s intelligent field devices with Heartbeat Technology can lead to further opportunities for increasing efficiency at Maynilad, a company that is open-minded about new technologies. “Heartbeat Technology performs self-checks in the background and reports the status of the instrument. The functionality of the device can also be verified at the touch of a button at anytime. No one has to be on site and downtime is prevented.”
> 1000
Endress+Hauser instruments are in use in Maynilad plants

10.3million
people in the Manila metropolitan area receive their water through Maynilad
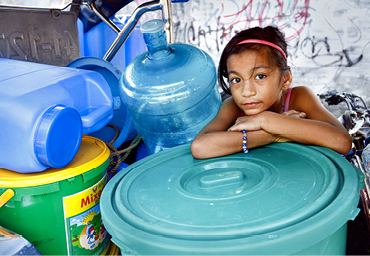

Thanks to data analyses, the water company can identify whether and where water is being lost in the metropolis, e.g. through leaks or illegal connections.
Transparency and efficiency gains
Automation and connectivity via the IIoT platform furthermore bring benefits in terms of sustainable water management. “We utilize Endress+Hauser instruments for optimizing the chemical treatment of wastewater or for adding oxygen, which is energy-intensive. This helps us conserve resources. And remote control of the pumps can only be carried out with the help of connected pressure sensors. Thus, via the IIoT platform, the pumps can be controlled as needed,” says Dr Castillo.
This prompts the question: could the use of AI lead to even more efficiency? After all, Maynilad has been collecting technical data for 10 years, an ideal prerequisite for employing AI models. Francisco Castillo, who wrote his dissertation on the subject of AI around 30 years ago, adds: “You should always think about things from the perspective of the problem. AI can be the solution, but in our case our initial focus is the IIoT platform.” Nonetheless, the company is already relying on machine learning for predictive maintenance as an example. The CIO emphasizes that even more data and processing power are required to train a large-scale generative AI model. “If we can solve a problem faster with AI and remain within the cost framework, we will do that.”
AI is already more firmly established in the area of customer service. Chatbots that operate on the basis of large language models should relieve the workload of call center agents in the near future. According to the CIO, cybersecurity is another interesting area where AI is employed to recognize hacking patterns and protect the system as a result. Francisco Castillo closes his laptop. “It’s a good thing that we began to collect and process data at an early stage,” says the CIO in summary. “And it’s important to have partners like Endress+Hauser at our side who supply the right hardware and understand the IT aspect at the same time.”
Published 16.05.2024, last updated 18.06.2024.
Dive into the world of the process industry through new exciting stories every month with our «changes» newsletter!
Subscribe to newsletter