Simulate, then build
Nearly every Endress+Hauser instrument is developed with the help of computer simulation. That not only leads to outstanding product characteristics but also takes the innovation process to a new level.
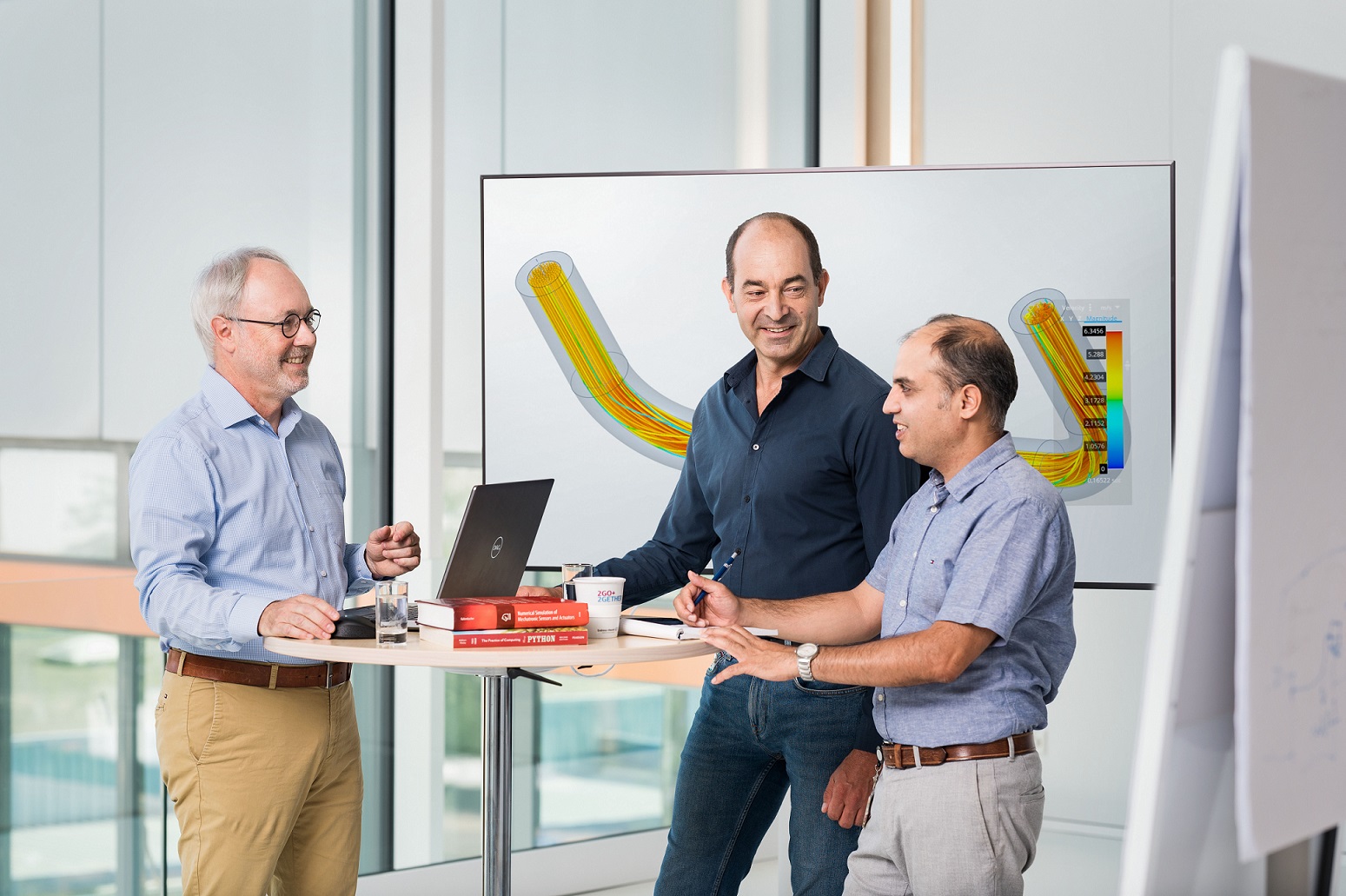
DEVELOPMENT
Take a typical application in the water or food industry: flow needs measuring at a specific place in the plant, but there is a bend in the pipe just upstream or downstream of the measuring point. The liquid develops vortices and turbulence, and hence doesn’t flow smoothly through the instrument as the sensor expects. This throws measurement results out of kilter.
For a long time, to deal with such flow disturbances plant operators had to either adhere to the recommended inlet and outlet distances or deploy an instrument with a restricted measuring tube. Since 2020 Endress+Hauser has offered an instrument that supplies precise measurements independent of the inlet conditions. The Promag W, with the 0 × DN full bore option, is the world’s first electromagnetic flowmeter that consistently supplies correct measurement values regardless of the flow profile. The instrument was developed with the help of numerical simulation.
THOUSANDS OF VIRTUAL PROTOTYPES
Numerical simulation is about modeling a measurement using numbers within a computer, and then testing the model under a variety of parameters. “With this method we are pushing into innovative product development territory that once seemed unreachable and which can no longer be done by conventional means,” says Dr Wolfgang Drahm, who heads up a 20-person team of preliminary and fundamental developers at Endress+Hauser Flow. With this approach, the computer model is only representative of the specific problem being addressed – never the whole instrument itself. “Flow simulation requires a different model compared to when you are calculating an instrument’s vibration or magnetic properties,” explains Wolfgang Drahm.
With the model created, you can then simulate countless designs and potential problems. How do different tube diameters affect the flow? What are the impacts of pressure rating, viscosity of the medium or disruptors such as a 90-degree pipe bend immediately upstream of the instrument? “We know how an instrument will behave even before it takes physical shape,” says Dr Vivek Kumar, who champions the topic of simulation within Endress+Hauser as principal expert on the subject. The wealth of parameters in today’s process industry is no longer capturable using simple paper, pencil and equations.
Instead, computers run through thousands of virtual prototypes before the first physical instrument is built. “We can use simulations to advance instrument designs to the point where the instruments are increasingly robust against disturbances,” explains the fluid mechanics specialist. That was the case for the Promag W with no inlet and outlet runs. “That such a device is even possible stretched our imagination,” adds Wolfgang Drahm. Indeed, the optimal solution lay within a very narrow window. “We were able to pinpoint this unique zone aided by the computer, which tested everything in accordance with ideas and specifications from the development team.”

MAN INSTRUCTS MACHINE
Virtual developments such as these are made possible by growth in computing power, increasingly userfriendly software and surrogate models. The latter augment the numerical simulation with the help of mathematical correlations and machine learning. “Whereas in fluid mechanics we can run hundreds of numerical simulations over the weekend, we can optimize yet thousands more designs automatically using surrogate models.”
“Many of our innovations would not be possible without the close symbiosis between simulation and experiment,” emphasizes Dr Alfred Rieder, who heads up a unit at Endress+Hauser Flow tasked with the fundamental development of Coriolis flowmeters. Simulation provides the development engineers with breathing space to perform their actual tasks. “We can fully dedicate ourselves to the physical issues while the computer calculates the scenarios,” says the expert. And this is exactly where the human factor is needed. “Computer simulation is not difficult. What’s difficult is teaching the computer what a good instrument is.” Only when the human precisely understands and specifies the important factors can the machine do its job properly.
Published 25.01.2023, last updated 13.02.2023.
Dive into the world of the process industry through new exciting stories every month with our «changes» newsletter!
Subscribe to newsletter