Shrinking the footprint
Endress+Hauser aims to gradually decarbonize its portfolio over the coming years. But how is that possible when you need steel to produce your measuring instruments?
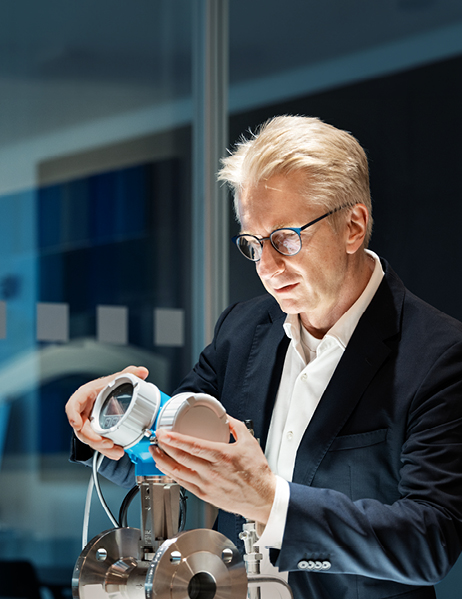
PORTFOLIO
Talk to manufacturing companies about their climate strategies and you will frequently hear them explain that most of their carbon emissions arise along the supply chain. “Endress+Hauser is no exception,” says Hans Joachim Fröhlich, director of technology and portfolio. “Our environmental footprint is for the most part attributable to the large quantities of steel and aluminum that go into our measuring instruments.” In collaboration with the company’s product centers, his aim is to reduce these emissions with a view to decarbonizing Endress+Hauser’s portfolio by 2050.
The simplest solution exists only in theory. “Were a financially appealing global market for green steel to emerge in the foreseeable future, we could convert our production immediately,” Fröhlich says. But climateneutral manufacturing of that raw material is still at the pilot stage. To complicate matters further, the speed with which capacities can be ramped up depends on the availability of green electricity and hydrogen. “That’s why we are looking for other ways to improve our products’ carbon footprint, using things that we can rapidly create and implement ourselves,” Fröhlich adds.
Some ideas are based on material savings through design. Modifying the sensors themselves is all but impossible because of the need to ensure accuracy and reliability. “However, you could remove the display from measuring devices that can be accessed wirelessly,” Fröhlich says. “Another option is to further miniaturize packaged electronics.” In flow and level measurement, Endress+Hauser has for some time been increasing the use of two-wire technology in measuring instruments: relative to four-wire, it needs less power to operate and fewer electronic components.

Looking at the big picture: Hans Joachim Fröhlich, director of technology and portfolio, is pursuing various ways to improve the carbon footprint of measuring devices.
MOVING TO MODULAR DESIGNS
The circular economy is an additional focus of attention at Endress+Hauser. “Our instruments already have long service lives of 15 to 20 years, and our main goal is to continue extending that,” Fröhlich says. Again, the instruments’ electronics can play a part in these efforts, since they don’t last as long and are more prone to technological obsolescence than sensors and mechanical systems. As one example, the latest generation of the Proline 300/500 transmitter family for flow measurement was designed to have easily replaceable main electronics and communication modules. This approach enables the straightforward addition of future communications standards and new functionalities.
But there are limits to the refurbishment and reuse of measuring devices. “Due to the large number of variants, almost every one of the three million instruments we produce each year is unique,” Fröhlich explains. Other obstacles to refurbishment are the lack of standardized measurement technology in plants, industry-specific standards, individual process requirements and the criticality of many measuring points. Yet there is potential to reduce the product-related carbon footprint during instrument operation: “Most new field devices from Endress+Hauser now include Heartbeat Technology with diagnostic, verification and monitoring functions. This makes it possible to optimize calibration cycles and precisely schedule service calls,” he says.
Fröhlich sees one thing as certain: decarbonization of the portfolio will shape innovation at Endress+Hauser. That will take close cooperation with customers, whose current priority is to tackle the major emissions drivers at their plants, such as energy supply, machinery, pumps and pipework. “At a large chemical site, measuring technology accounts for only half a percent of the carbon footprint,” he says.
Published 20.12.2023, last updated 12.01.2024.
Dive into the world of the process industry through new exciting stories every month with our «changes» newsletter!
Subscribe to newsletter