As if by magic
The TrustSens temperature sensor continuously calibrates itself in the running process – a milestone for temperature measurement engineering.
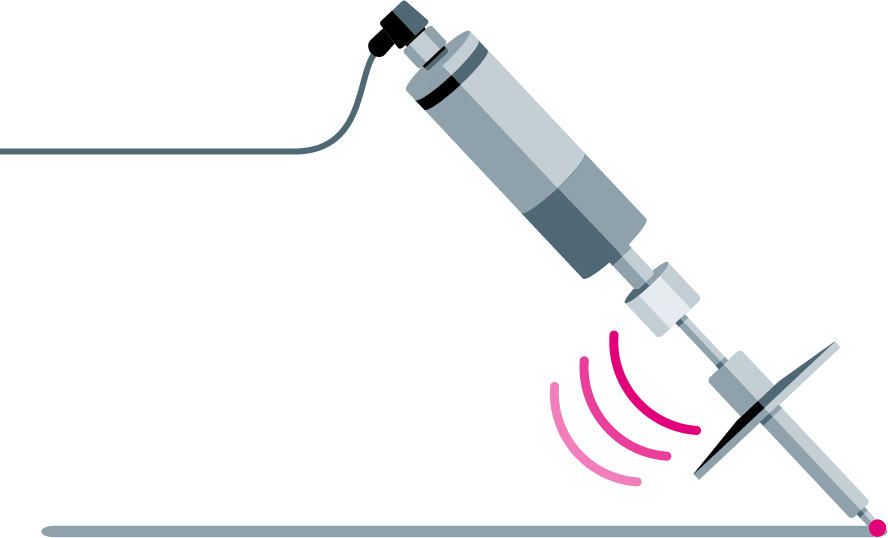
How TrustSens works
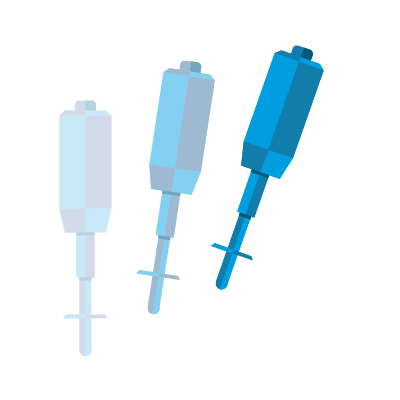
(1) Regulated industry
Measuring points in the life sciences and food & beverage industries often have to be dismantled and reassembled several times a year in order to be calibrated. This is time-consuming and costly, in particular for large plants.
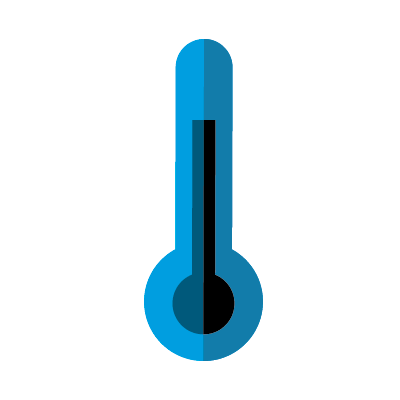
(3) Physical phenomenon
The sensor takes advantage of the so-called Curie temperature: a constant value which, once attained, abruptly changes the characteristics of a material. The Curie value can be precisely determined for every material.

(5) Minimal effort
Human intervention is only necessary if the TrustSens sensors report a malfunction. Calibration certificates can be provided automatically via asset management software such as Endess+Hauser’s FieldCare.
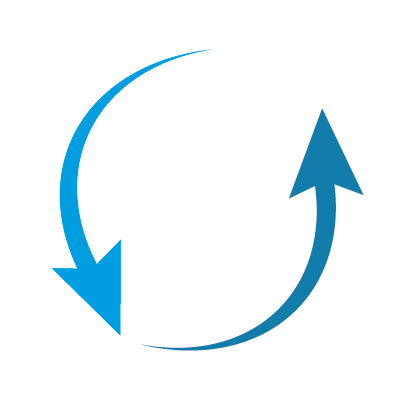
(2) Sense-it-yourself
With TrustSens this is a thing of the past: it is the first sensor that can carry out its own traceable calibration – continuously and on-line. This reduces the risk of unrecognized measuring errors down to a minimum.
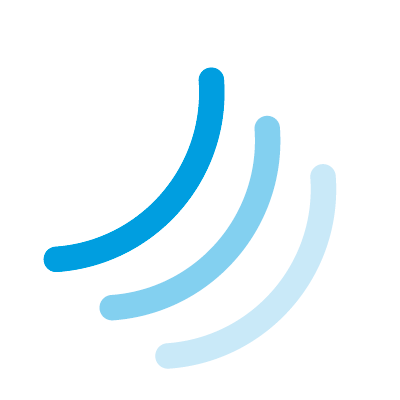
(4) Built-in reference
A special reference (master) sensor supervises the primary temperature sensor. A calibration of the primary sensor occurs each time the Curie temperature of the reference sensor falls short.
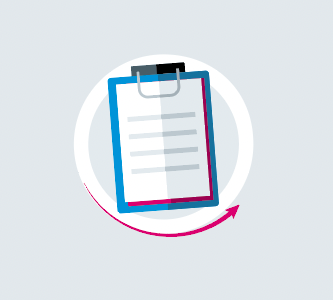
10 years of research and development back up TrustSens. The Endress+Hauser life sciences network initiated the breakthrough technology. Customers and partners from the world of science were closely involved.
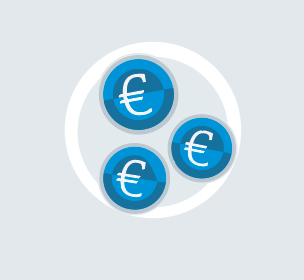
850.000 euros is the amount a plant operator can save with TrustSens over a period of five years if 1,000 temperature sensors have to be recalibrated twice a year. By this sample calculation, the extra investment pays off after only the second calibration.
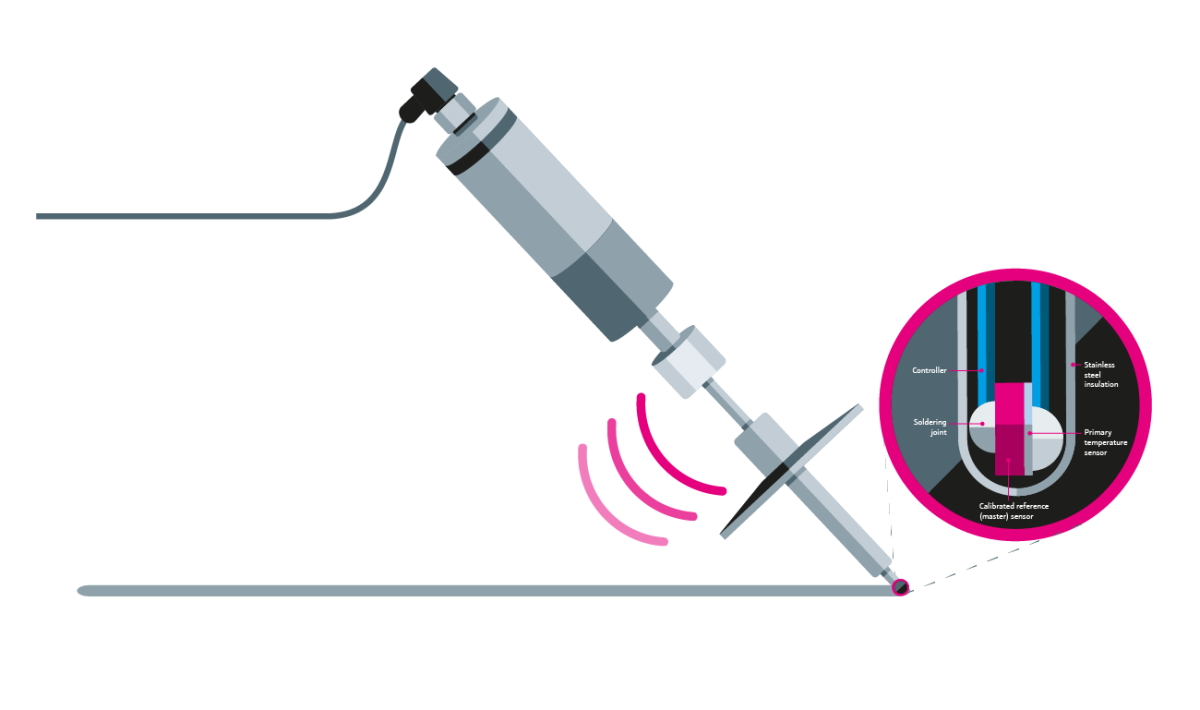
Published 10.10.2017, last updated 16.12.2022.
Dive into the world of the process industry through new exciting stories every month with our «changes» newsletter!
Subscribe to newsletter