Hitting the gas for hydrogen
Green hydrogen has the potential to decarbonize entire industries. But as a fuel for the new zero-emissions energy era, it would need producing in huge amounts, a feat that requires enormous effort. Companies and researchers are working together to bring industry closer to the goal of CO2 neutrality.
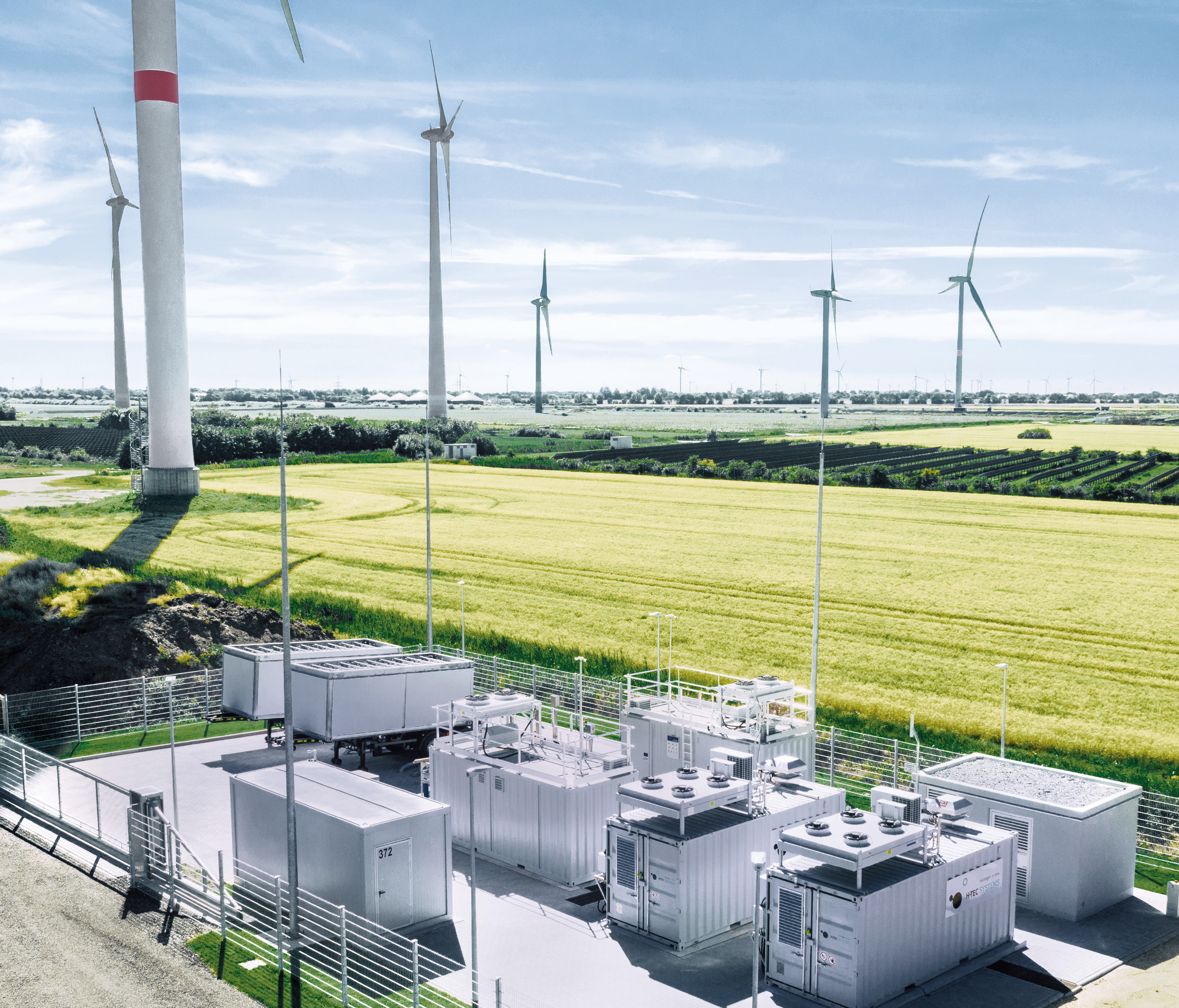
In some places the future is already here. Take the northern coast of Germany, for example, where the land is flat and the horizon wide. Meadows alternate with fields, and wind turbines and solar modules generate renewable energy. Over the last two years, this region has seen the addition of five white containers that hold electrolyzers from H-Tec Systems. These use locally generated electricity to split water into hydrogen and oxygen. The hydrogen goes on to further use.
While it may sound simple, there is a whole lot more behind it, because here is a piece of the global energy revolution puzzle. Hydrogen produced with wind, water and solar energy is CO2-free – also known as ‘green’. “Green hydrogen could be one of the keys to the energy transition and help industry achieve a breakthrough in decarbonization,” says Uwe Wagner, Global Industry Manager for Power & Energy at Endress+Hauser.
This emissions-free gas has numerous uses in many sectors. It makes excess production of green energy storable. It can be fed into the gas grid. And it can be converted to electricity and heat in fuel cells. In the chemical industry, it serves as a feedstock for producing ammonia and methanol. In the oil industry it’s used in the refining process. Combined with CO2, it makes synthetic methane and synthetic fuels. “And in the steel industry, green hydrogen can replace coal as a reducing agent in blast furnaces that manufacture pig iron,” says Jens Hundrieser, European Industry Manager for Energy at Endress+Hauser.
To date the global demand for hydrogen, currently at 90 million tonnes annually, has been met almost entirely with inexpensive gray hydrogen produced by steam reforming of fossil fuels. Electrolysis currently generates just 0.03 percent. Still, more than 30 countries have adopted or are planning a national H2 strategy. In the EU alone, the goal is to increase production of renewable hydrogen to 10 million tonnes per year over the period 2024 to 2030. Alliances are driving the project forward.
“Industry and science are working together to make green hydrogen a competitive product.”
Jens Hundrieser,
European Industry Manager for Energy at Endress+Hauser
From niche application to the heart of industry
“Industry and science are working together to make green hydrogen a competitive product. Work is underway on industrial-scale production, as well as on use in a wide range of applications,” reports Jens Hundrieser. Technological trailblazers in the manufacture of green hydrogen in Germany include H-Tec Systems, a manufacturer of PEM electrolyzers and electrolysis stacks based in Augsburg, as well as the Center for Solar Energy and Hydrogen Research Baden-Württemberg (ZSW).
For more than 10 years, ZSW has been developing electrolyzers and components on its own initiative and on behalf of customers. The center also plans and sets up test systems and builds demonstration systems. “At the beginning we were guided by the then novel power-to-gas concept as a way to store renewable energy whose production inherently fluctuates, rather than being steadily generated to meet consumer demand. Hydrogen with its high energy density makes the ideal storage medium,” says Andreas Brinner, Head of Electrolysis and Location Support. “For this reason we wanted to develop an alkaline electrolyzer that would operate efficiently and at low cost – in other words, a system that is an effective energy converter, with a long service life, able to start up quickly, endure downtime and require little auxiliary energy.”
These are also the features of another major process that H-Tec Systems is focusing on: proton exchange membrane electrolysis, or PEM for short. In contrast to alkaline electrolyzers, the PEM process dispenses with potassium hydroxide as an electrolyte. Instead, it utilizes a semipermeable membrane that allows the passage of protons. “PEM electrolyzers have the advantage of continuing to operate efficiently under rather less than full load, so they do a great job on fluctuating renewable energy,” explains Emily Pröll, Marketing Manager at H-Tec Systems.
Since this is a relatively new technology compared to alkaline electrolysis, its use to date has been only on a small scale and in niche applications. “PEM electrolysis still has a lot of development potential. In the years to date our primary goal has been to design an efficient, scalable technology that customers can use to produce industrial quantities of high-quality hydrogen at the lowest possible cost.”
High demands on the measurement technology
There are plenty of challenges in hydrogen production. “Electrolysis relies on lots of auxiliary systems coupled together and decked out with measuring points for all kinds of parameters that require continuous monitoring. Hence the need for a considerable amount of reliable and precise measurement instrumentation,” explains Andreas Brinner. Then there is the fact that H2 is the lightest of all gases, with extremely small molecules. “Hydrogen easily diffuses through lots of materials and can cause metals to become brittle,” says Prasanth Sreekumar, Global Industry Development Manager for Gas at Endress+Hauser. “This calls for careful selection of materials, instruments and seals.”
Like many other electrolysis specialists, both H-Tec Systems and ZSW put trust in instrumentation from Endress+Hauser. “We have long relied on measurement technology from Endress+Hauser and value its quality, reliability, precision, media resistance and versatility. The large portfolio gives us many options,” says Andreas Brinner. Other pluses include the instruments’ compliance with functional safety (SIL) and explosion protection requirements. This in turn guarantees a high degree of plant safety. “We can cover a wide range of measurement tasks in our process with the sensors from Endress+Hauser,” confirms Martin Linder, Development Engineer at H-Tec Systems. “What’s also important for us is their straightforward installation and commissioning.”
900
million tonnes of CO2 are emitted each year in the course of producing hydrogen from primarily fossil sources.
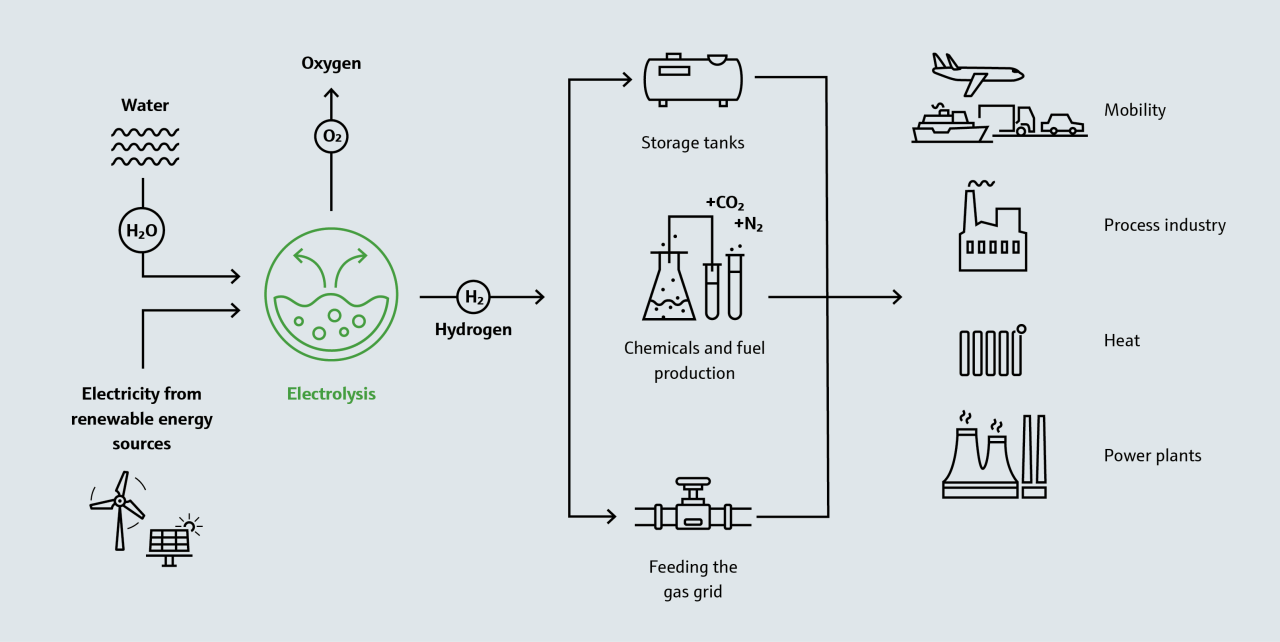
Multitalented
Green hydrogen holds potential across a wide range of sectors. It can be converted to electricity and heat in fuel cells, fed into the gas grid or used in gas turbines. In the chemical industry, it serves as a feedstock for producing ammonia and methanol. In the oil industry it’s used in the refining process. Combined with CO2, it makes synthetic methane and synthetic fuels. In the steel industry, green hydrogen can replace coal as a reducing agent in blast furnaces that manufacture pig iron.
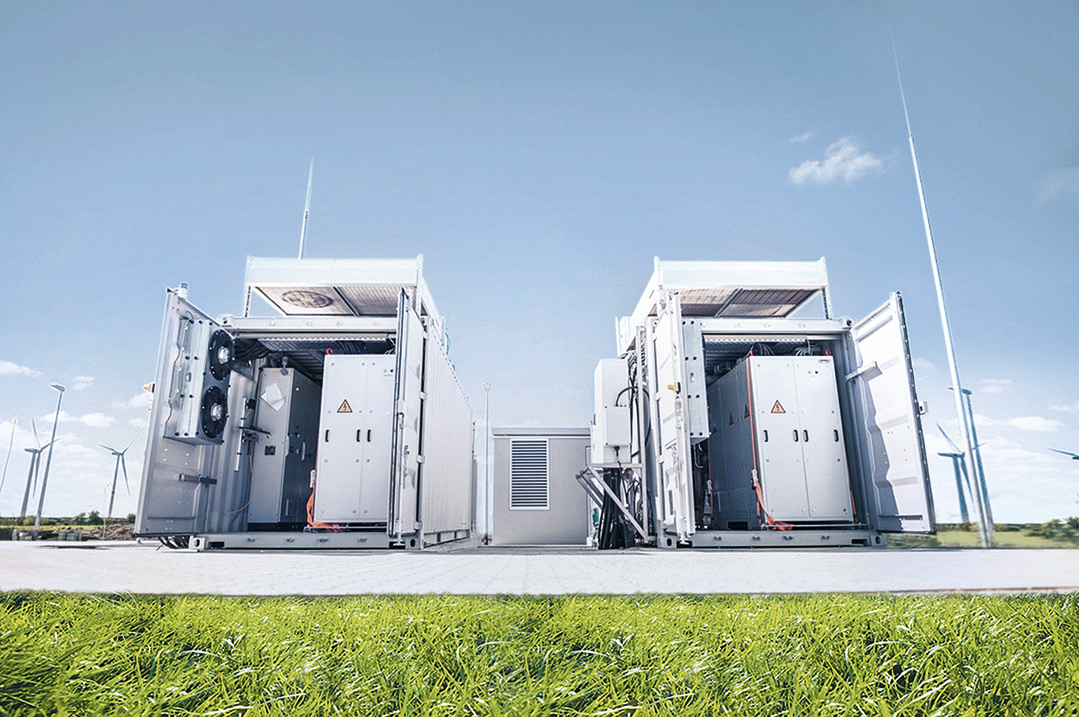
The electrolyzers from H-Tec Systems have a compact design. PEM stacks built inside mobile containers produce hydrogen efficiently.

46
million tonnes of H2 were used by the chemical industry in 2020, three-fourths for ammonia production and one-fourth for methanol production. Around 40 million tonnes went into oil refining.
Endress+Hauser has benefited as well from its early involvement in green hydrogen. “This allows us to learn together with our customers and expand the breadth of products and solutions for the hydrogen sector,” emphasizes Prasanth Sreekumar. The market requires not only instruments that can withstand pressures of up to 1,000 bar and beyond, but also solutions suited to extremely low temperatures. “Innovation is in our DNA. Today Endress+Hauser boasts a broad portfolio of solutions for critical measuring points in the hydrogen value chain,” adds Prasanth Sreekumar.
The portfolio includes gas analyzers that use laser-based technologies such as TDLAS to reliably and precisely determine the quality, concentration and composition of gases, all with minimal maintenance effort. Added to that are solutions along the value chain, such as flow measurements in pipelines or level measurements in tanks storing liquid hydrogen. Customers furthermore profit from Endress+Hauser’s expertise in the field of gas applications. “We have acquired valuable process and industry knowledge over the years, from both gray and blue hydrogen applications, as well as from CO2 capture,” reports Prasanth Sreekumar. “That makes it easier to jointly develop standards for new applications.”
H-Tec Systems has demonstrated many times that PEM technology is helping to spur the energy transition. At E-Farm, for instance, Germany’s largest hydrogen mobility project, the locally produced H2 is transported to hydrogen filling stations. In other projects, green hydrogen is fed into the gas grid or used in gas turbines. “We are swamped with inquiries. There is also interest from industrial sectors in addition to mobility applications,” explains Emily Pröll. Andreas Brinner from ZSW can confirm this trend: “We have a lot to do.”
On the path to mass production
Both ZSW and H-Tec Systems are currently focused on reducing the cost for green hydrogen in order to make it more competitive. To do that, data is being used to optimize the electrolysis process and increase the power rating of the individual modules comprising the systems. “At the moment we’re making inroads into increasingly larger areas,” reports Emily Pröll. “That means more and more systems in the double-digit megawatt range.”
Another goal is to enable the series production of electrolyzers. This is where H-Tec is working with industry and research partners, within the framework of the German government-funded flagship project H2Giga, to develop new production processes for PEM electrolysis stacks and electrolyzers. ZSW is also addressing the question of how electrolyzer technologies can be scaled further. “We’re conducting research into materials and manufacturing technologies that will allow implementation on an industrial scale,” says Andreas Brinner. The scientists are also developing a concept for large-scale manufacturing of electrolyzer blocks.
The market is already demonstrating how progress is being made with green hydrogen. Shell has been operating Europe’s largest PEM electrolyzer featuring 10 megawatts of capacity since 2021. And in 2022, industrial gas manufacturer Linde will bring online the world’s largest PEM electrolyzer, rated at 24 megawatts. Several 100-megawatt projects across the globe are also planned. The focus is primarily on regions that have an abundance
of renewable resources for electrolysis: inexpensive energy from solar, wind or hydropower plants, as well as seawater that can be desalinated.
It seems the future is picking up even more steam. Whether the impetus is sufficient depends on more than just investments, new technologies and industry’s willingness to change. “The political frameworks must be right as well,” emphasizes Jens Hundrieser, who recently started representing Endress+Hauser in the European Clean Hydrogen Alliance. Above all, that means one thing: “A global carbon pricing mechanism has to be established. Only then will the energy transition be successful. Only then will the hydrogen economy prevail. And only then can the global climate goals be achieved.”
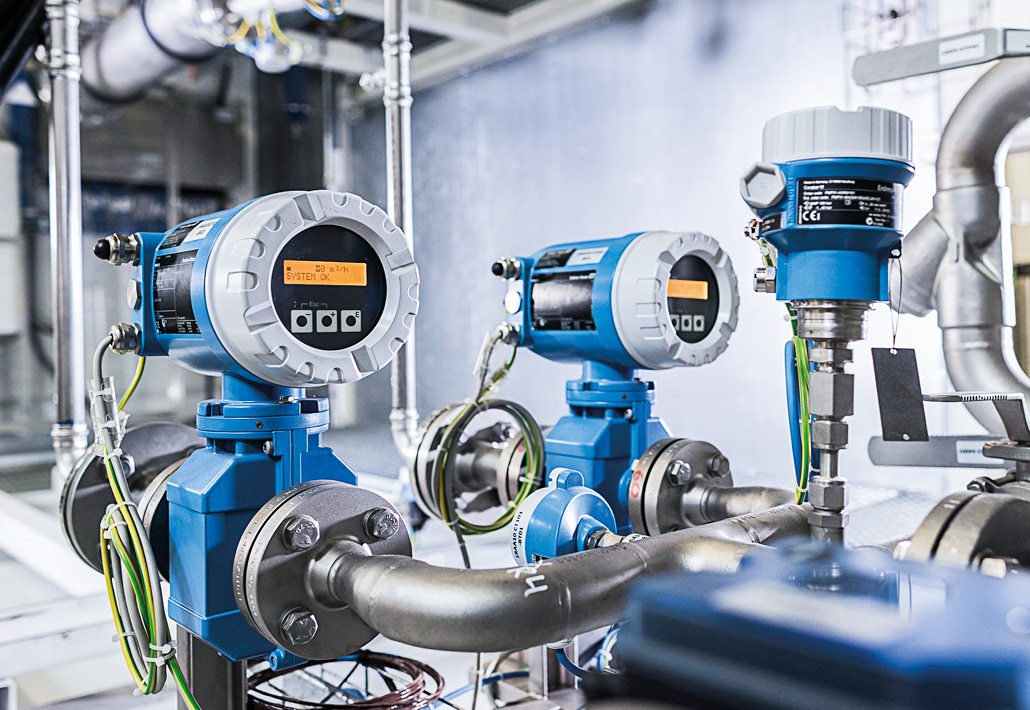
Reliable, precise and robust: the Center for Solar Energy and Hydrogen Research Baden-Württemberg relies on instruments from Endress+Hauser to monitor the electrolysis process.
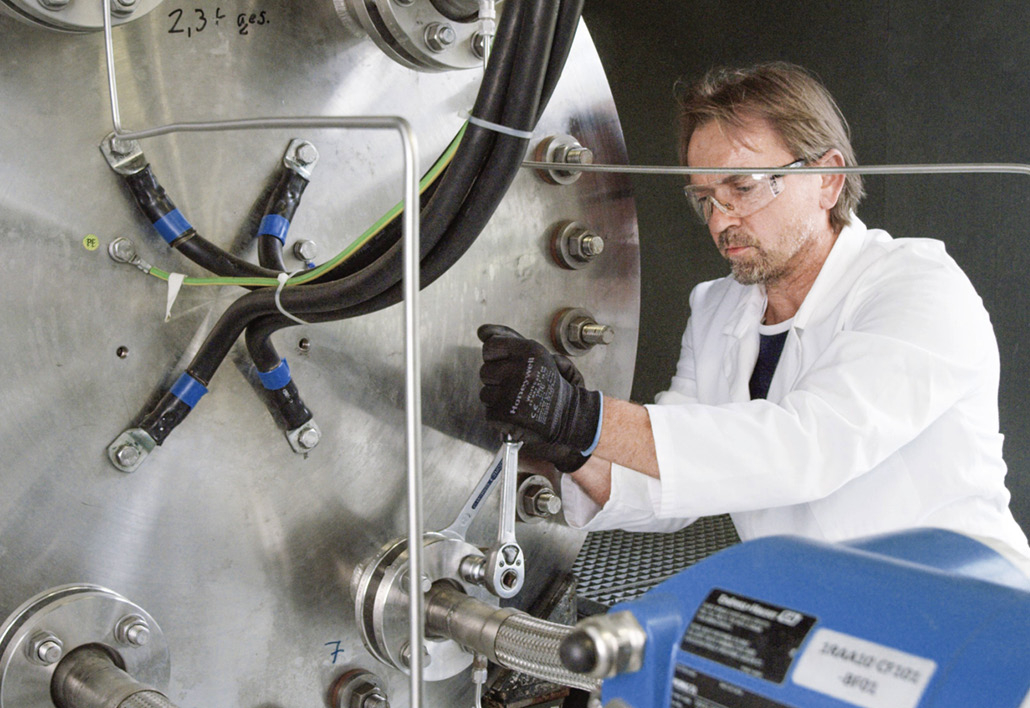
Published 21.07.2022, last updated 14.09.2022.
Dive into the world of the process industry through new exciting stories every month with our «changes» newsletter!
Subscribe to newsletter