A clever combination
Making better, data-based decisions just got easier thanks to the Netilion IIoT ecosystem from Endress+Hauser. Netilion automates the transformation of data from the field into valuable information. Here are three illustrative examples of customers who already see their everyday business benefitting from the opportunities afforded by Netilion – in terms of improved operation, streamlined maintenance and lower costs.
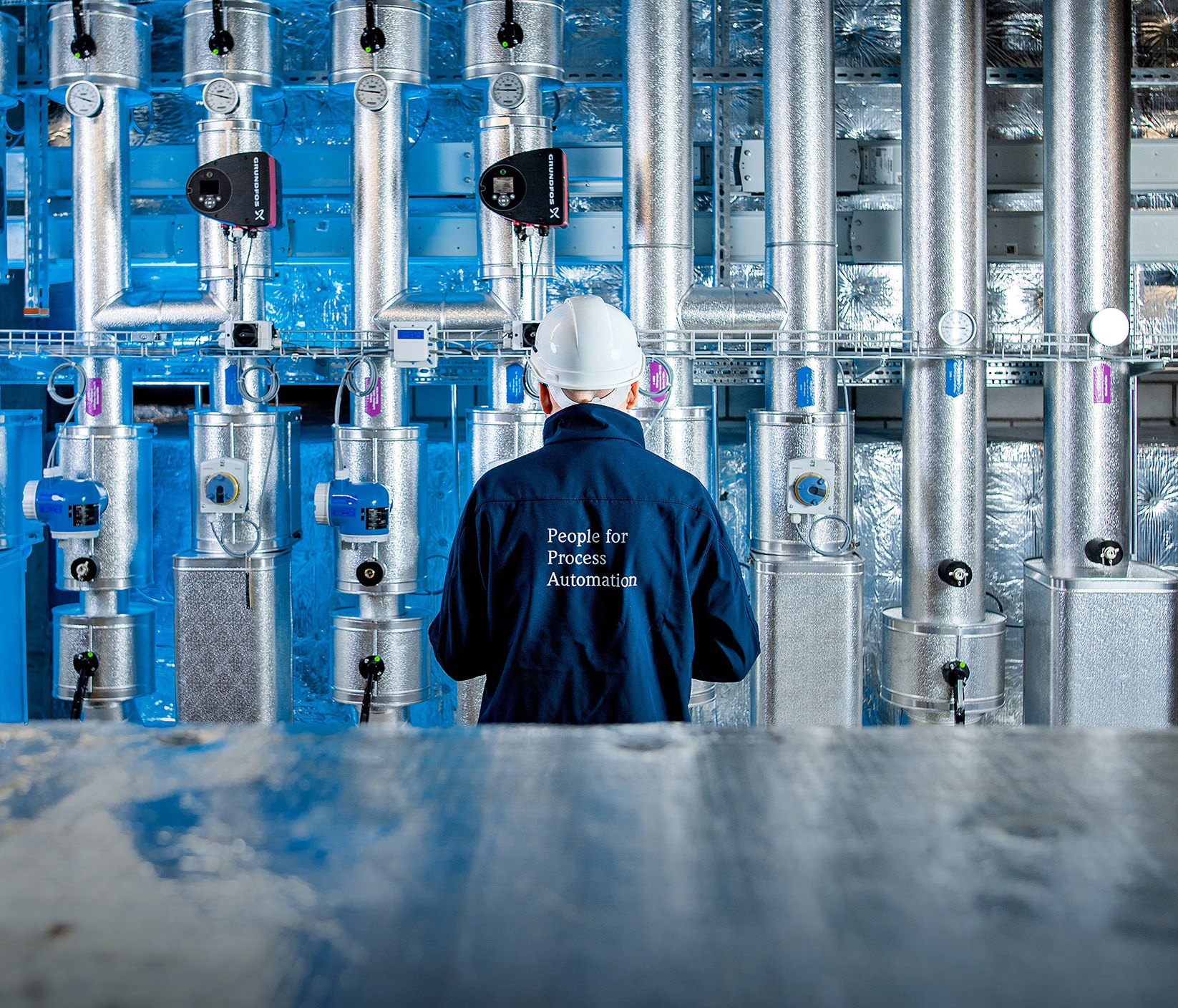
19000
measuring points have been digitally captured for the service contract with the 15 Brazilian operations of a global brewery group.
Progress can sometimes be measured in numbers, for example when taking inventory of the installed base of field instruments in process plants. Carlos Behrends, Managing Director of Endress+Hauser Brazil and Corporate Sales Director for South America, reports: “Two of our service technicians toured the country for six months, developing a calibration concept for the Brazilian branches of a large brewery group. To that end they pinpointed the applicable measuring points at 15 locations. They noted down instrument after instrument on site, drew up lengthy tables, structured them according to specific criteria and analyzed the results in painstaking detail. After Endress+Hauser won the service contract, the two engineers repeated their installed base analysis, this time for every one of the breweries’ 19,000 measuring points. By that time the Netilion IIoT ecosystem had been introduced, which helped them greatly. “With our new digital tools we needed only a fraction of the time and gained much deeper insights into the instruments,” points out Carlos Behrends.
GAINING TRANSPARENCY
For the digital installed base analysis, the Endress+Hauser service engineers relied on Netilion Analytics – a digital service embedded in the Netilion IIoT ecosystem – together with the Netilion Scanner app. This uses a smartphone or tablet’s built-in camera to snap an image of the instrument name plate and automatically generate a digital twin from the information printed on it. Netilion Analytics analyzes the transmitted data, links the data for Endress+Hauser instruments to entries in the device database and presents a clear display of results. A dashboard shows key information at a glance. Detail on every instrument is readily retrievable. “We get loads of useful information about the installed base, such as instrument age, availability of spare parts or the extent to which the measurement technology is standardized,” reports Saymon Galaci, Strategic Account Manager for the customer in Brazil. “We can also spot straightaway the criticality of a given measuring point to the process, an important criterion for us when it comes to calibration.”
This newfound transparency aims to improve the maintenance and operation of the customer’s breweries in Brazil. “With Netilion we save time and resources. We can do a better job of planning calibration activities, avoid plant downtime and drive down maintenance costs,” says Saymon Galaci confidently. Regarding the maintenance contract, Endress+Hauser uses the Netilion IIoT ecosystem as a tool for its own service technicians, so they can do the best possible job of fulfilling a customer order. “Our aim is to see the customer renew the contract in five years’ time,” emphasizes Saymon Galaci. He is convinced that sooner or later the group itself will be exploiting the possibilities of digitalization in its brewing operations, just like increasing numbers of plant operators already do today.
“With Netilion we save time and resources. We can do a better job of planning calibration activities, avoid plant downtime and drive down maintenance costs.”
Saymon Galaci,
Strategic Account Manager at Endress+Hauser Brazil
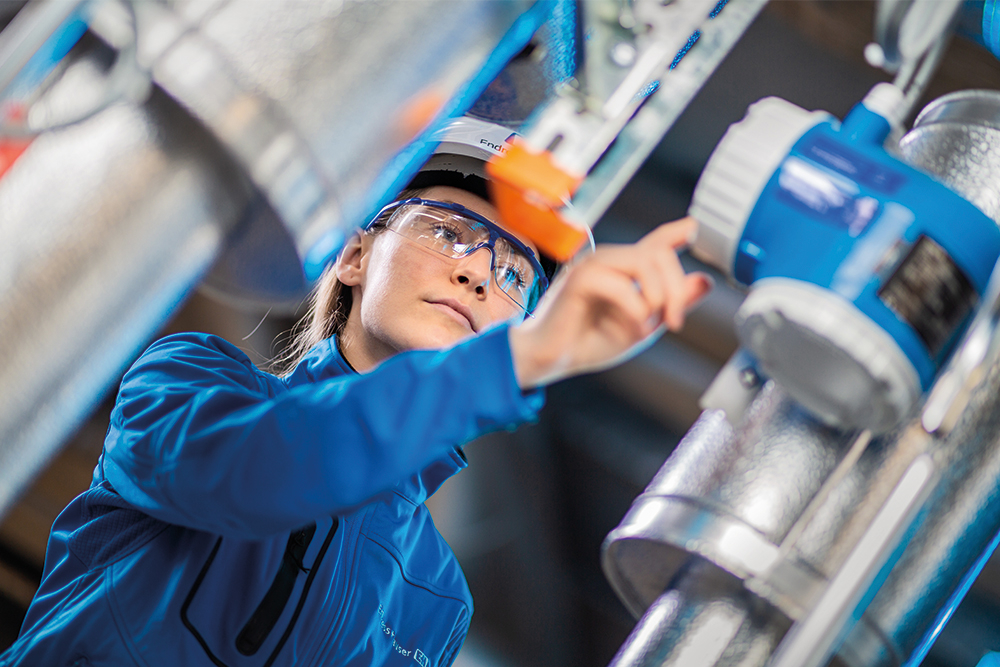
To develop a calibration concept for the instrumentation of a process plant, the entire installed base must first be captured manually or electronically.
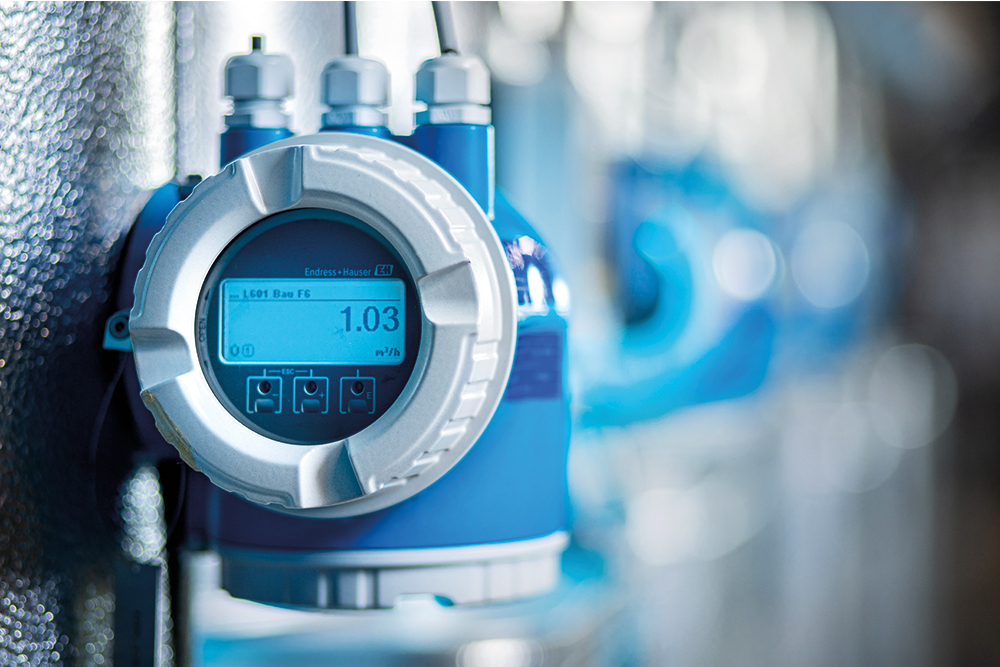
Which are the operationally critical measuring points? A digital service like Netilion Analytics helps to quickly and reliably pinpoint the instruments concerned

In large plants, measuring devices are installed in countless and sometimes hard-to-access locations, such as these brewery fermentation tanks.
5
Data fusion and analysis
Algorithms for early anomaly detection, verification, forecasts, etc.
4
Data management and visualization
Monitoring of networks and decentralized infrastructure
3
Data collection and transmission
Flexible edge connectivity solutions
2
Data collection and control
Smart field devices and sensors (flow, level, pressure, temperature, analysis, etc.)
1
Physical world
Infrastructure (pipes, pumps, valves, etc.)
“The smart maintenance management feature helps customers to fully concentrate on their core competencies.”
Julia Grether,
IIoT Product Owner at Endress+Hauser
SCALABLE SOLUTIONS
“Netilion makes digitalization something tangible for the process industry. By linking the physical and digital domains, our IIoT ecosystem ingests field-level data and then generates valuable information from it,” says Tobias Zubler, Service Product Manager at Endress+Hauser. The full benefits come to fruition with dynamic utilization of process and instrument data. Where field instruments themselves lack the required connectivity, there are adapters or edge devices for opening up an additional secure communications channel. This is a must for using other cloud-based services. “Netilion offers customers a wealth of possibilities, consistently aligned with their needs,” explains Tobias Zubler, who goes on to emphasize: “Our solutions are scalable, starting with basic data transmission from individual measuring points, to utilization of digital services for greater operational efficiency, to a full package where we remotely monitor instruments while assuming responsibility for their service.”
REMOTE MAINTENANCE
Management at the Waterschap Hollandse Delta regional water authority went for just such an all-encompassing solution. The authority operates 19 wastewater treatment plants in the southern Netherlands, spread over five islands and the port city of Rotterdam. “The water authority service technicians have more than 270 sensors and analyzers to maintain and service. For instrument inspections, that previously meant driving to individual plants, some of them unstaffed,” explains Julia Grether, IIoT Product Owner at Endress+Hauser. The issue is that these routine visits take time. And when problems do arise, the technicians cannot see what has actually happened until they are on site. To rectify a problem, they sometimes have to call for help from other experts.
This is what Waterschap Hollandse Delta wanted to change. “To ensure maximum possible plant availability and reduce costs, the authority looked around for a partner who could provide an intelligent maintenance scheme along with a comprehensive service package for the next 10 years,” reports Julia Grether. Endress+Hauser sold the water authority on an all-round portfolio of measuring technology, coupled with the possibilities offered by the Netilion IIoT ecosystem. “What helps us is the capability for continuous remote monitoring of the instrumentation. Plus, over time, we can leverage the data to become proactive and stop problems before they even occur. Our goal is a significant reduction in the number of on-site service calls,” says Julia Grether.
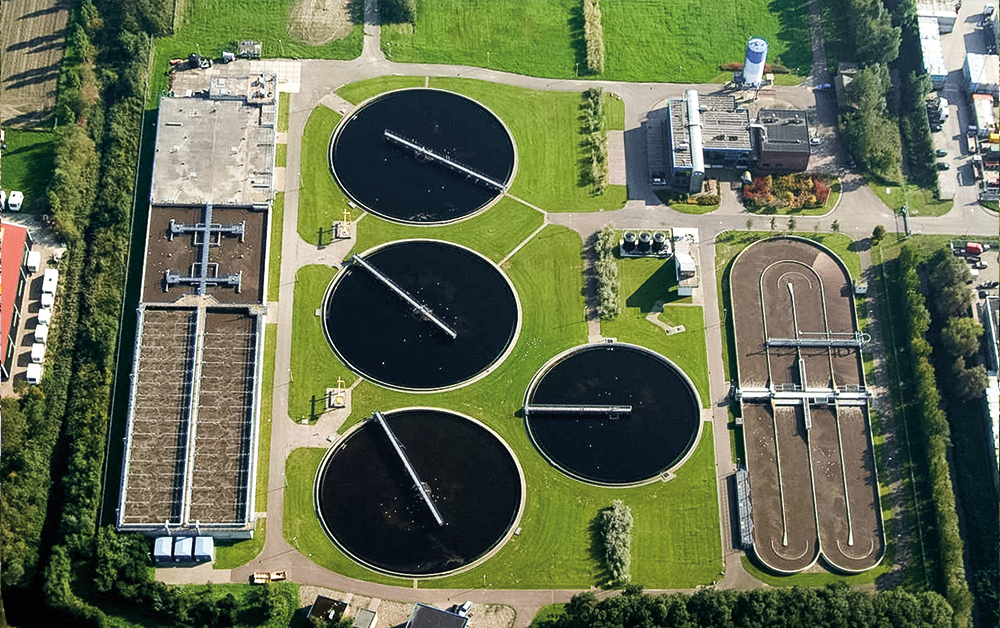
One of 19 wastewater treatment plants operated by the Waterschap Hollandse Delta water authority.
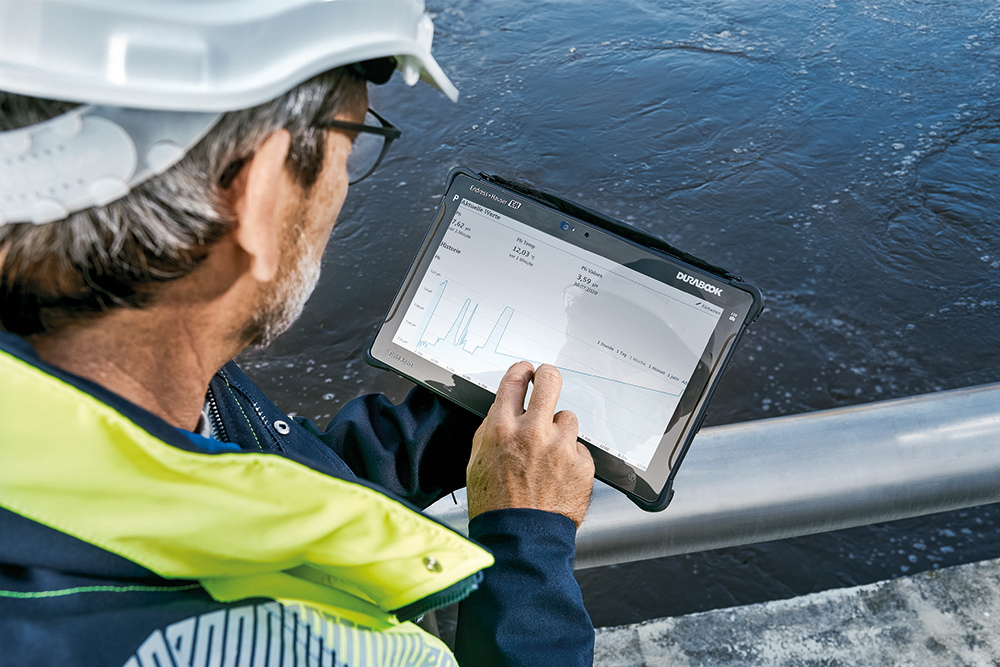
Sensor data and device information are remotely accessible via digital services.
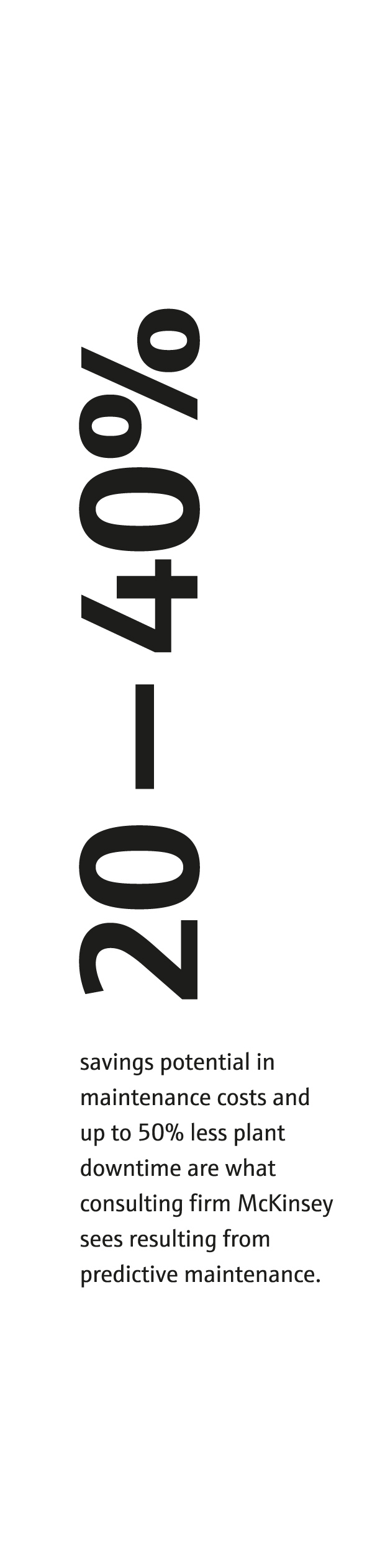
INCREASED OPERATIONAL RELIABILITY
How, exactly, does this work? First, existing instrumentation was completely swapped out. The newly installed sensors and analyzers from Endress+Hauser all send their signals and data via edge devices to the Netilion cloud. The Netilion Health service in turn gives the Endress+Hauser team a dashboard they can check anytime to see that everything is okay, based on the constant monitoring of the instruments’ diagnostic data. Should an error pop up, technicians use the transmitted diagnostic information to instantly pinpoint the cause and decide how to fix things. “Netilion Analytics also shows the precise location of each instrument in the plant,” adds Julia Grether. Finally, the Netilion Library service helps on site by presenting full documentation for any instrument.
But Netilion does more than facilitate a fast and focused response to malfunctions. It also helps to prevent them from happening at all. “Our analyzers detect supply levels of reagents needed for operation,” explains Julia Grether. Should a supply fall below its predetermined threshold, this automatically triggers a notification. The water authority can then act in time to top up the supply and ensure continued reliable operation. “Netilion also makes it possible to keep an eye on the sensors. If we detect deviations over time, we can replace them before they malfunction,” says Julia Grether. According to the contract, Endress+Hauser assumes full responsibility for maintenance and calibration activities during the first year. Thereafter, appropriately trained authority employees will use Netilion themselves for basic service activities such as sensor cleaning. “The smart maintenance management feature helps customers to fully concentrate on their core competencies,” points out Julia Grether.
“Compatibility between systems is essential for plant operators to extract optimum benefit from field-level data.”
Steffen Ochsenreither,
Business Development Manager at Endress+Hauser
LINKING SYSTEMS
“We have talked about condition monitoring and predictive maintenance in the process industry for ages. Now we are gradually approaching these topics,” says Steffen Ochsenreither, Business Development Manager at Endress+Hauser. However, large brownfield plants often contain not just hundreds but thousands of sensors from various vendors. “Compatibility between systems is essential for plant operators to extract optimum benefit from field-level data,” explains Ochsenreither, who adds: “This is why our Netilion IIoT ecosystem offers connectivity with other cloud solutions.” One example is SAP’s Asset Intelligence Network (AIN), a cloud-based maintenance platform giving shared access to operators, suppliers and service partners. The prerequisites are defined interfaces and a standardized reference architecture that ensures all manufacturers adopt the same structure for providing data and information.
Both pharmaceutical company Boehringer Ingelheim and the Crop Science division of chemical and pharmaceutical giant Bayer use SAP AIN to administer their field instruments’ master data and manage maintenance and calibration activities. This all helps to optimize plant upkeep. “There is an interface for providing instrument-specific data and information from the Netilion cloud to the SAP AIN platform,” explains Steffen Ochsenreither. “Employees have ready access to up-to-date information and documentation on every field instrument, so they can complete tasks faster without needing to access manufacturer-specific solutions and platforms,” says Ochsenreither, clarifying the advantages. He sees this as a first step toward more transparency and even deeper integration. “Connectivity between IT systems like SAP and production processes at the OT level opens up completely new digitalization potential,” adds Ochsenreither with confidence. “This allows optimization of operational processes over a plant’s entire life cycle, as well as linking of value chains beyond enterprise boundaries.”
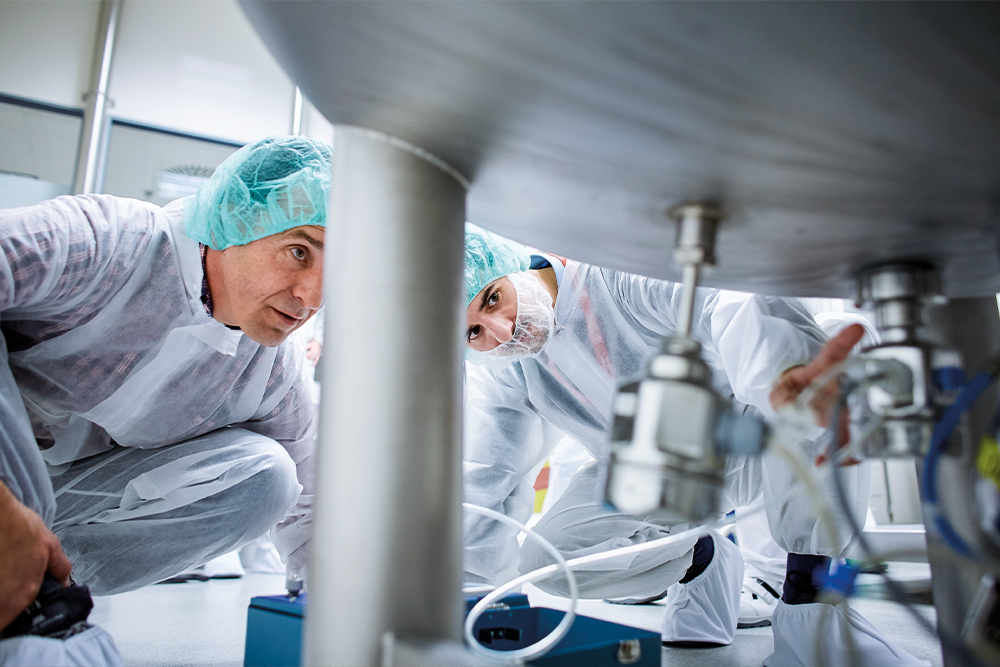
Large chemical and pharmaceutical plants are fitted with thousands of sensors from various manufacturers.
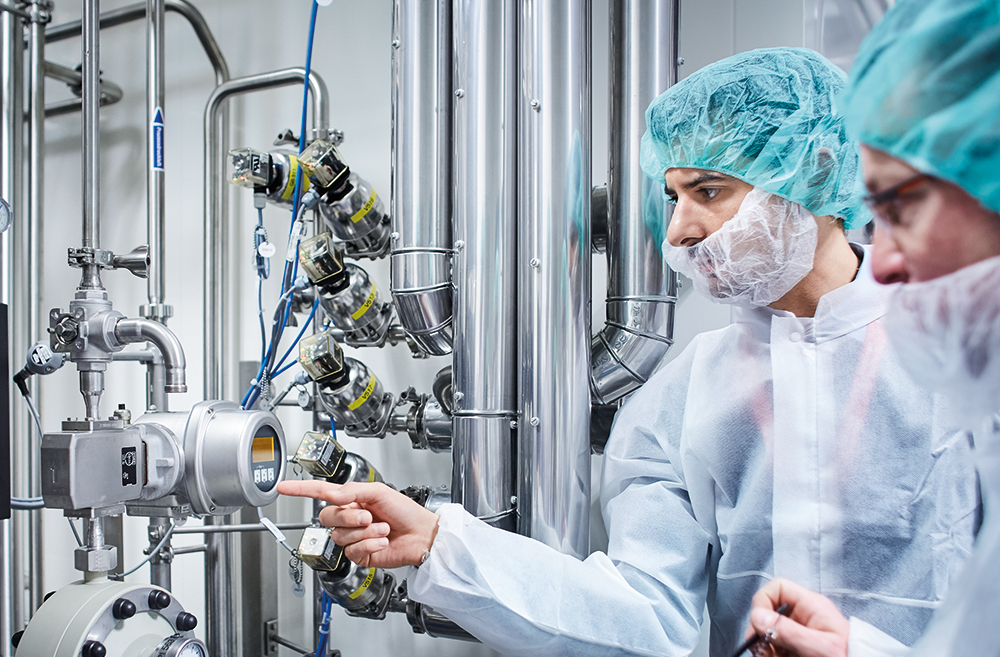
The Netilion IIoT ecosystem includes interfaces for providing instrument data and information to other platforms such as SAP.
Published 06.12.2022, last updated 12.12.2022.
Dive into the world of the process industry through new exciting stories every month with our «changes» newsletter!
Subscribe to newsletter