Riding the waves to success
Radar technology is often employed when reliable level measurement in containers is required. Ever since Endress+Hauser introduced this measurement principle in 1993, radar-based instruments have seen steady development. Let’s take a look at a genuine jack-of-all-trades.
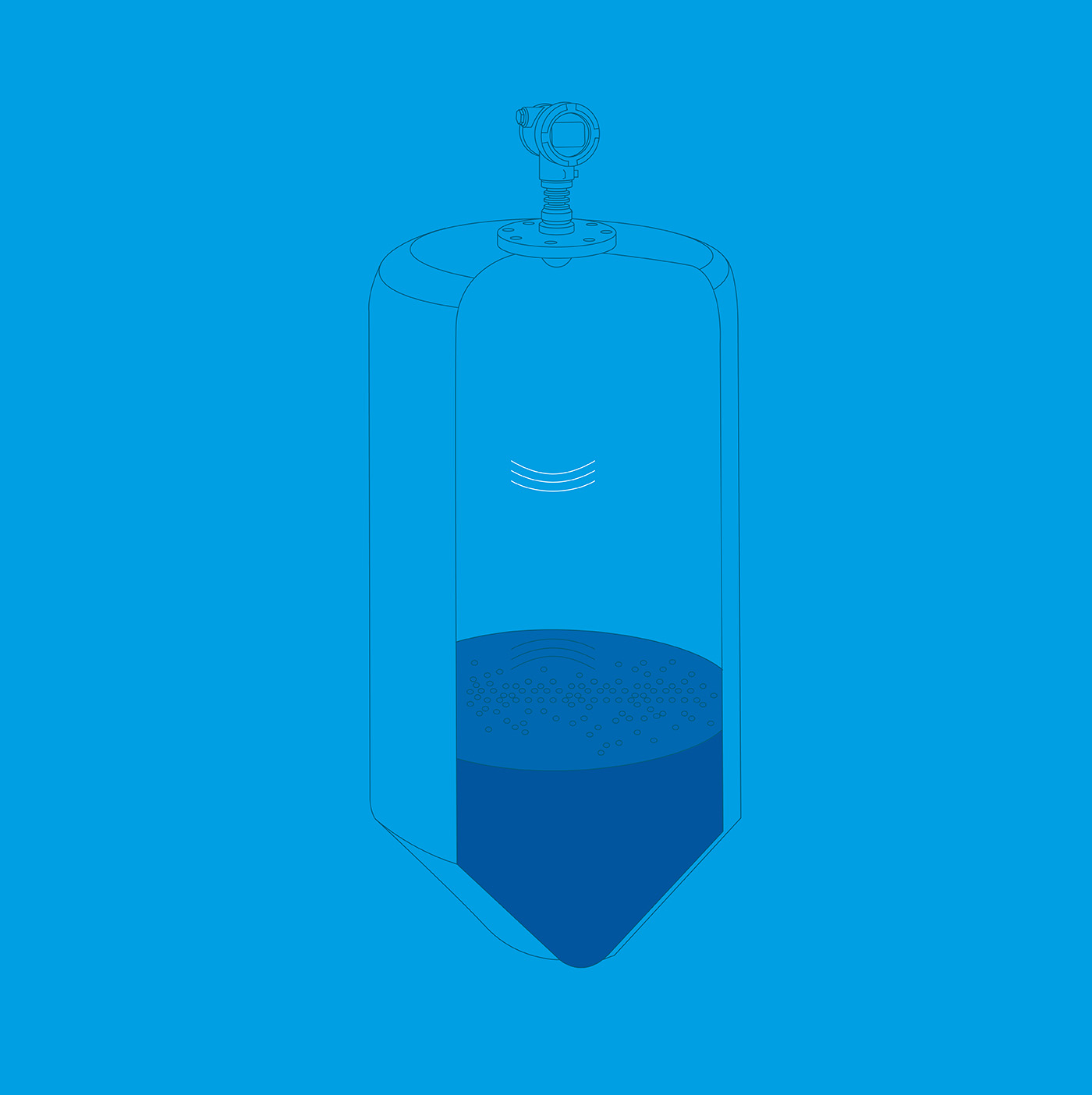
The requirements for level measurements are as high as they are diverse. Whatever the medium – pastes, bulk solids, liquids and more – precise measurement of fill levels forms the foundation for safe and efficient operation. Radar-based instruments utilize what is known as the time-of-flight measurement principle, where the system continuously emits radar pulses that the medium reflects back into a sensor. The time delay between emitted and reflected pulses is used to calculate the distance between the sensor and the surface of the medium. The distance value, taken together with the dimensions of the container, in turn yields the fill level.
How exactly the radar pulses are emitted depends on the operating conditions. If the signal flows to the medium along a rod probe, there is a high degree of reliability regardless of conditions at the medium surface. Instruments using free space radar waves provide contactless measurement and are often the first choice for critical applications in industries such as chemical, oil and gas, pharmaceuticals and food, since contactless measurement needs less maintenance.
Technology with a long history
Endress+Hauser has employed this radar measurement principle since 1993. Andreas Möller, Head of Product Management for Level Instruments, recalls the early days: “Our first radar-based level instrument was considerably larger than today’s systems and impractical for mounting on small containers. Furthermore, its high energy requirements always necessitated an additional power source.” Today’s instruments are highly compact and mountable on even the smallest of containers. For mobile applications, Endress+Hauser developed battery-operated instruments with wireless data transmission.
Engineers successively adapted the instruments’ functions for a closer fit with increasingly specific requirements. One example is instruments that operate at 26 or 80 GHz as opposed to the first models that used a frequency of 6 GHz. These later instruments are suited to media where the fill level is extremely difficult to measure by other methods, such as liquids with low relative dielectric constants (DC value) or liquids in reactors where material properties such as density change during the reaction process.
“Over the decades, radar-based measurement technology has evolved into a versatile solution. It delivers reliable and precise values, even in extreme conditions such as temperatures from minus 196 to plus 450 degrees Celsius, or pressure up to 160 bar,” says Philipp Walser, Level Portfolio Manager at Endress+Hauser.
Digital evolution
One aspect of the instruments’ evolution is their increasing ease of use for customers. The latest-generation Micropilot is ready to operate in short order using a built-in assistant. “Thanks to a Bluetooth interface and our SmartBlue app, customers have convenient remote access to systems. That means instruments can be configured and monitored from a safe distance, which is especially relevant in hazardous processes,” explains Andreas Möller. Integrating the instruments becomes smoother still thanks to industry-standard communication protocols and technologies such as Ethernet-APL.
Taking a glance into the future, Philipp Walser adds: “With innovations such as the new generation of Micropilot instruments, we have improved radar-based level measurement technology even further. Thanks to the diverse portfolio, and with further innovations in the pipeline, there will be continued high demand for radar technology in process automation.”
Published 28.08.2023, last updated 11.09.2023.
Dive into the world of the process industry through new exciting stories every month with our «changes» newsletter!
Subscribe to newsletter