Perfectly coordinated
With complex international projects, Endress+Hauser also handles customers’ supply chain management. From the life sciences industry comes a demonstration of the immense difference this makes.
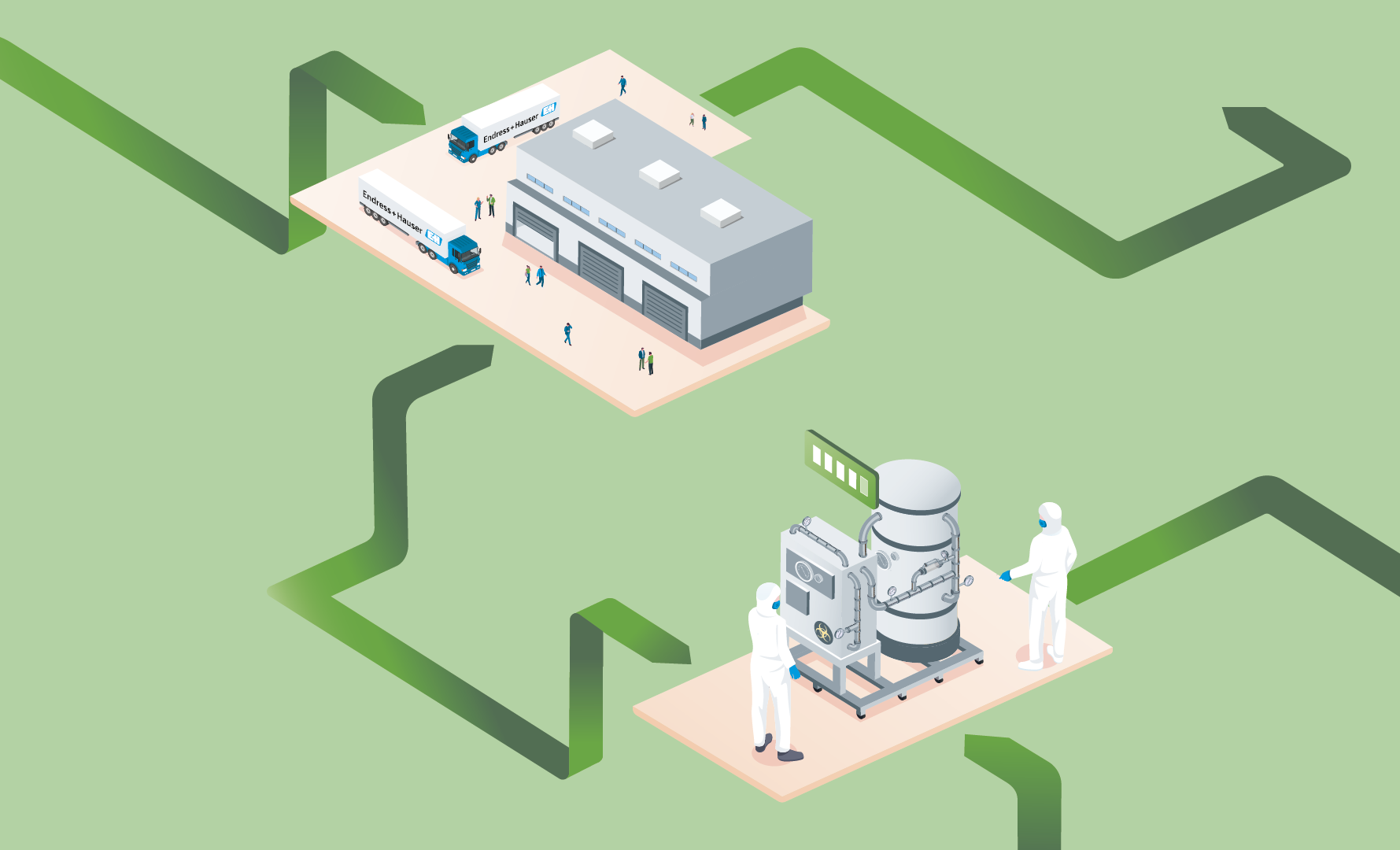
ONE FOR ALL
Time is of the utmost importance in the life sciences industry, more so than in virtually any other industry. To ensure that innovations reach patients speedily and to maximize the use of patents, medicines must be developed and brought to market as quickly as possible. “When approval of a drug is imminent, companies have to establish their production capacity in record time,” explains Philipp Zumoberhaus, head of global program management at Endress+Hauser. That is when he and his team lend their assistance to implement these transnational efforts. “As a prime supplier of instrumentation, we offer a full spectrum of measuring technology to the industry. In addition, with our global program we organize the entire supply chain side of things and coordinate everyone involved. That means our customers can focus completely on their core business and medicines become available earlier.”
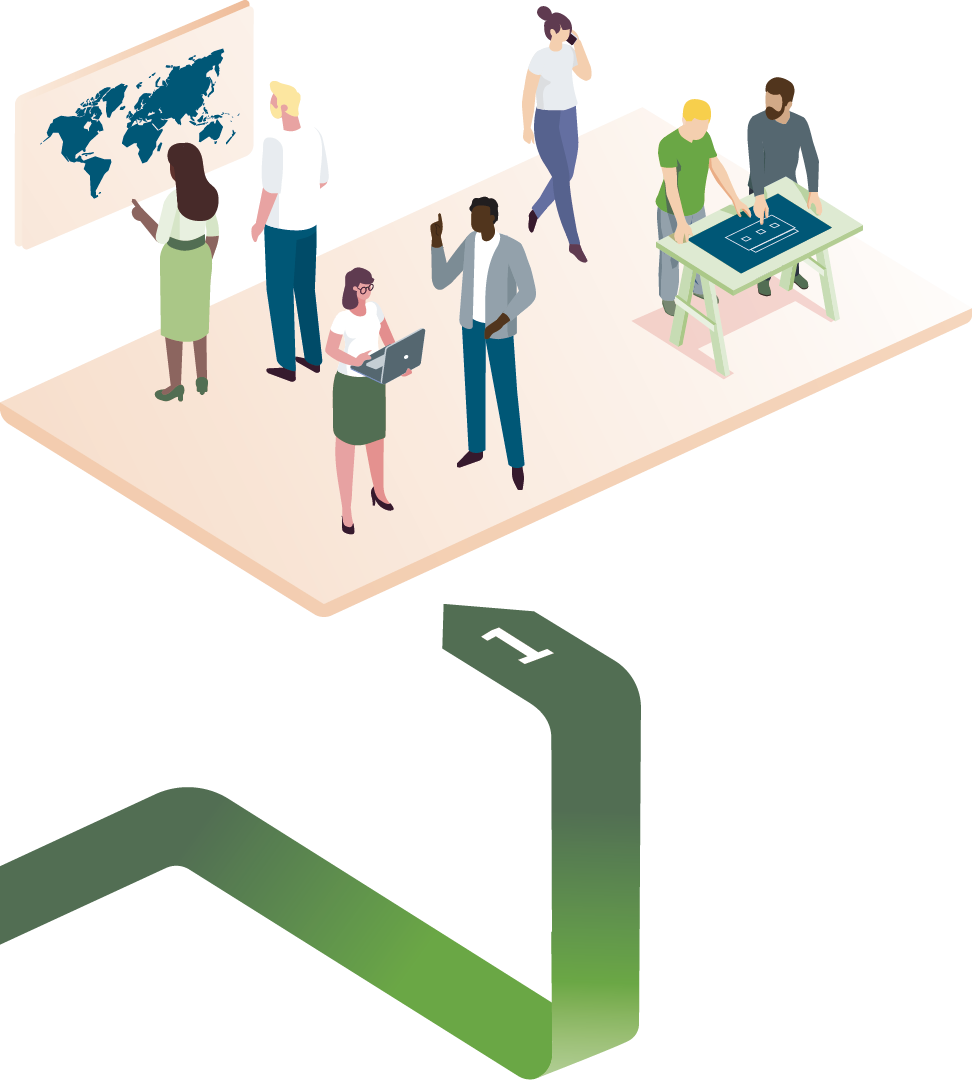
STANDARDIZED BASELINES
As a global project partner, Endress+Hauser is already contributing expertise at a plant’s preliminary design and detailed planning stages. “Modules destined for a plant come from engineering, procurement and construction (EPC) firms in more than one country. That makes it a good idea to standardize the instrumentation,” Philipp Zumoberhaus says. Engineers advise the end customer on the best measurement technology for each process at the new plant, agree with them a standardized basis for the instrumentation and ensure its correct implementation by the module suppliers. Standardization minimizes time and effort spent on installation. It also simplifies plant commissioning and employee training, as well as spare parts management further down the line. “Involving us early on also means that our product centers can plan better. And that ultimately guarantees high reliability of supply, helped along by the sales centers responsible for individual EPCs and by our global logistics network,” Philipp Zumoberhaus explains. A project schedule provides transparency and keeps everyone in the project coordinated worldwide, not least in the event of new requirements arising.
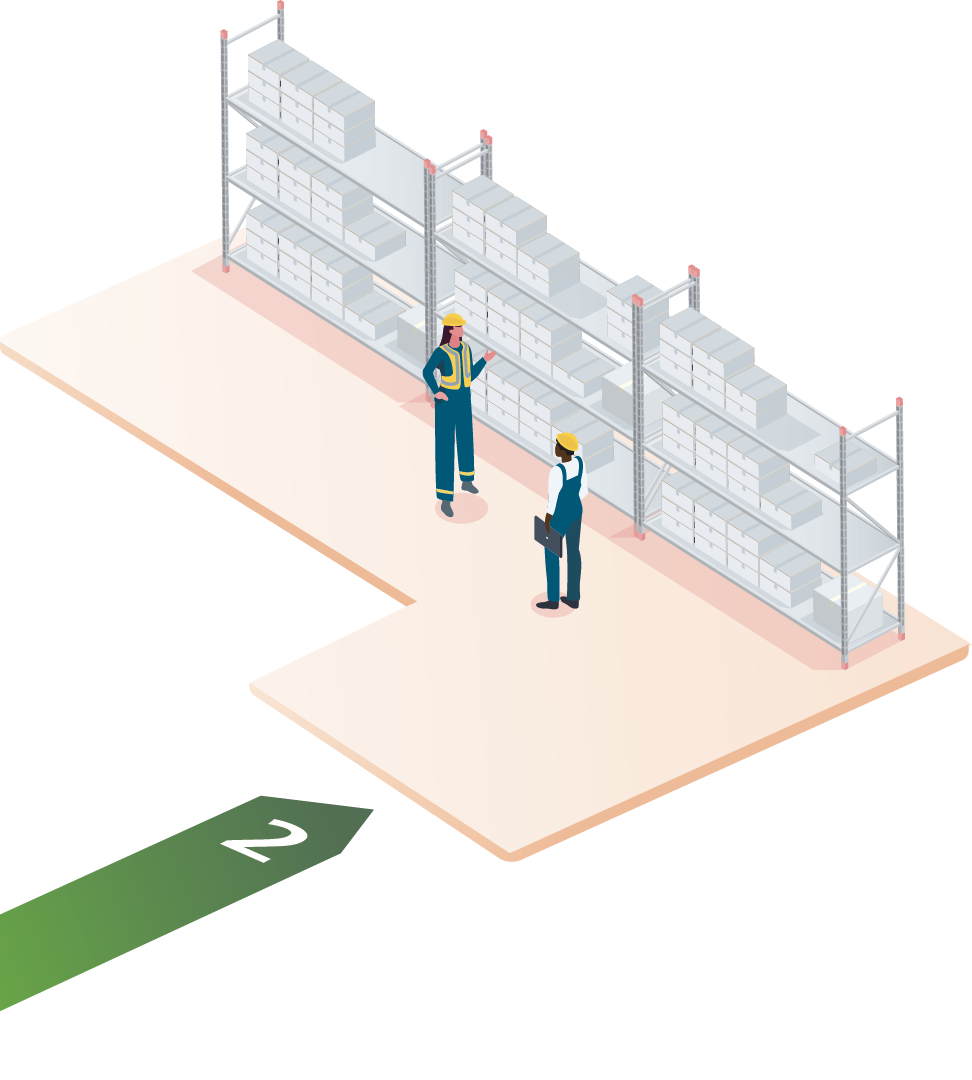
DOCUMENTATION AT THE READY
“What also makes global life science projects so extremely complex is that they operate in a highly regulated environment,” Philipp Zumoberhaus states. For a company to obtain market approval, it must fulfill the Good Manufacturing Practice (GMP) guidelines in place to ensure that medicines are produced consistently according to stipulated quality standards. Qualification of plants and validation of processes are integral to that. Measurement technology likewise has standards to comply with. Here, the global program ensures that EPCs and end customers receive the complete and traceable documentation they will need for factory acceptance tests and inspection by government agencies. Included in the scope are a variety of certificates concerning, for example, the origin of the materials used or a particular surface roughness. Philipp Zumoberhaus points out: “Our industry experts are well-versed in the requirements and action everything at the right time.”
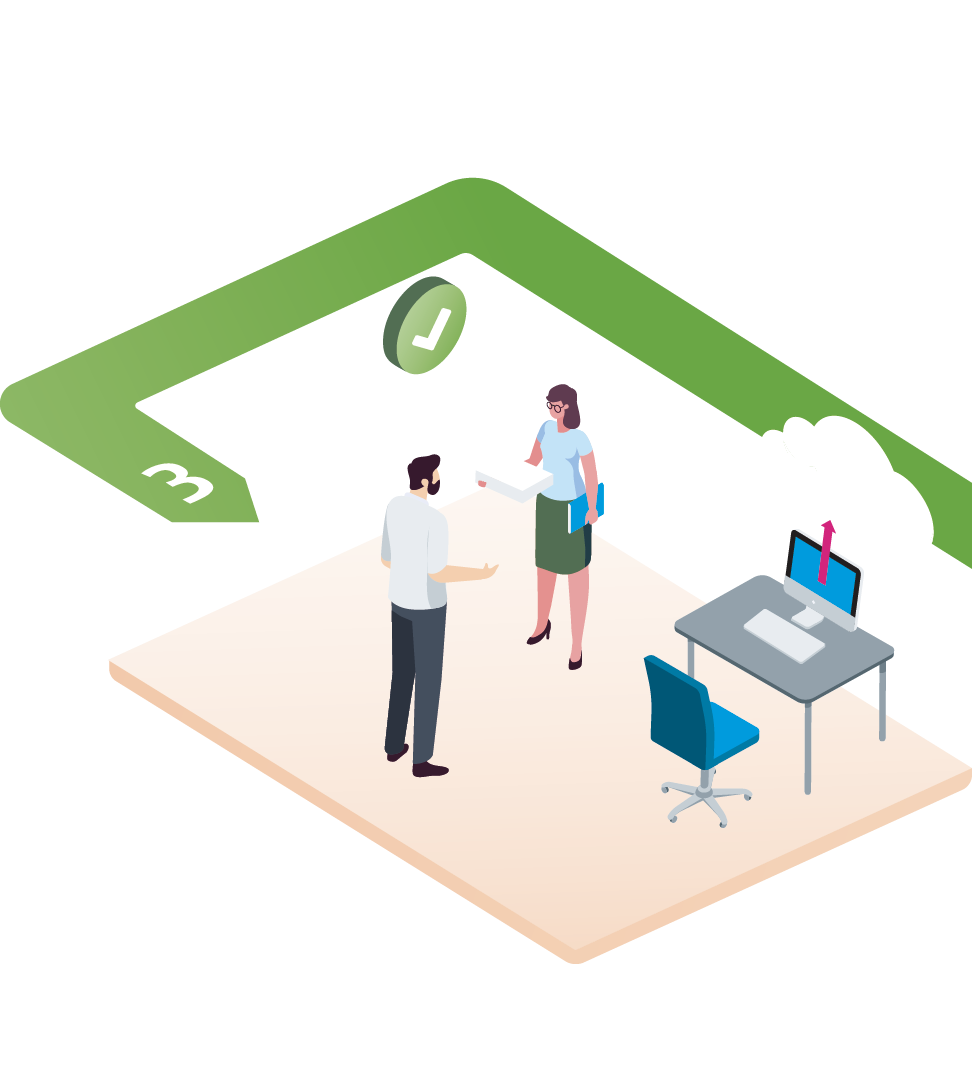
WAREHOUSING WITH DELIVERY ON DEMAND
Endress+Hauser recently supplied several thousand instruments – everything from flow measuring technology right up to Raman spectroscopy – for a new biopharmaceutical production rollout that involved EPCs in multiple countries. There were likewise several thousand instruments sent directly to end customers in Asia who would be handling the ancillary processes. “On the customer’s behalf we also handled local warehousing, building storage capacity for that purpose,” says Philipp Zumoberhaus. The warehousing facility was validated according to GMP guidelines. Employees were trained in compliance with standard operating procedures. Processes for incoming and outgoing goods were digitalized to ensure precise traceability. Then every incoming measuring instrument was checked for conformity, including verification that its documentation was all present and correct. When the customer was ready to have measuring instruments installed, Endress+Hauser shipped them on demand to the plant construction site – at times as many as 1,500 units per month.

READY TO GO IN JUST 18 MONTHS
The project also demonstrates the efficiency benefits that the Endress+Hauser global program delivers: “It took just a year and a half from the initial customer meeting to plant handover, with five Endress+Hauser product centers and six local entities involved,” Philipp Zumoberhaus reports. Throughout this time, his team kept an eye on progress and costs, implemented changes quickly and provided advice to everyone involved. It was the kind of collaboration that convinced the customer to involve Endress+Hauser again when they construct more plants.
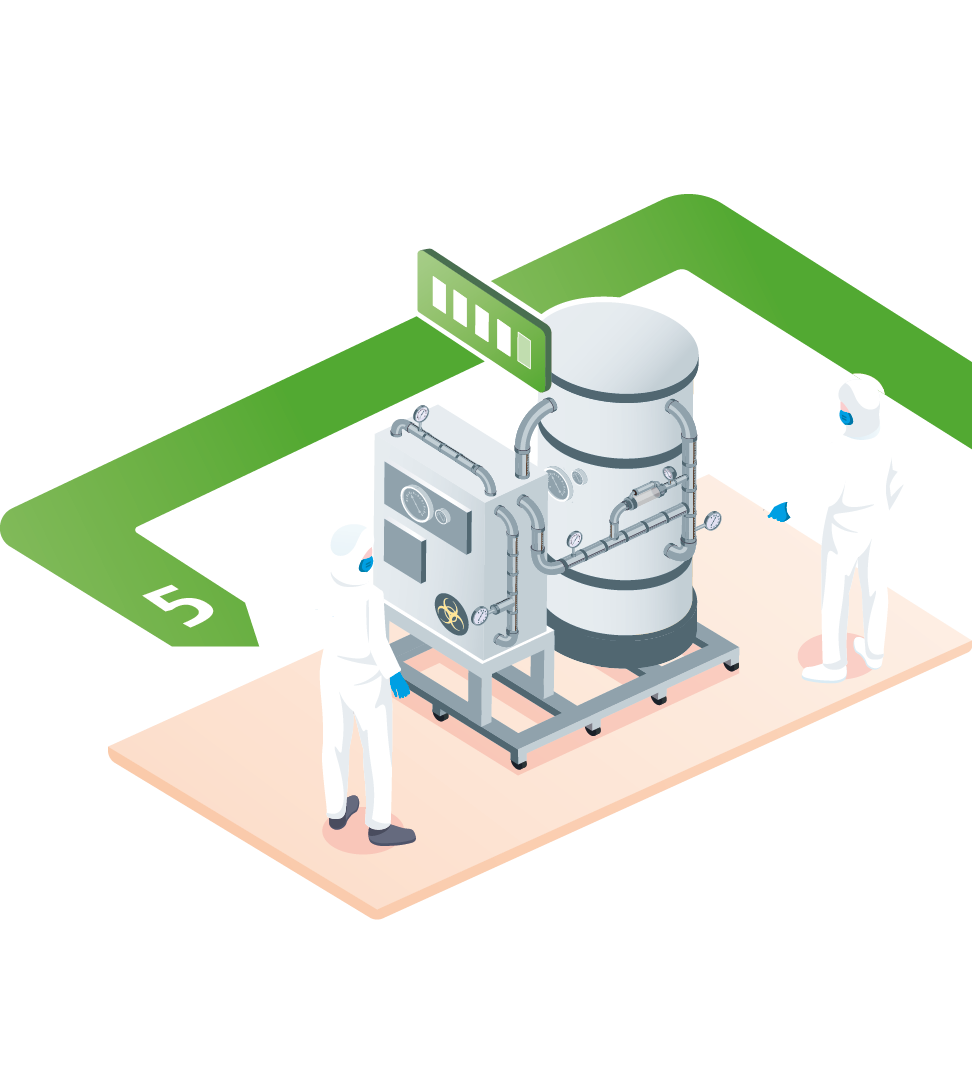
Published 04.03.2025, last updated 09.03.2025.
Dive into the world of the process industry through new exciting stories every month with our «changes» newsletter!
Subscribe to newsletter