Creative in a crisis
The pandemic brings significant challenges, but for modern analytical technology and remote monitoring, it becomes a springboard. Steve Beeston of the engineering and consulting firm Wood shares his experiences.
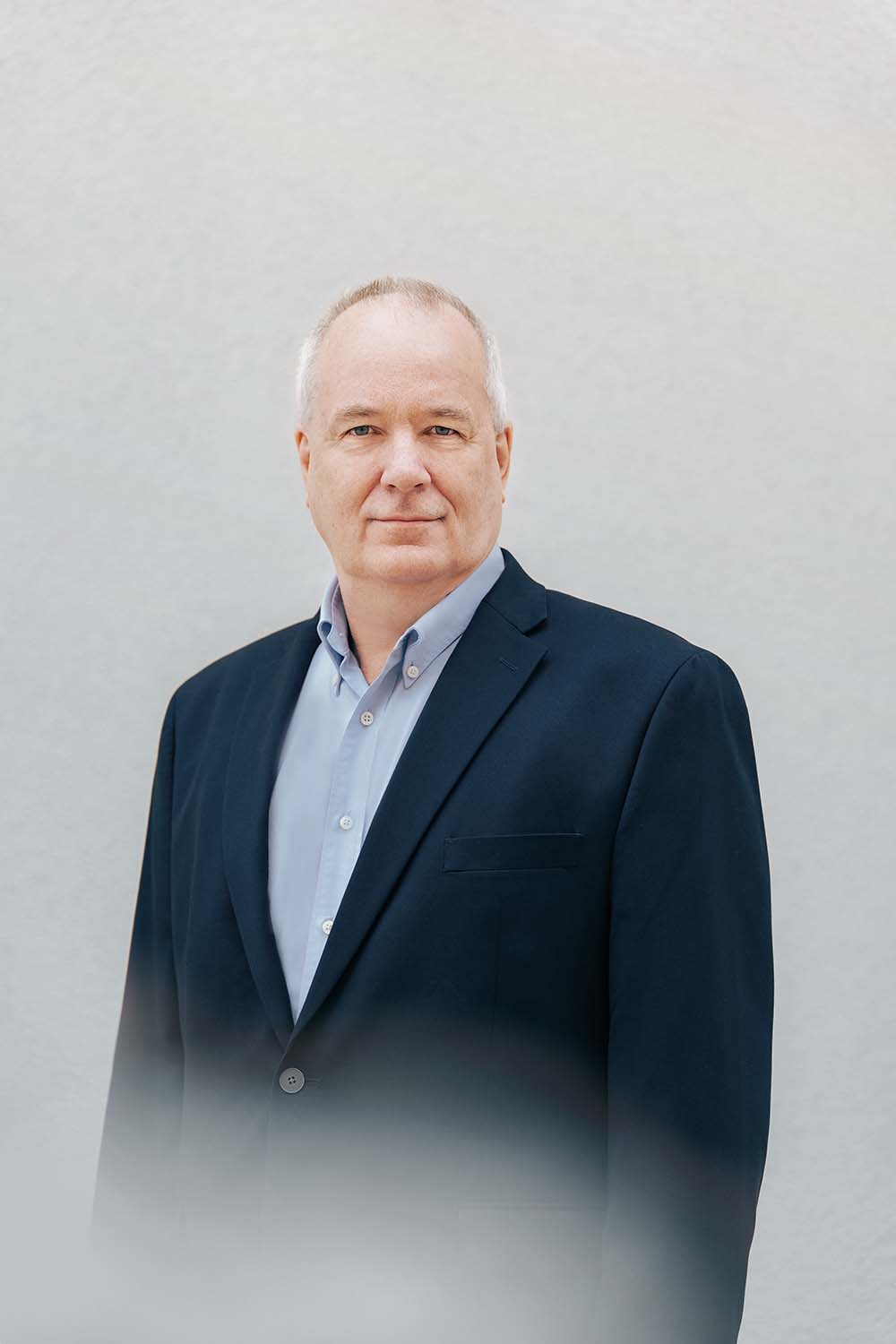
Wood is a market leader in developing and delivering delayed coking units for oil refineries. You are leading a team of highly specialized engineering experts developing technological solutions. What was the biggest challenge posed by Covid-19?
One of the major challenges we faced was transitioning all employees to working from home. We made sure everybody had laptops with good internet capability to access the engineering software. Working remotely with clients in different time zones has been a tremendous challenge. We hardly have time for discussion, and in addition, it becomes very cumbersome to review piping and instrumentation diagrams, drawings or process flow diagrams on laptop screens. There is no substitute for the productivity brought by face-to-face meetings where everything can be explained in detail!
Have you been able to utilize new technologies during the pandemic?
We had some delayed coker start-ups that the subject matter experts monitored remotely utilizing virtual reality goggles, cameras and smartphones. It is of course not ideal because of the missing interaction with the operations personnel. This is especially important for training the operators.
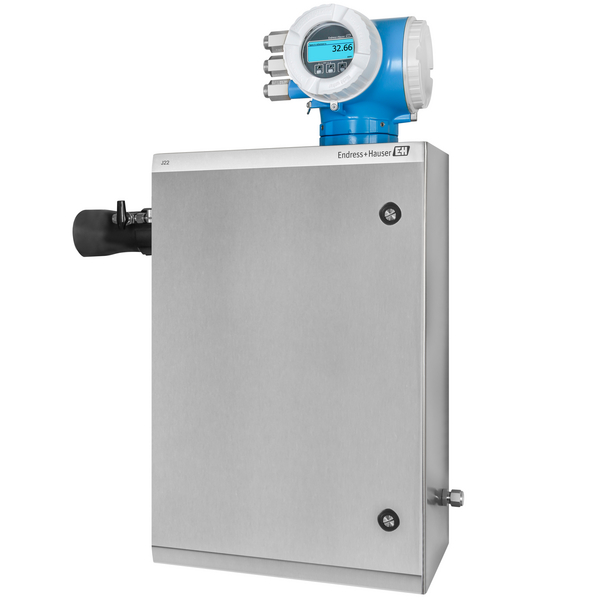
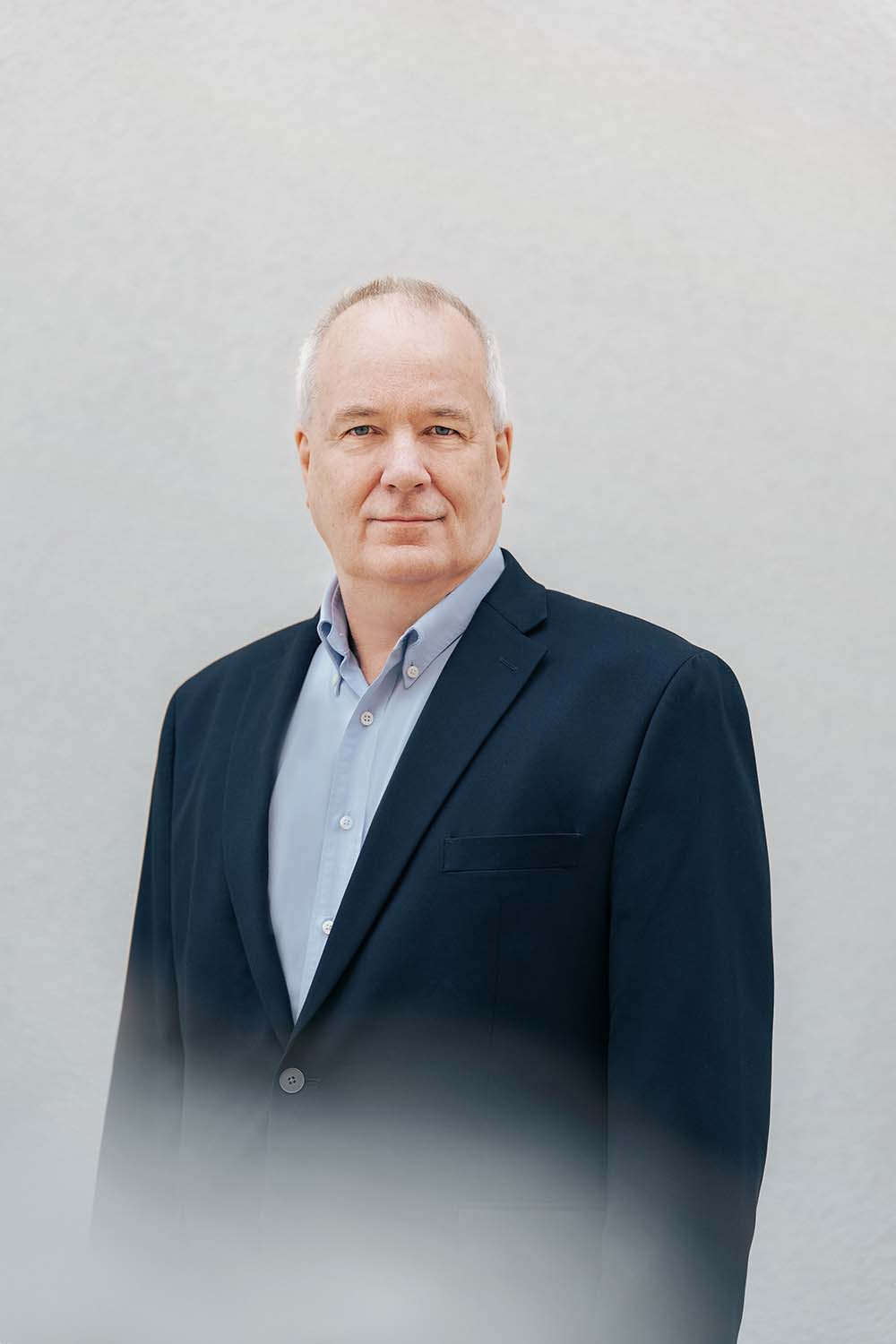
Steve Beeston is Vice President and Head of Process Technology Licensing at Wood. The group is a global leader in consulting, projects and operations solutions in the energy and built environment, and employs around 45,000 people in over 60 countries.
Are the current challenges driving technological advancements in your field?
Definitely! We see several changes on the horizon. For example, there is a move towards utilizing the concept of digital twins, and there is also an increasing demand for remote monitoring for cokers and de-asphalting units. The key to this is performing real-time data measurements such as relevant quality parameters that were previously recorded in the laboratory. Endress+Hauser has a strong portfolio of analyzers with technologies such as Raman and tunable diode laser absorption spectroscopy. That is why we discussed with Endress+Hauser how we could obtain this data using these measurement principles. If we capture parameters live, we can monitor and optimize plant operation in real time.
Would you say the crisis presented an opportunity to initiate improvements?
When you must do things differently, it promotes creativity. The home office also has advantages: Since we traveled less, we were able to use the time for further technological developments and process improvements. I’m sure that modern analysis methods and remote monitoring will make our business even more efficient. However, the pandemic will bring significant changes in other areas. There will be a more flexible attitude towards home offices and hybrid solutions to interface with clients. Keeping virtual teams together will also require leaders who set the appropriate context.
How would you describe your collaboration with Endress+Hauser during the crisis?
Knowing the staff on both sides is important and very helpful. We have been working together for decades; Endress+Hauser is one of our key suppliers for various measurement solutions. That makes it easier to move things forward together!
Published 05.05.2021, last updated 20.06.2022.
Dive into the world of the process industry through new exciting stories every month with our «changes» newsletter!
Subscribe to newsletter