Turning point
Like a catalyst, the coronavirus pandemic has accelerated and reinforced developments in the process industry. Digitalization is leaping forward and economic balances are shifting. And once the immediate crisis has been overcome, long-term challenges will push their way back on to the agenda.
Arthur Zhang vividly recalls the moment when he realized the virus would change his business. It was 22 January 2020, five days before the Chinese New Year festivities, when the doctor responsible for his residential district called him. “Is it correct that you returned from Wuhan the day before yesterday?” Arthur Zhang did indeed travel to Wuhan for a customer meeting – and thus received an urgent recommendation to stay at home for two weeks. He used the time to reorganize his company from the confines of his apartment.
Arthur Zhang is managing director of the Endress+Hauser sales center in China, where he is responsible for the Group’s single largest market. After the outbreak, he instructed around 70 percent of more than 450 employees to work from home, then organized medical protective masks for the remaining people. What followed was a demanding quarter, not least in economic terms.
A BOOST FOR DIGITALIZATION
Just under a year later, China’s economy is booming again. Growth would have been higher still were it not for a shortage of shipping containers that restricted export capacity. Does that mean everything is back to how it was before the pandemic? Arthur Zhang, who has worked in the process industry for more than three decades, begs to differ. “In the new normal, we’re still living with a high awareness of the risks.” Although meetings with customers are being held again, and ever more employees are returning to the office, digital meetings are now part of the daily routine.
The digitalization boost has touched all areas, including industrial production. “The pandemic made the value of smart factories very clear,” reports Arthur Zhang. Many customers are investing in automation, IT and communication technologies. “In many cases, the sensors are initially being deployed to remotely monitor process conditions,” says the managing director. “Customers then realize that the data this makes available can be used to positive effect on process safety and product quality.”
Robert Helminiak from the Society of Chemical Manufacturers and Affiliates (SOCMA) in the United States confirms this assessment. “The pandemic has magnified the demand for further integration of components and plants in the Internet of Things, digitalization of data processing and cybersecurity,” says the vice president, whose association represents more than 200 companies in the specialty chemicals industry. However, there is still no agreement on how far digitalization needs to go and how fast it should happen.
“The pandemic has magnified the demand for further integration in the Internet of Things, digitalization of data processing and cybersecurity.”
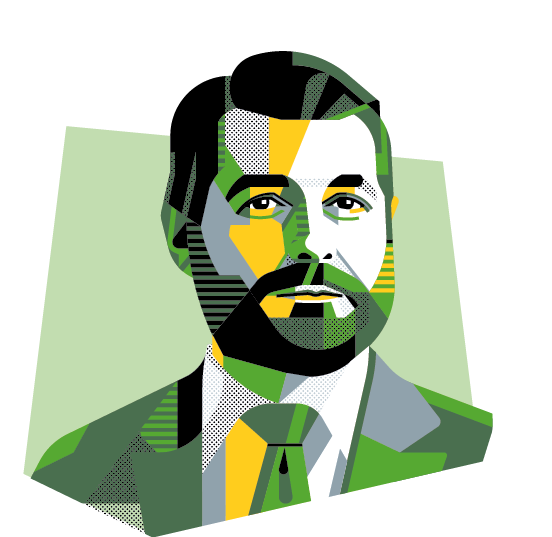
Robert Helminiak,
Vice President, Society of Chemical Manufacturers and Affiliates
OLD CHALLENGES, NEW SOLUTIONS
Digitalization of the process industry could also help in other areas, for example in coping with demographic change. “Many of the experienced chemists and process engineers, who can monitor the plant almost by sight, will be heading into retirement within the next few years,” says Thomas Hucht, managing director of engineering services company plantIng, a subsidiary of the Able Group. “Given that there is a lack of young talent, it would be smart to digitally model the experience these experts have acquired.”
Generally speaking, Covid-19 has had little effect on the significance of global megatrends. At best, the crisis has led to increased emphasis or provided additional momentum to these developments. Although worldwide CO₂ emissions have fallen seven percent in the past year, this will offer mankind no more than a brief respite in the battle against climate change. For chemicals and other segments of the process industry, in 2020 the global decisions on climate protection were at least as consequential as the pandemic. While the economic repercussions of the pandemic are mostly short term, CO₂ neutrality often means a complete retrofit of existing production processes.
“The substitution of hydrocarbons, as well as the introduction of a circular economy, are the greatest challenges of the future,” emphasizes Professor Kurt Wagemann, managing director at Dechema, a Germany-based expert network in the area of chemical technology and biotechnology. The European Union believes the key to climate-neutral industrial production lies in green hydrogen, strategically setting a corresponding course in 2020. The plan now is not only to steer investment programs toward a long-term restructuring of the energy industry but to provide a boost to energy efficiency and advance electromobility on the continent.
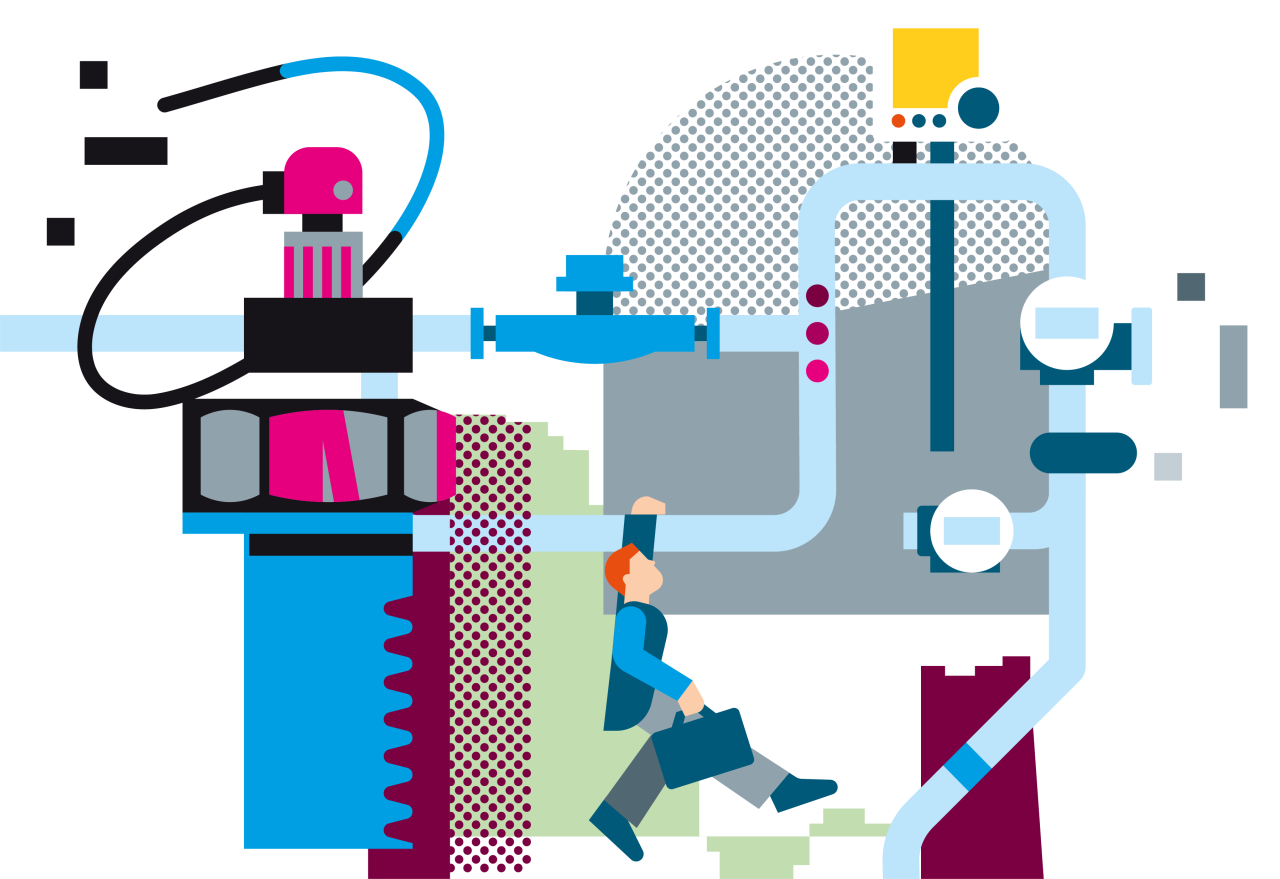
NEW GREEN DEAL
It at least appears that the major economic blocs are once again pulling together in terms of climate protection. While Europe tightened its climate goals for the year 2030, US President Joe Biden, on his first day in office, signed an executive order to have the country rejoin the Paris Agreement, and Chinese President Xi Jinping announced that his country wants to be climate-neutral by the year 2060. A harbinger of closer cooperation in tackling the major tasks of the future?
“The concerted response to Covid-19 offers renewed hope that international science, technology and innovation cooperation can help provide solutions to other global challenges,” writes the Organization for Economic Cooperation and Development (OECD) in a report full of optimism. In record time, researchers developed vaccines effective against the coronavirus. And working at great speed, pharmaceutical companies vastly expanded their capacity to ensure safe production of the vaccines. Industry is not part of the problem, but the solution.
Triggered by temporary supply bottlenecks during the pandemic, complaints about the global flow of goods and value chains are being voiced in Europe and the US. According to a survey by Euler Hermes, 94 percent of all companies suffered supply chain disruptions last year. Other studies claim figures between 56 and 80 percent. The reasons vary, from rapidly rising demand and production stoppages, to closed national borders. But one thing seems clear: our highly interconnected global economy showed how vulnerable it is.
“Globalization will continue to spread; there is no turning back. And China will be part of the system.”
Arthur Zhang,
Managing Director, Endress+Hauser China
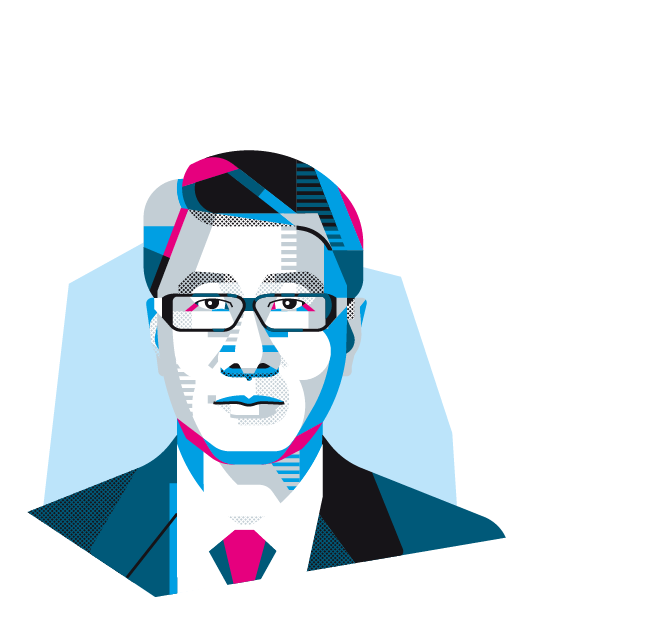
GLOBAL DEPENDENCIES
Will globalization now be rolled back? Will value creation become more regionalized? “With the pandemic fracturing the global supply chain, companies can no longer afford to rely on a single provider of an input,” emphasizes Robert Helminiak from SOCMA. On the other hand, the bottlenecks could have created new opportunities as well. “Pioneering new products that are integral in making our lives safer, healthier and more sustainable will continue to be a top priority for the industry,” predicts the US expert.
On the other side of the globe, Arthur Zhang considers the idea of regional independency “overrated”. He believes that “globalization will continue to spread; there is no turning back. And China will be part of the system”. The country has indeed grown economically more powerful as a result of the pandemic, while also expanding its political influence by achieving a breakthrough during the negotiation of the Comprehensive Agreement on Investment with the European Union. And as a member of the Regional Comprehensive Economic Partnership, China is part of the world’s largest free-trade zone that stretches from the Himalayas to New Zealand and encompasses 15 countries with more than 2.2 billion people.
Be that as it may, supply chain robustness is likely to receive more attention in the future. The pandemic highlighted the value that redundancies and reserves have for companies. And when Arthur Zhang thinks about the further development of the Chinese sales center, there is one thing he will always be aware of: “The virus illustrated how everything can change from one moment to the next. And that we always have to be prepared for it to happen.”
Published 01.02.2021, last updated 17.11.2022.
Dive into the world of the process industry through new exciting stories every month with our «changes» newsletter!
Subscribe to newsletter