The treasure trove
When Endress+Hauser began building a centralized instrument database 20 years ago, the Internet of Things was still a distant vision. Michael Herzog, a founding father of the Common Equipment Record, explains how it came into existence and why the huge volumes of data are a genuine treasure trove today.
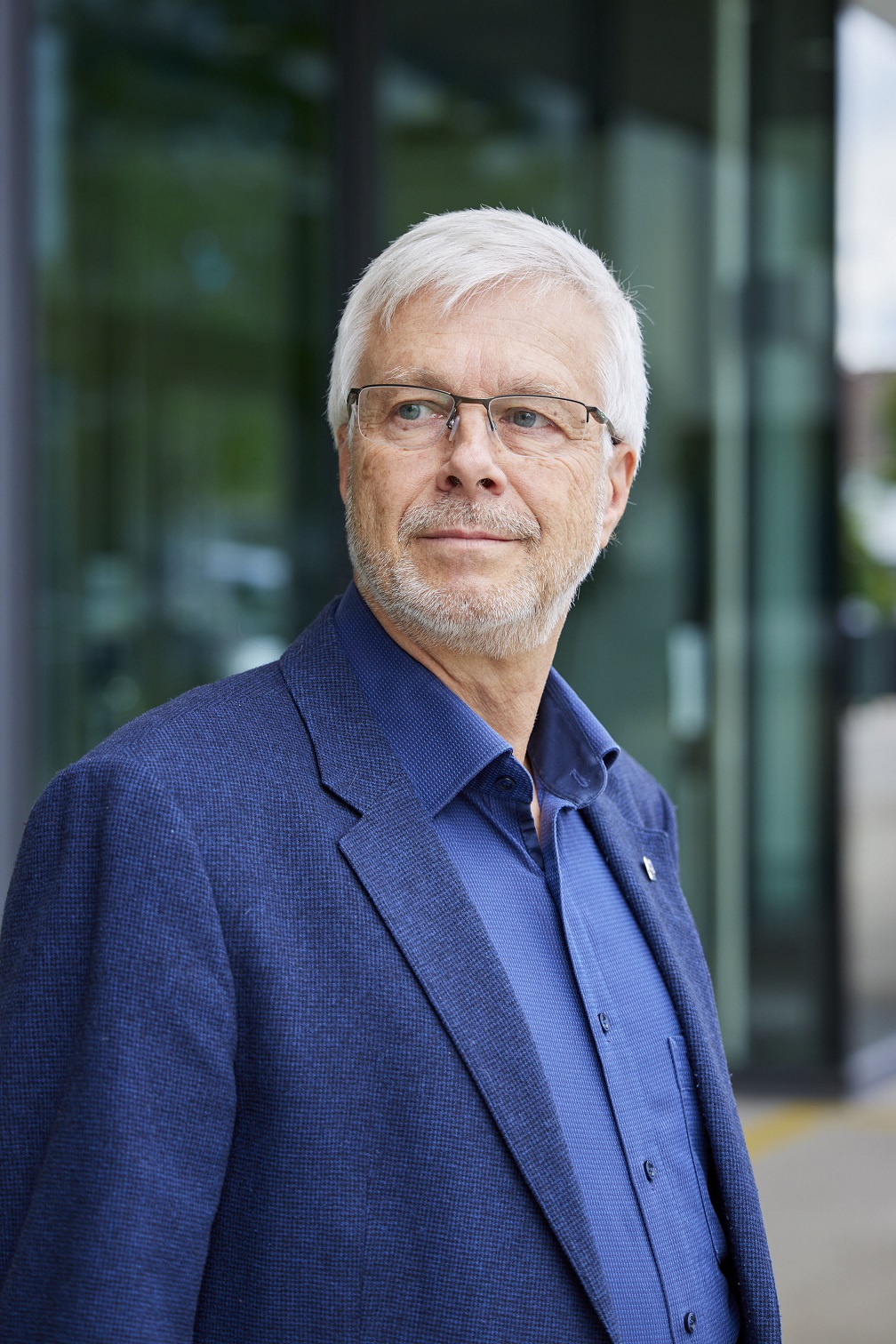
SERVICE
You mean to tell me that Endress+Hauser has been systematically and centrally gathering instrument information for 20 years? I hear this astonished question quite often, because many other companies are only now beginning to establish such databases. We can thank our service orientation for the fact that we are a pioneer in this field. Back then we realized it would be complicated if customers could no longer find a calibration certificate, one of the most important instrument documents. With the serial number in hand, they had to call the responsible sales office, which in turn contacted the respective production facility, where the certificate had to be searched for – and then everything took its return journey to the customer. The archive was already huge at that time, even though back then we were producing only a small fraction of today’s 2.7 million sensors!
The Common Equipment Record allowed us to eliminate the mountain of paper. With the help of interfaces, our own proprietary system and a new standard, we first stored the certificates and then more and more information about the instruments. That information was now available in-house around the world – digitalized and stored in one location – which meant that the sales offices could answer customer inquiries faster. Today the system contains information on more than 50 million instruments: core data such as serial number, production date, documentation, 3D drawings, replacement parts lists, latest software and all the service reports. So, more than just a ‘register of births’. The database reflects the entire lifespan of our measurement instruments. And today it also helps in creating digital twins, for example.
I must admit that 20 years ago, we approached the whole thing very intuitively. But we were confident that the information would create a lot of benefits. Indeed, as time progressed and the volume of data continued growing, it turned out to be a real treasure trove and a vast source of knowledge. For example, it wasn’t long before the data was being used to better advise customers and generate new quotations. On top of that, we gave customers access to their own product data on a single platform. With this transparency, we not only built a lot of trust but created new benefits as well. Since then, plant operators have been able to manage their products over the entire life cycle and thus optimize their processes. And today, instrument traceability helps quality management to create a high degree of transparency regarding product quality in the field.
We have now reached a point where we have so much data that we can use new technologies to analyze it and identify patterns. For instance, we can see how an instrument behaves in the field over a long period of time. And all without having to generate additional information, for example via service personnel. This brings us back full circle to the inception of the Common Equipment Record. It will also help us to further improve our quality and our service, in totally novel dimensions. I’m curious to see what else we can gain from our treasure trove of 50 million instruments!
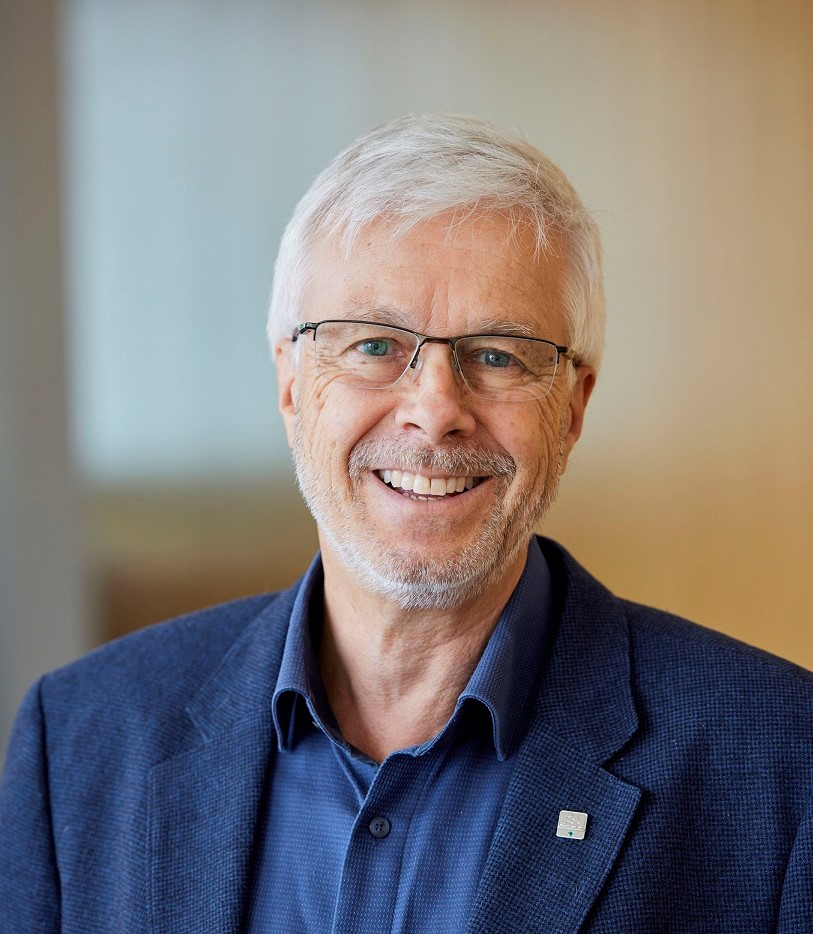
Published 25.01.2023, last updated 13.02.2023.
Dive into the world of the process industry through new exciting stories every month with our «changes» newsletter!
Subscribe to newsletter