Reaching our goal together
Supply chain decarbonization is a must for Endress+Hauser to achieve its aim of climate neutrality by 2050. Sustainability expert Janaina Fagundes explains how everyone involved is working together to achieve this objective.
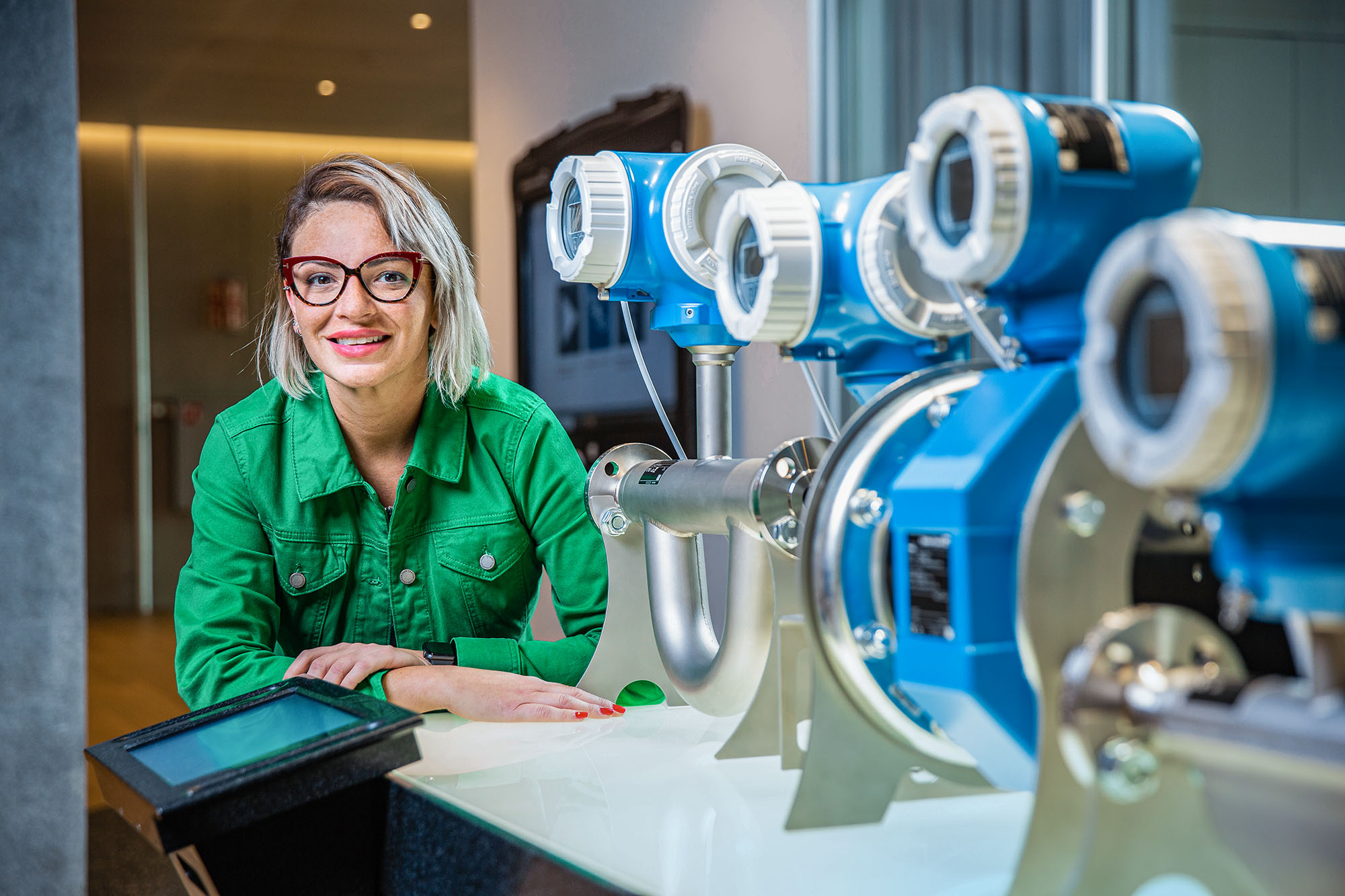
Like the entire manufacturing industry worldwide, Endress+Hauser has
embarked on a journey towards greater sustainability. We want to pivot away from fossil fuels and shape our business and production processes to be more climate friendly. We and many other companies have realized that the largest share of our carbon footprint comes from greenhouse gas emissions alongnupstream and downstream value chains in Scope 3. Materials procurement alone accounts for one third of the footprint, because a lot of steel and aluminum goes into our measuring instruments.
So for us to become climate neutral by 2050, every other stakeholder in the supply chain must similarly reduce their emissions to net zero. By 2034, we aim to emit 35 percent less CO2 in Scope 3, where our suppliers also contribute. Endress+Hauser Flow, the competence center for flow measurement technology, has accordingly approached suppliers whose goods reach us carrying a particularly high emissions load. We are currently finalizing agreements with them on the percentage by which they can reduce their carbon footprint by 2034 and drawing up joint action plans. Those include suppliers reporting specific measures being taken – for example, whether they are switching to renewable energy, implementing process improvements or setting up closed-loop
heating systems.
Creating transparency
Like all the other Endress+Hauser competence centers, we will have calculated the carbon footprint of our top products by the end of this year. This involves taking stock of the impact of the individual components. It is a highly complex procedure when one considers an instrument such as Prowirl F 200, a vortex flowmeter.
425 parts from 69 direct suppliers and many subcontractors go into its manufacture. Due to the high complexity and variety of data, calculation inaccuracy is likely to be 40 percent. Nevertheless, this product-related footprint becomes a valuable tool: we can see which components have a particularly high CO2 load and hence what our priorities should be in terms of materials procurement and product design.
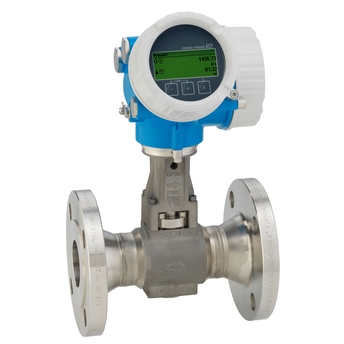
In our company, as in the manufacturing industry as a whole, we are experiencing the transformation day by day. Sustainability is becoming a key factor for successful business, not least because of the reporting requirements incorporated into various pieces of legislation. Moreover, under the EU Carbon Border Adjustment Mechanism there will be levies on imports of CO2-intensive goods starting in 2026. This means companies that have not cut back on CO2 in their manufacturing will lose competitiveness.
Europe, India and China have industry forums at which we discuss these issues with our suppliers in person. It is about learning and progressing together. Our long-standing focus on dependable relationships gives us a good starting position. I see some pleasing momentum here: At the beginning of 2023, many suppliers still did not have this topic on their radar. Now, just one year later, I feel things in motion. It’s like a stone dropped into water, creating ever-wider circles.
Published 04.02.2025, last updated 17.02.2025.
Dive into the world of the process industry through new exciting stories every month with our «changes» newsletter!
Subscribe to newsletter