From problem to product
Greenhouse gas emissions cannot be avoided in the cement industry. Is that a bad thing? Not for Holcim Germany. The building materials manufacturer sees it as a great opportunity for the future.
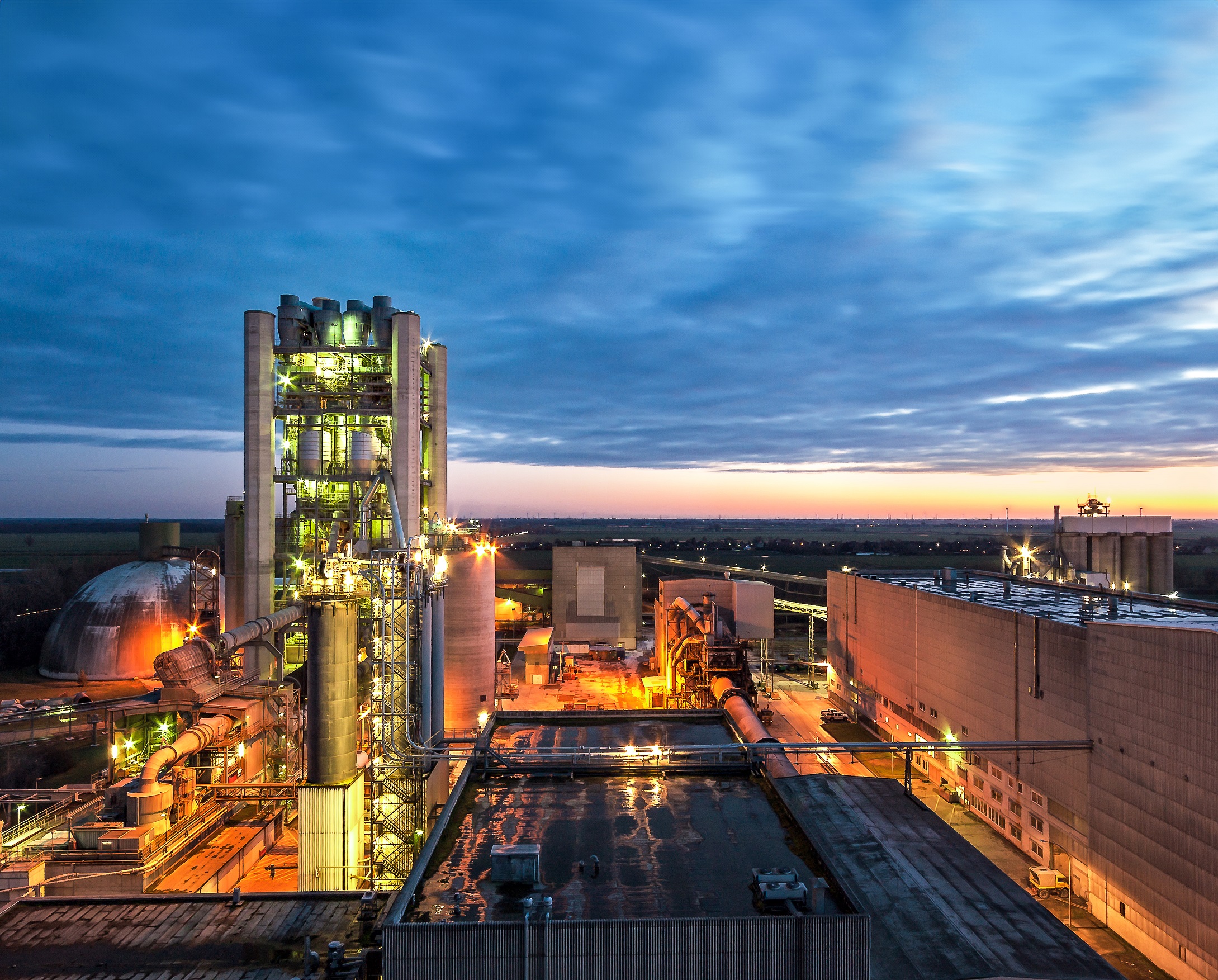
CARBON CAPTURE
To see into the future of the cement industry, travel to northern Germany and Holcim’s operation in Lägerdorf. Rich chalk deposits there have been used for more than 160 years to produce the coveted binding agent for concrete around the clock. This amounts to 1.5 million tonnes annually, in the process releasing 1.2 million tonnes of CO2 into the atmosphere. The cement industry is one of the world’s largest greenhouse gas emitters. But this is set to change, at least in Lägerdorf. “We want to be one of the very first cement works to become climate neutral in the next six years,” says Arne Stecher.
Arne Stecher is head of decarbonization at Holcim Germany. In his 25 years there in management roles, he has never seen anything like the current situation. “We are currently in the midst of a global transformation, with fossil value chains disappearing and new green ones emerging. All companies must change,” says Arne Stecher. Not just to save the climate, but also to safeguard their own future. But while many industries can go green by switching fuels or processes, that does not work in cement manufacturing: two-thirds of emissions arise from burning the cement clinker in a kiln. This process decomposes chalk, or calcium carbonate (CaCO3), into calcium oxide (CaO) and CO2. “There will never be cement without carbon dioxide,” says the process engineer.
In 2016 the Paris Agreement on climate change had just come into effect. This led top managers at Holcim, one of the world’s leading building materials groups, to ask themselves two questions: How can we economically capture millions of tonnes of unavoidable CO2? And what will we do with it then? “We scanned the market and the research on carbon capture technologies, identified 80 interesting approaches and initiated 50 pilot projects worldwide,” says Arne Stecher. “This will produce maybe 25 real-life industrial projects, and a handful of technologies will ultimately emerge.”
All three of the company’s German plants are implementing pilot projects. In Lägerdorf, construction will begin in 2024 of a new kiln line using the innovative oxyfuel process, which involves blasting pure oxygen into the combustion chamber where clinker is made, in place of the atmospheric air commonly used to date. The resulting flue gas stream is almost entirely ultrapure carbon dioxide, which is simple to collect and use. “However, there are modifications and new construction involved, as well as investments costing hundreds of millions of euros, so this integrated approach only works at large sites with long-term raw material availability,” says Arne Stecher.
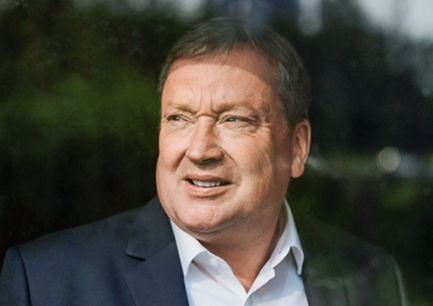
Arne Stecher is head of decarbonization at Holcim Germany.

In Beckum, Endress+Hauser handles the measurement side of testing the latest amine scrubbing technology.
“CO2 will be a coveted raw material in future"
Arne Stecher
head of decarbonization, Holcim Germany
ECONOMICAL USE
At other sites, end-of-pipe technologies are set to be upgraded: The process will remain unchanged, and the CO2 will be separated from the flue gas stream downstream. To do this, at the other two works Holcim is developing new amine scrubbing and membrane technologies with research and technology partners. Endress+Hauser is involved in this effort with instruments to monitor process safety and efficiency. “Carbon capture is nothing new for us. In the oil and gas industry, carbon dioxide has long been separated for use in oil recovery. We have extensive application knowledge in this area,” Frederik Effenberger, industry manager for decarbonization at Endress+Hauser, explains. The aim of the tests is to achieve the highest possible separation rates and high purity with minimal expenditure of resources.
So, does that make decarbonization first and foremost a technology issue for Holcim? “No,” says Arne Stecher. “The major transition is taking place beyond our own works, because to use the CO2 we have to build new value chains and think in terms of material cycles. For this we need partnerships.” At Lägerdorf, for example, oxygen for the oxyfuel process will come from the electrolyzers of other companies that split water into hydrogen and oxygen using green electricity. Holcim and its partners seek to process the CO2 for the petrochemical and other industries, which in turn will use it together with hydrogen to produce e-fuels, e-chemicals and e-methanol. The CO2 could also go directly to the chemical industry as a primary feedstock. Making all this happen requires logistics, infrastructure and buyers, as well as carbon dioxide in varying grades of purity. “The material streams must flow continuously,” says Arne Stecher, who was head of purchasing at Holcim for 11 years. “That again makes supplier partnerships one of my key focal points.”
8%
of global CO2 emissions are produced by the cement industry.
COVETED RAW MATERIAL
Holcim Germany, says the decarbonization expert, is a first mover in carbon capture and utilization (CCU), both within the group and for the industry as a whole. Arne Stecher is convinced that the pioneering role is worthwhile: When he first started taking interest in CCU, a ton of CO2 cost 20 euros in European emissions trading; in 2022, the price was 80 euros. “The time has already come where it makes sense to invest in avoidance technologies,” he emphasizes. As a first mover, Holcim also occupies an emerging market: the market for CO2. “The new green value chains will not function without CO2; the chemical industry alone will always need a carbon source,” says the head of decarbonization. And that is something Holcim can supply in the immense quantities required. CO2 will go from being a problem to a product. “I believe that CO2 will be a coveted raw material in future,” says Arne Stecher.
Published 20.12.2023, last updated 12.01.2024.
Dive into the world of the process industry through new exciting stories every month with our «changes» newsletter!
Subscribe to newsletter