Clear signals
Field devices with Heartbeat Technology have a sense of what’s going on: they intelligently use sensor data in addition to the primary measured value to provide deep insights into the instrument and the process being monitored. The benefits are huge – even predictive maintenance becomes possible.
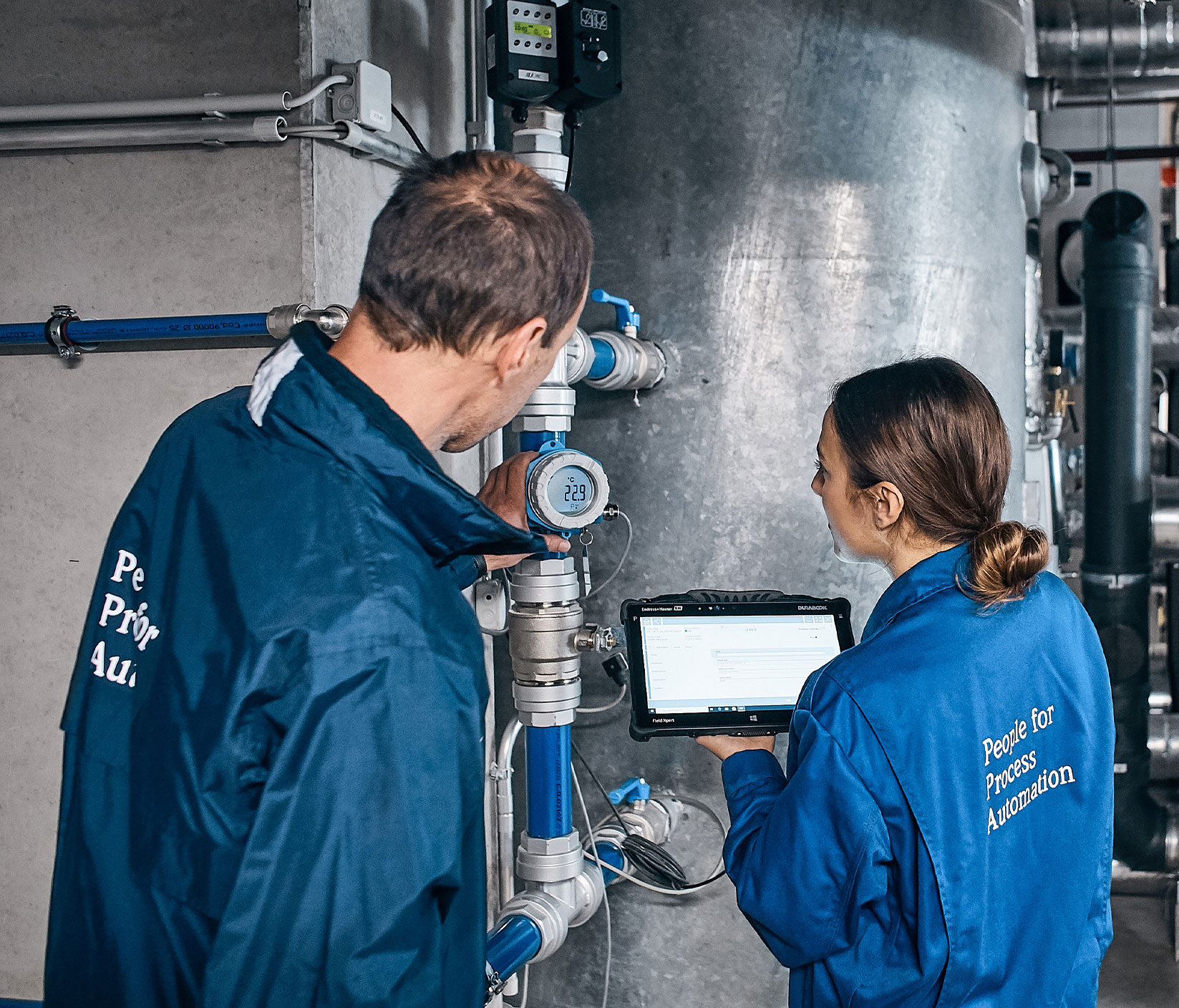
Smart Sensors
A shutdown of a production plant is always costly – especially if it’s unplanned. According to a study conducted by AI specialist Senseye, large industrial plants lose on average 323 hours of production time annually. Average losses caused by downtime amount to 170 million dollars per plant. So it’s no wonder that three out of four companies have declared predictive maintenance as a strategic goal.
The question is, how can a plant operator know early enough that a process is not running smoothly or that there is an issue with an asset? “This is why Endress+Hauser developed Heartbeat Technology,” explains Daniel Persson, Process & Portfolio Manager for Innovation. It is built into numerous measuring instruments for flow, level, pressure and temperature, as well as for liquid and gas analysis. “With Heartbeat Technology, field instruments monitor themselves and even spot changes in the process. This allows for reliable detection of anomalies and timely implementation of corrective measures,” says Daniel Persson.
Heartbeat Technology is based on signals that field devices capture in addition to the primary measured value. “We use these signals for various functions that are integrated directly into the device and provide plant operators with practical added value,” reports Daniel Persson. All those functions provide detailed insights about the instrument and the process, which help to increase plant availability and reduce operating costs. With the Heartbeat Diagnostics function, for example, instruments continuously check themselves in the background and report their status. In the event of instrument failure or disturbed process conditions, they provide clear information on what is happening right now and what needs to be done next.
With Heartbeat Verification, instrument performance can be verified at the push of a button without interrupting the process. Among other things, it automatically tests whether device components still retain their original reference values and indicates the presence of specific system faults that might impair instrument or process performance. The verification concept is traceable in compliance with ISO 9001 and certified by an external authority. “Self-diagnostics and verification improve process performance, as well as enabling optimization of calibration and test intervals,” says Daniel Persson.
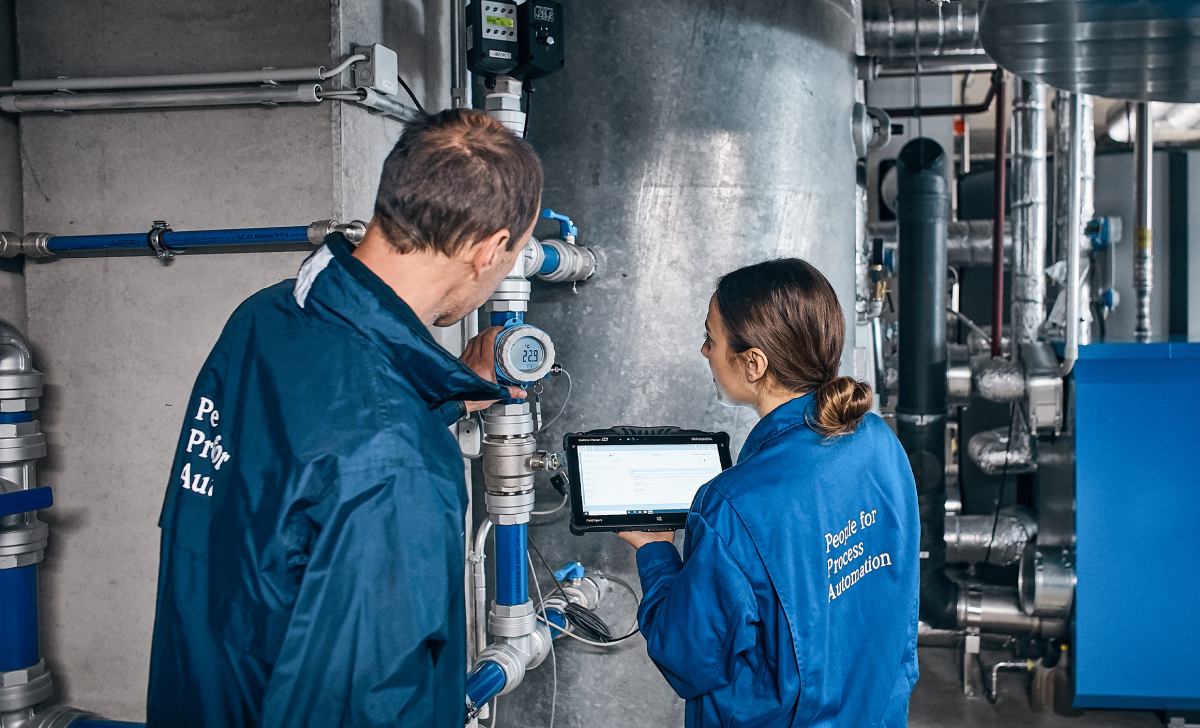
Smart measurement technology uses sensor signals for new diagnostic, testing and monitoring functions.
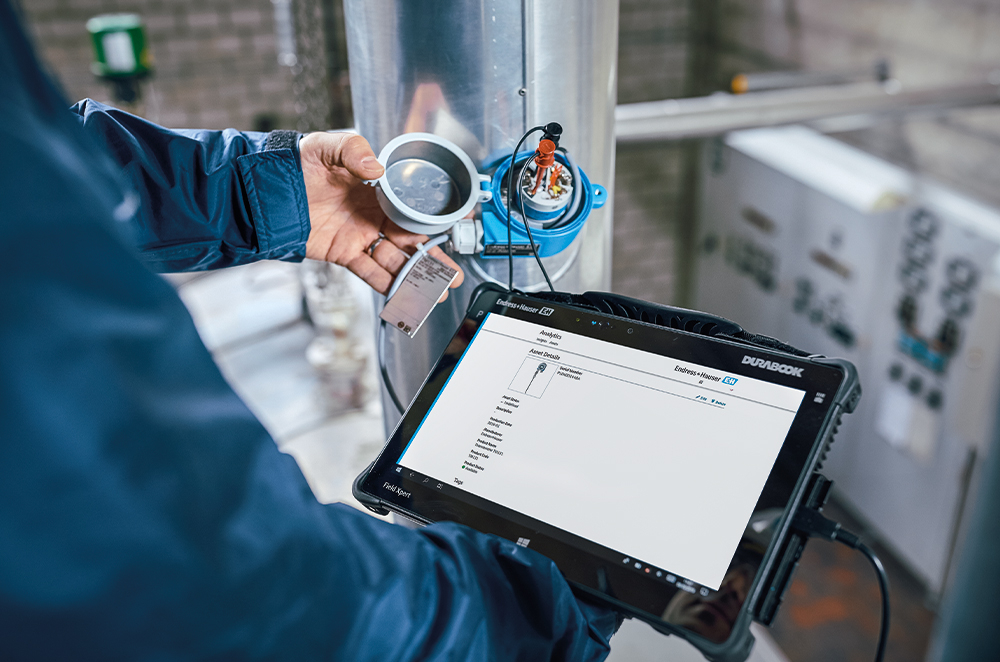
Plant operators gain deep insights into the device and the process – and can thus increase productivity.
Looking for process trends
Even more can be derived from sensor signals, for example whether demanding process conditions are adversely affecting the instrument. “Typical examples include corrosion or abrasion of the sensor components, the appearance of foam in a tank or build-up on the sensor surface. Heartbeat Monitoring functions detect these factors and convert them into easily understandable information about the instrument and the process,” explains Daniel Persson. By observing these parameters over time, plant operators can reliably and promptly identify undesired deviations. Most Heartbeat Technology functionalities are accessible from the instrument. However, the full potential is unlocked when field devices are integrated with the plant infrastructure or even connected to the cloud: processes can be optimized or maintenance activities scheduled for a suitable time.
Published 20.12.2022, last updated 17.01.2023.
Dive into the world of the process industry through new exciting stories every month with our «changes» newsletter!
Subscribe to newsletter