All for One
Hydrogen is considered key to the energy transition and climate neutrality of entire industries. All along the value chain, companies are working on innovative technologies and applications to help this new energy carrier achieve a breakthrough. Here are three examples.
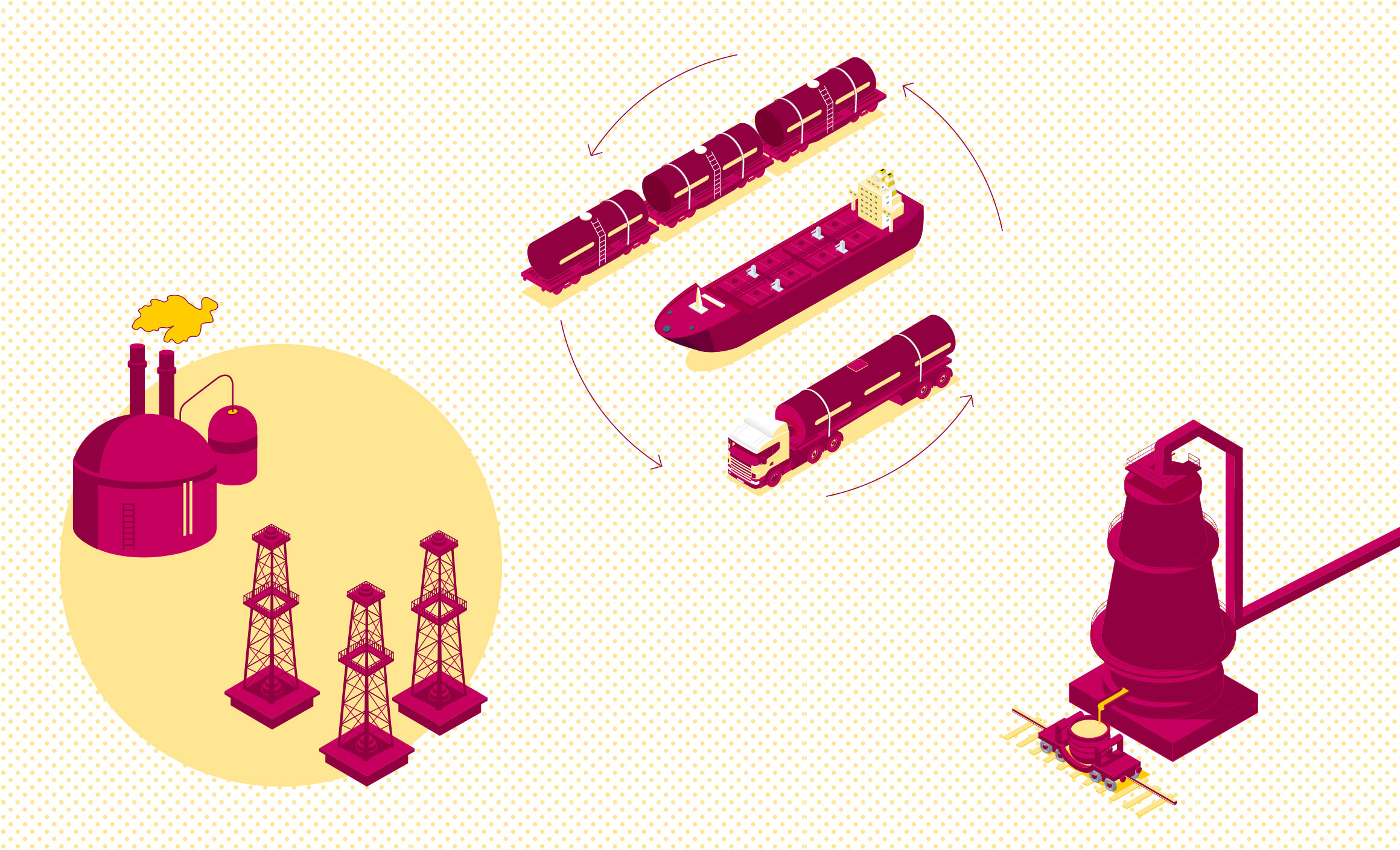

1. Plasmalysis taps new hydrogen sources
To produce climate-neutral hydrogen, the raw material in strongest focus at the moment is water (H2O). Electrolysis powered by green electricity splits it into hydrogen (H2) and oxygen (O). But hydrogen is not just found in water. It is also a constituent of numerous hydrocarbon and nitrogen compounds in wastewater, slurry and gases. Berlin-based company Graforce wants to extract hydrogen from these residual materials: It has developed a plasma electrolysis (‘plasmalysis’) process where a high-frequency plasma field is generated using renewable energy. The plasma field splits the ammonia molecules (NH3) in sewage, or methane molecules (CH4) in natural gas or biogas, into their atomic constituents. “Water bonds H2 more strongly than other chemical compounds. That is why methane plasmalysis can generate a given amount of hydrogen using only one-fifth of the electrical energy of water electrolysis,” Dr Jens Hanke, managing director of Graforce, explains. This cuts production costs considerably. Furthermore, putting methane through the plasmalysis process produces, in addition to hydrogen, solid carbon (carbon black) that finds uses in the construction and steel industries, for example. And with biomethane, CO2 is not emitted from the process but actually extracted from the natural carbon cycle. Running the technology with natural gas as the methane source would be useful in the oil and gas industry, which could consequently avoid flaring off the gas and so achieve its climate targets. The modular Graforce plants are already market-ready. Endress+Hauser supplies the measurement technology for methane plasmalysis. “Plus points include our large portfolio, our application expertise, online technical documentation and the on-site support we can offer all over the world,” Mathias Christ, a technical sales employee of Endress+Hauser Germany, explains.
2. Innovative carriers simplify logistics
It is frequently uneconomical to produce green hydrogen at the place where it is actually needed. So how can it be transported? The gas grid can only blend in a limited amount of hydrogen with natural gas. For seaborne logistics, the highly flammable hydrogen must be liquefied at −250°C; cooling and compression use a lot of energy. Now there is a new solution: liquid organic hydrogen carriers (LOHCs) – unsaturated, generally aromatic hydrocarbon compounds that can absorb hydrogen through a catalytic reaction. H2 bonded in this way is very easy to store and move around under atmospheric conditions, with no pressure or cryogenic containers needed. So transportation can use existing logistics infrastructure for liquid fuels, such as tankers, tanker trucks and tanker wagons. The hydrogen finally gets released from its liquid carrier at the point of use. “Measurement technology is indispensable both for hydrogenation at the source and for dehydrogenation at the destination: it helps monitor and control the chemical reactions,” says Jens Hundrieser, Endress+Hauser’s European industry manager for mining, minerals & metals. “Furthermore, process photometers using inline colorimetry enable quality control and purity monitoring of LOHCs.”


3. Coke oven gas makes blast furnaces transformation-ready
Hydrogen has a large part to play in the future of steel production. The idea is to use the gas in new production processes like direct reduction that will supplant the classic carbon-based blast furnace route. But blast furnaces have long investment cycles and direct reduction requires green hydrogen in very large amounts. So bridge technologies are needed on the road to carbon-neutral steel. “One possibility is to inject coke oven gas into the blast furnaces,” says Jens Hundrieser. Coke oven gas contains 55 percent hydrogen; this replaces coal as a reducing agent and energy carrier for the process. The benefit here is an immediate way for manufacturers to lower emissions while also laying the groundwork to operate their blast furnaces with green hydrogen in future. In Germany, Dillinger and Saarstahl have been using this new technology since 2020; the injection systems come from plant builder Paul Wurth. Longstanding, partnership-based customer relationships have led both companies to equip their plants with Endress+Hauser measurement technology, including 200 Cerabar pressure sensors.
Published 30.01.2024, last updated 12.02.2024.
Dive into the world of the process industry through new exciting stories every month with our «changes» newsletter!
Subscribe to newsletter