Ahead of their time
Although gas-fired power plants are considered a bridge technology in the energy transition, they still have to be efficient, flexible and cost-effective. The plants operated by German regional energy provider KMW achieve this with innovative ideas, intelligent systems and advanced technology.
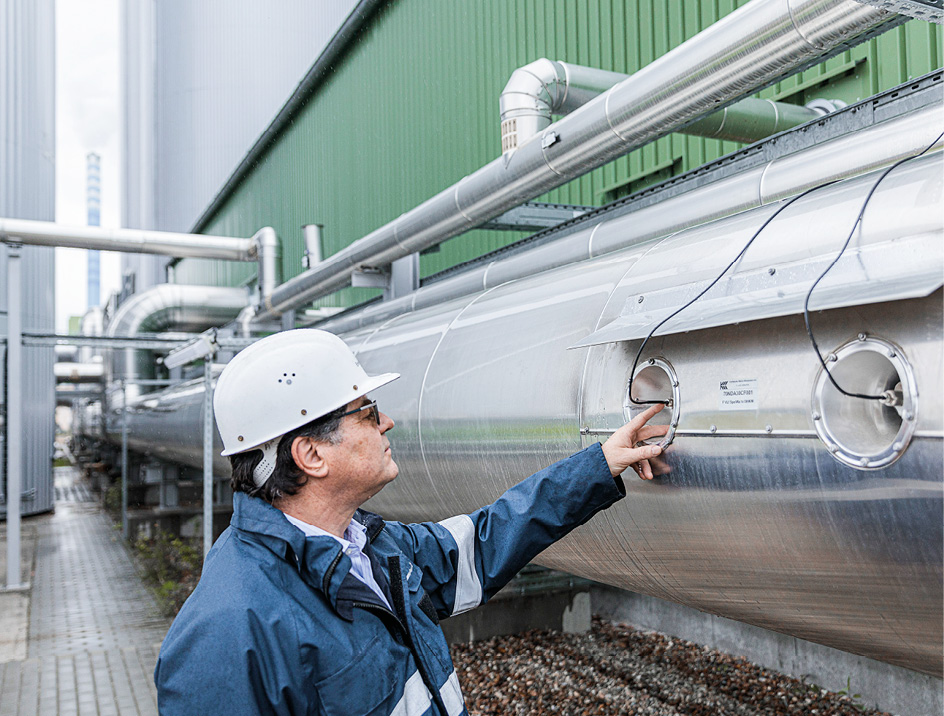
The only reminder of the coal era at the Kraftwerke Mainz-Wiesbaden AG (KMW) facility is a wooden sculpture of Saint Barbara. The patron saint of coal miners stands in the control center of the German regional energy provider, watching over the machinery’s performance and the employees’ fates and fortunes. “The statuette is a remnant from the demolition of our three coal-fired plants,” says Thomas Zimmerer, who works on electrical and control technology in KMW’s engineering business area. Since switching to gas in the year 2000, the company has relied on highly efficient plants and flexibility to hold its own in an electricity market made increasingly volatile by renewable energy sources.
Patented hot standby method
Starting right at the fuel changeover, the focus was on cost-effectiveness and sustainability. At a single stroke, the then newly built 400-megawatt gas turbine combined cycle power plant (GTCC) reduced CO2 emissions by 1.4 million tonnes per year and even today remains one of the most efficient in the world. Net efficiency is 58.4 percent, which can be increased to 80 percent by decoupling the process steam and district heating. In addition, steam from the company’s adjacent waste incineration plant is used to generate electricity and keep the machinery warm. “That means the cogeneration plant can be ramped up within a half hour, even after two days of downtime,” reports Thomas Zimmer.
All of that notwithstanding, several years ago KMW was facing new challenges and once again instigated a power plant plan. For one thing, German gas power plants are putting in fewer operating hours because of the increase in renewable energy resources and declining commodity exchange prices for electricity. Second is rising demand for district heating in the region. “The issue is that the GTCC plant can only be operated in a reasonably economic manner when its operating hours track the electricity market, rather than district heating needs,” explains Thomas Zimmerer.
Quickly ramping up to full power
The solution was a €115 million cogeneration power plant (CPP), brought on line in 2021. Ten identical gas engines with electrical and thermal output totaling 100 and 90 megawatts respectively can be started up and shut down in 150 seconds. The engines make very efficient use of the natural gas energy – over 85 percent. “When there is less sun or wind, meaning that electricity prices are good, the CPP starts up quickly. The heat is decoupled and, in situations of low demand, temporarily held in three new heat storage units with a total capacity of 12,000 cubic meters,” says Thomas Zimmerer. Together they can buffer up to 750 megawatts of thermal power for later release.
The plant includes technology from Finnish general contractor Wärtsilä Energy Solutions – and know-how from Endress+Hauser, the main instrumentation supplier. More than 300 instruments monitor the processes for water used in cooling and heating, and the auxiliary systems. In addition, KMW directly commissioned Endress+Hauser to supply instrumentation for the heat storage systems: more than 120 temperature sensors record their heat profile; feed water is analyzed as well. At the input end of the CPP, Coriolis flowmeters measure the precise volume of incoming gas. Many of the measurement points are designed along the ‘two out of three’ principle: three sensors measure independently of each other so that should one malfunction, two values remain available.
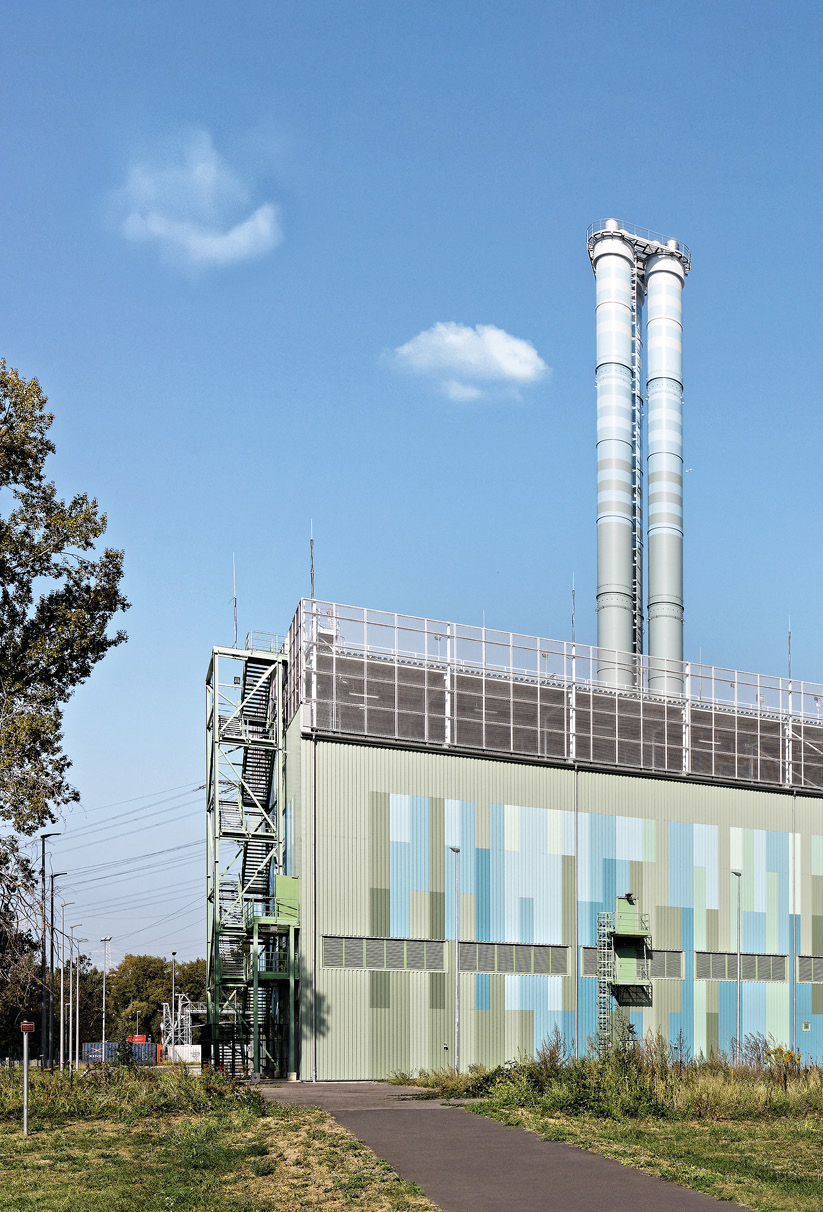
The new cogeneration plant can start up or shut down in just 150 seconds.
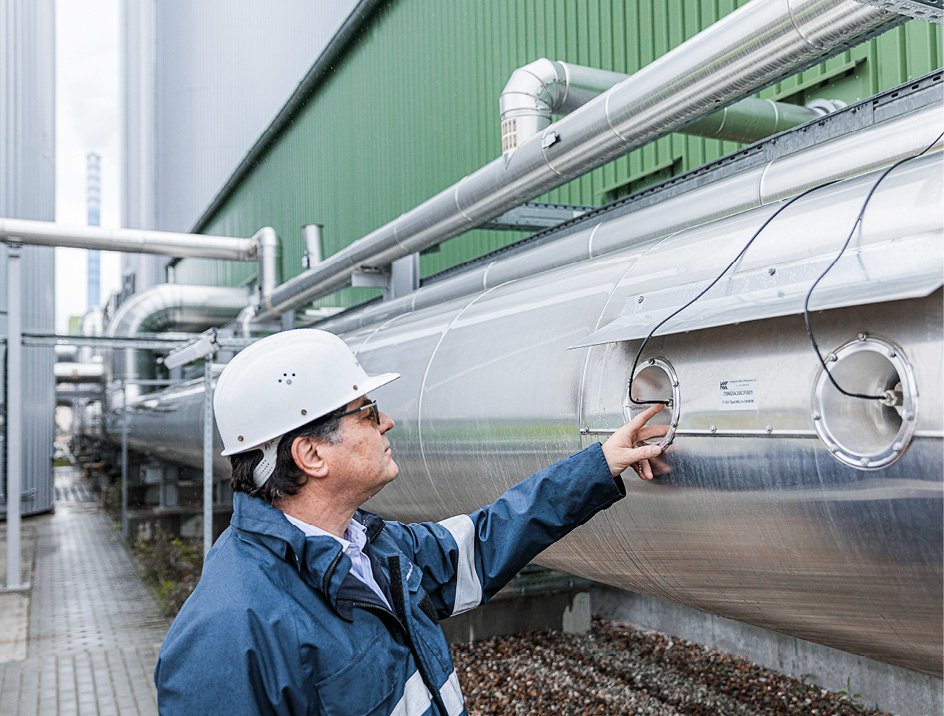
Clamp-on ultrasound sensors are deployed all around the plant.
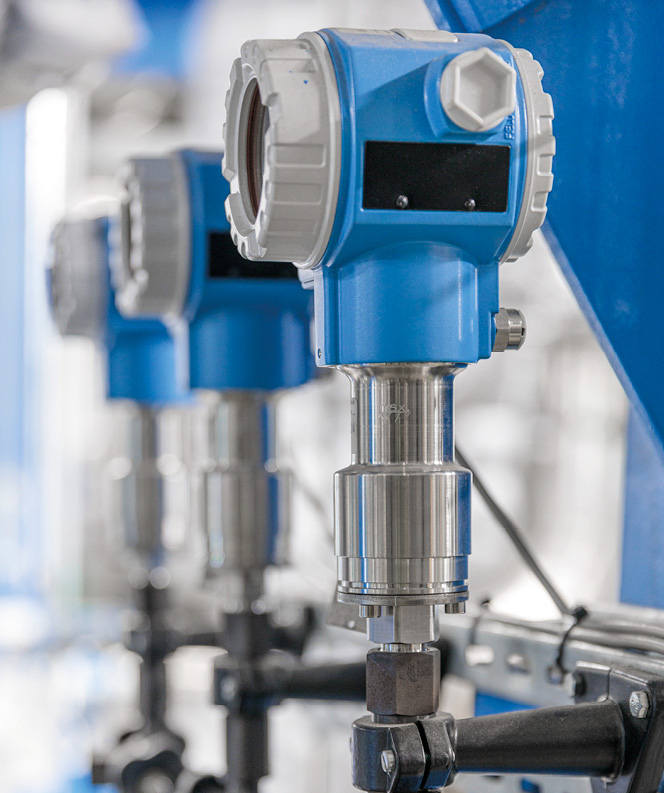
Endress+Hauser Cerabar S pressure transmitters monitor plant functioning.
Non-contact measurements
It’s no coincidence that Endress+Hauser was awarded the contract. “We always rely on our experience with the measurement technology in question when making our buying decisions,” says Thomas Zimmerer. Among the things he values are the clamp-on ultrasonic sensors. “We’re highly satisfied with these products’ safety, measurement stability and precision.” Other plus factors for Zimmerer are the simple operation of all instruments, as well as Endress+Hauser’s capability to offer the complete installation, including pipework and commissioning. The people aspect is a good fit, too: “We enjoy working together with KMW,” says Endress+Hauser employee Horst Theobald, who handles field support for the company. “And that’s also because we can sense a lot of innovative spirit here!”
Published 15.07.2022, last updated 14.09.2022.
Dive into the world of the process industry through new exciting stories every month with our «changes» newsletter!
Subscribe to newsletter