Using it all
Wernsing turns potatoes into french fries and hash browns – as well as into heat and electricity. Precisely tailored solutions ensure that every process is optimized.
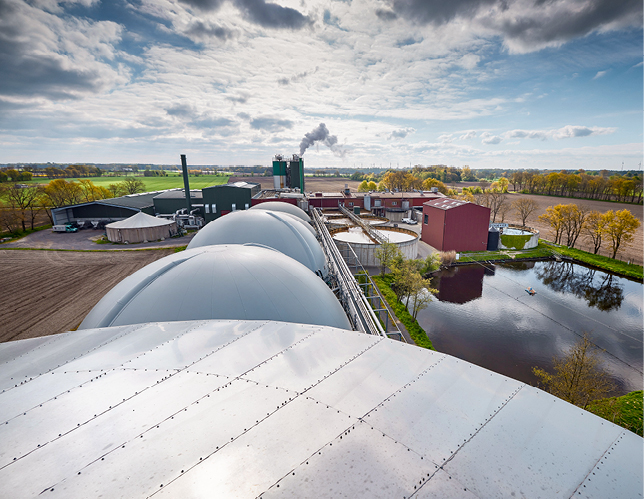
Sustainability? Extracting the most out of what’s available? Circularity? Those concepts aren’t new for the Wernsing Food Family. The group of companies processes around half a million tonnes of potatoes every year into french fries, croquettes, hash browns and other specialties at 15 locations around Europe. The plant at Wernsing’s headquarters in the north German village of Addrup has been utilizing every last bit of potato for the past 20 years. The site leverages the potential of wastewater and production waste to cover a substantial portion of its electricity needs for the energy-intensive manufacturing processes.
The core element is generation of biogas. Wernsing channels remnants from potato and food product manufacturing into six fermenters, where fresh material is added twice an hour. The gas given off, with an average methane content of 62 percent, is dried and purified. Then it is used to run five combined heat and power (CHP) units that generate up to four megawatts of electricity. At a temperature of 450 degrees Celsius, the exhaust gas from the CHP units helps to dry the dewatered sludge produced during fermentation. What remains is a natural fertilizer, which the company sells.
6fermenters
turn potato remnants into biogas for electricity generation at the Wernsing plant in Addrup.
PRECISE MEASUREMENT WITH BIOGAS EXPERTISE
Process instrumentation is at the heart of the wastewater treatment and biogas system. In its search for robust and durable instruments, Wernsing turned to Endress+Hauser as a full-range supplier. The right measuring technology also helps to master the various applications’ specific challenges, resulting in flawless system operation around the clock. For wastewater, the partners came up with a solution that manages air supply to the aeration basins in sync with the biodegradation process, thereby optimizing energy use. When it comes to biogas, another solution ensures that the sensors in the fermenters are cleaned regularly. Along the pipes and ducts leading to the CHP units, 19 Prosonic Flow B 200 ultrasonic flowmeters measure the quantity of gas precisely, even under fluctuating conditions. The unique measurement technology also directly detects methane levels in the biogas, so fermentation anomalies are identified and corrected without delay.
Projects like these have nurtured a partner-like relationship between Wernsing and Endress+Hauser. And the company’s path to greater efficiency continues: There are firm plans in place to process the treated wastewater using ultrafiltration and reverse osmosis for subsequent use in technical equipment. There will also be a biomass heating system to generate steam for the production processes. Taking the 2018 figure for carbon emissions as a baseline, the company’s climate strategy calls for a 40 percent reduction by 2025, with the amount of electricity produced from biogas also slated to increase by 40 percent to over 20 gigawatt-hours a year.
Published 31.01.2024, last updated 12.02.2024.
Dive into the world of the process industry through new exciting stories every month with our «changes» newsletter!
Subscribe to newsletter