Putting experience into practice
Thanks to the ingenuity of Raoul Merklen, flanges can be repaired in next to no time.
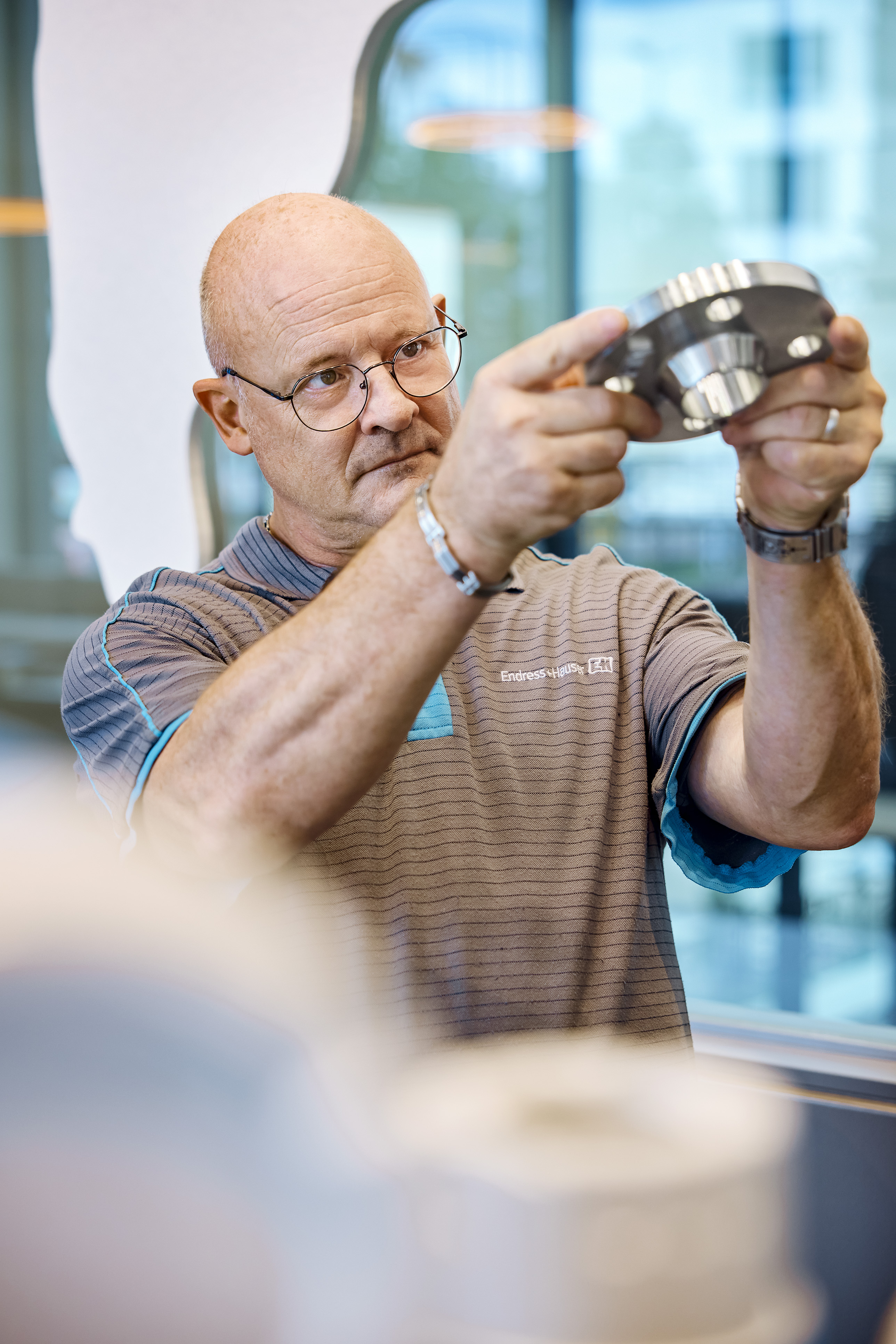
Flanges are what connect instruments to the process. Damage to the flange contact surface can weaken the seal. Even minor impairments can mean a flange replacement, which involves removing the electronics, separating the flange, grinding down the welding seam and recalibrating the instrument. All that might take a good six hours. If a special flange needs ordering, then it can take days. Unless you have someone like Raoul Merklen on your team. A mechanic at Endress+Hauser Flow, he can repair a flange in 15 minutes. His secret? Rather than separate the connection from the instrument, he basically performs ‘open heart surgery’. He simply machines away small indentations with a fine grinding tool (or welds over them in cases of heavier damage). Although this destroys the surface cross hatching, rendering the flange temporarily unusable, Raoul Merklen developed a tool that allows him to accurately retrace the fine grooves on the contact surface back to the radius. Thanks to this special tool, which resembles a compass, the flange ends up looking like new. “In Cernay, I was able to rescue six titanium instruments costing 25,000 euros each using this method,” says the technician, who hails from the Alsace region of France. “Without the repair work, the customer would have had to wait eight months.”
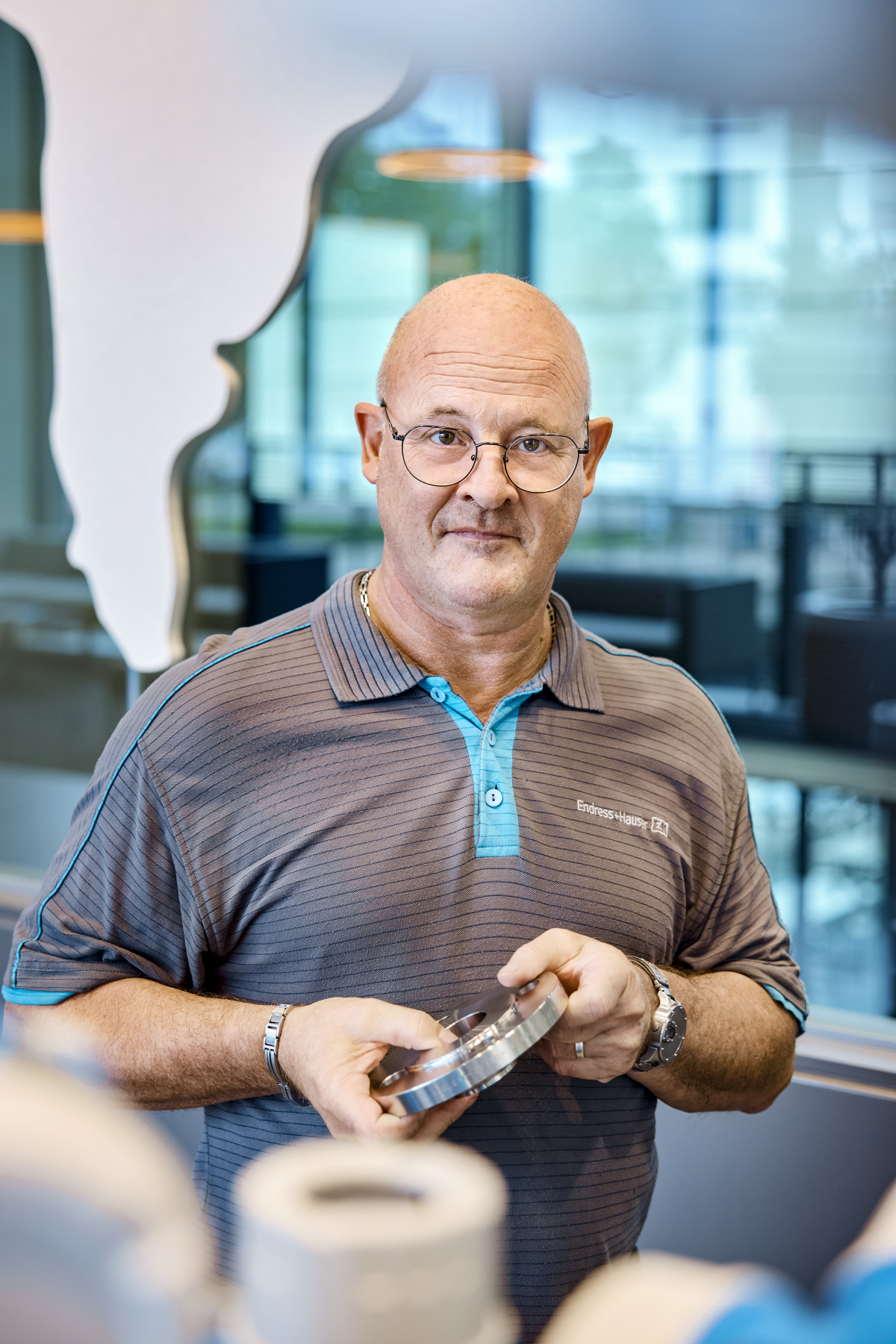
Extensive experience
Raoul Merklen has been with Endress+Hauser Flow for 30 years, working as a logistics specialist, fitter, mechanic and welder. His experience is worth its weight in gold. Today he is a machining expert and operates the new machining robot that puts the finishing touches on flowmeters. While the machine itself makes no mistakes, by the time the instrument is manufactured, calibrated, packed and installed at the customer site, it’s been through a lot of hands. One careless moment or a single impact, and the damage is done. Damaged flanges regularly land on his workbench, whether from production or the customer. In emergency situations, he sometimes heads out with his special tool to provide on-site assistance. “If I can save an instrument, then I’ve had a good day,” he says, adding that “No matter where the damage was caused, we stand for superior quality. Every customer is entitled to a flawless instrument.” Thanks to his innovation, which he implemented with the help of Rainer Lorenz and Gebhard Gschwend from tool making, he has already gotten a lot of customers out of tight spots – and deservedly won the 2021 Process Innovation Award.
Published 06.12.2022, last updated 12.12.2022.
Dive into the world of the process industry through new exciting stories every month with our «changes» newsletter!
Subscribe to newsletter