Measuring what counts
To save energy, you first need to know how much is being consumed. Which is exactly what the EngyCal RH33 BTU meter has been measuring for years. Given the rising cost of energy and stricter emissions requirements, this evergreen instrument is gaining even stronger appeal.
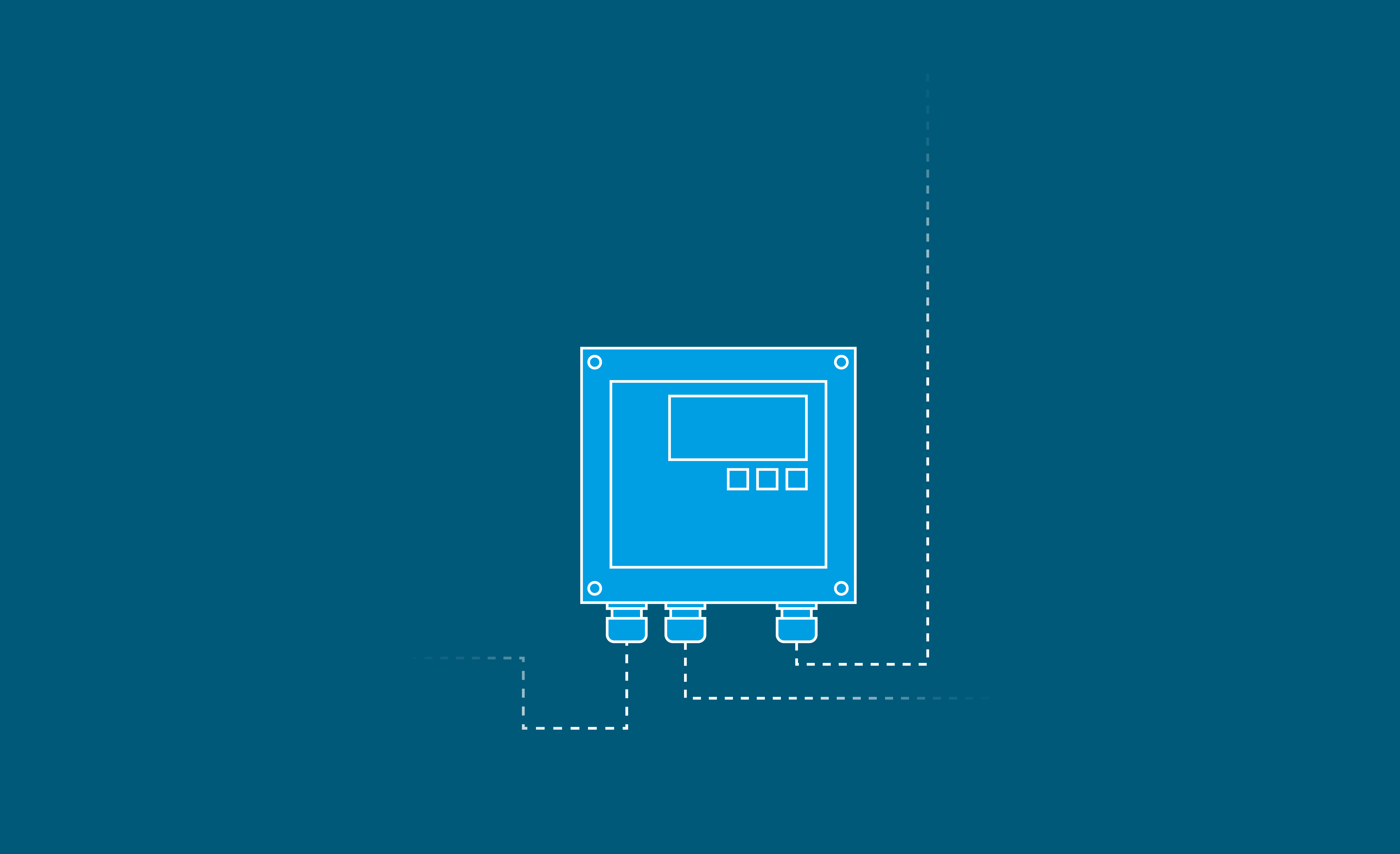
Heating and cooling are musts for industrial production. Processes taking place in vessels, tanks and piping systems often need to run at specific temperatures, and then there are buildings to be heated or cooled. A full 60 percent of industrial electricity consumption is used for heating and cooling, a statistic that illustrates the vast potential for optimization. It also shows the importance of every kilowatt saved when energy is scarce and costly and there are climate goals to be reached. Joachim Hajek sees the most savings potential in thermal energy. “Countless thermal processes exist for generating hot water and steam,” says the global product manager for system components at Endress+Hauser. There has to be clear data on those processes. For years Endress+Hauser has offered a proven product for that precise purpose: the EngyCal RH33 BTU meter.
This custody transfer instrument operates using two resistance temperature sensors and a flowmeter. Their temperature and flow measurements feed into the EngyCal, which calculates an energy consumption figure for later billing, much like the electricity meter in your home. “The instruments alone don’t save energy, but they do show where there are savings to be had. Which is precisely what customers have their sights on: they need a basis for devising energy-saving measures,” says Hajek. Customers are able to draw further inferences from the mix of energy consumption, peak load and time of use relative to the size of the plant. Energy providers can then use this information to generate invoices, while energy managers can monitor usage across entire industrial complexes. “By installing our solution at various points around a process system, you get a precise overview of where the energy is going.”
Published 16.02.2024, last updated 11.03.2024.
Dive into the world of the process industry through new exciting stories every month with our «changes» newsletter!
Subscribe to newsletter