Less is more
Procurement offers great leverage towards achieving climate neutrality. That’s because with high production volumes – of instrument housings, for example – even small material savings can make a difference.
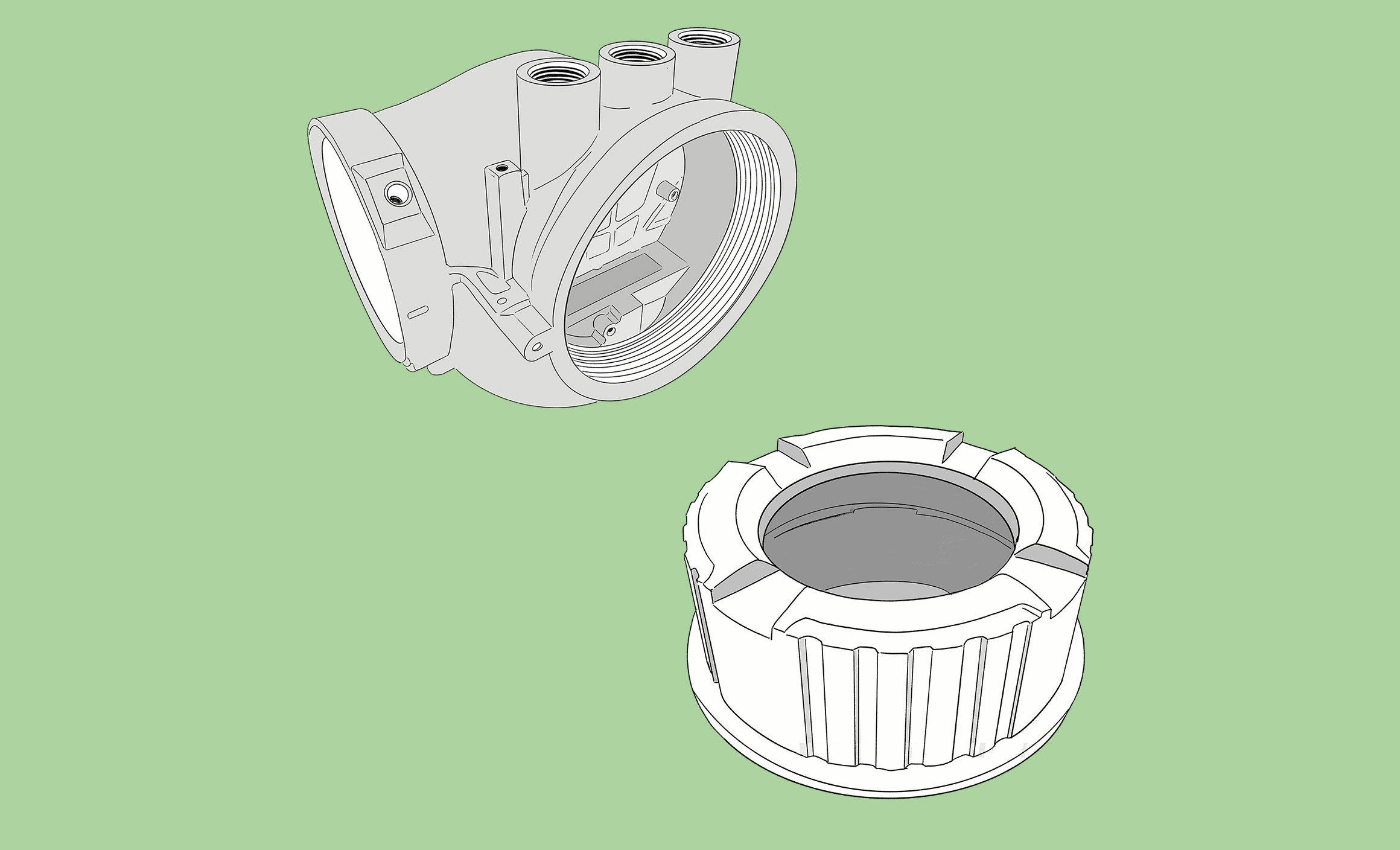
Endress+Hauser groups several flowmeter product families under its Proline instrument concept. One variant of Proline 300 alone ships in quantities of around 50,000 units per year, all with identical housings. This is where strategic buyer Roger Tschudin sees huge potential for saving material through design. “We already had experience from redesigning another housing cover, a relatively simple affair. But this housing presented a considerably greater challenge because the instrument inside is used in explosion protection areas with their own special requirements.”
Carbon footprint analysis of flowmeters shows that their mechanical components account for around 85 percent of the total because they contain a lot of steel and aluminum. “In principle, the steel sensor components offer most scope for saving material and thus emissions, but it would be very difficult to make changes here,” says Fabian Dreier, head of supply chain management at Endress+Hauser Flow. “The pipes are under pressure and there are norms and standards to be met.” It is more practical to adapt the housing and cover of the transmitters. While these account for around 30 percent of the carbon footprint, they still cannot be redesigned instantly.
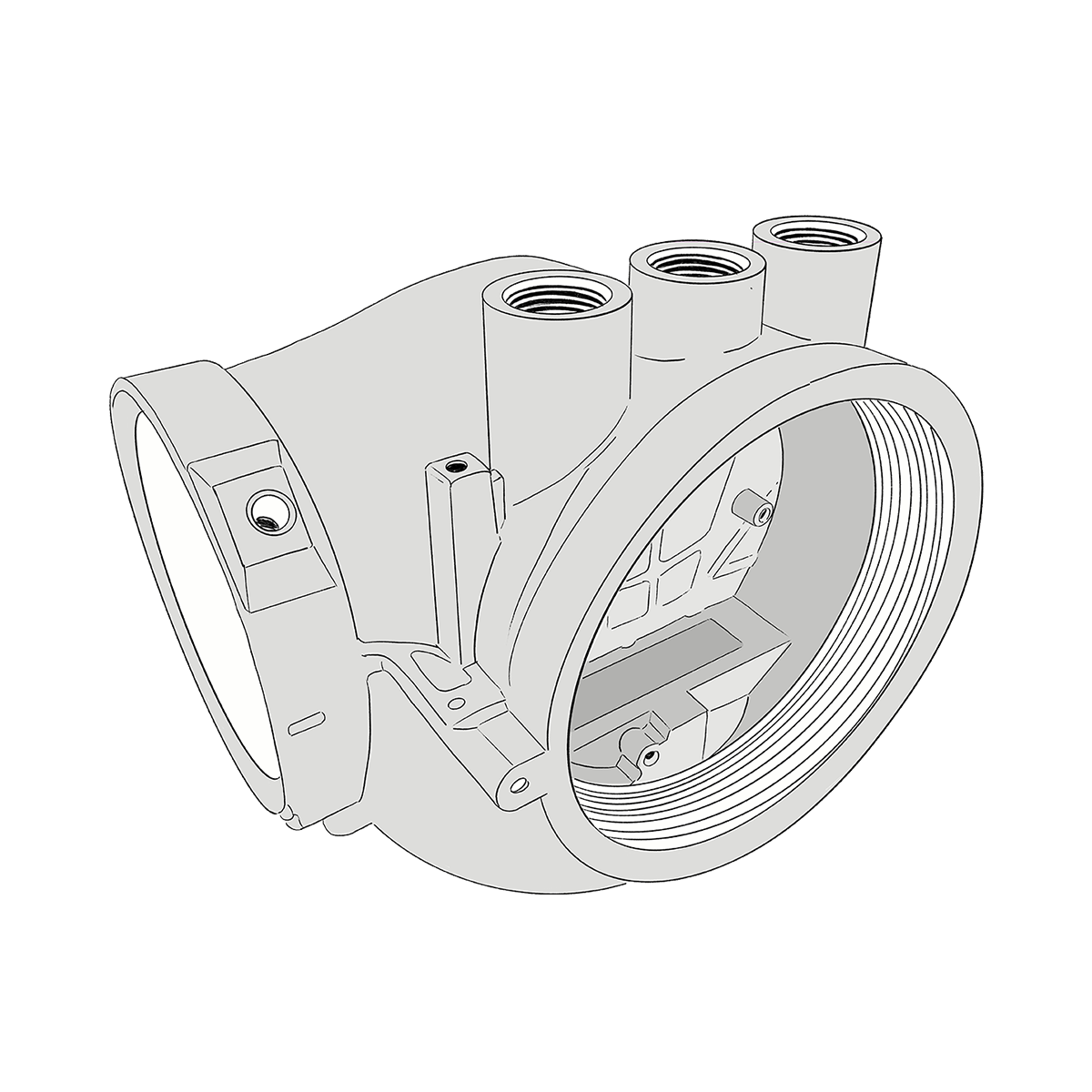
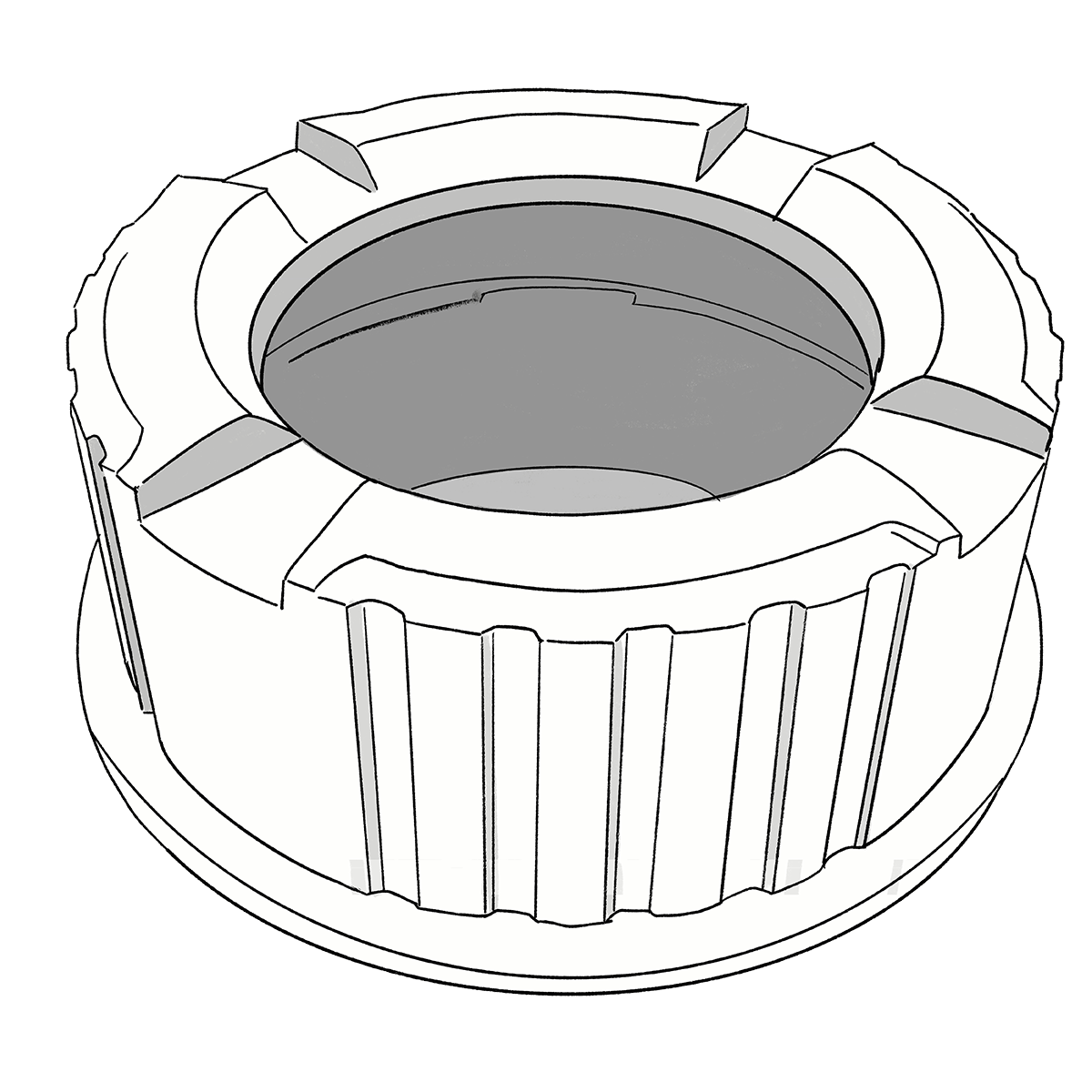
It took three years of close cooperation between engineering and suppliers before Fabian Dreier was able to announce the results: reducing wall thickness from 9 to 7 millimeters makes the housing and the cover 12 and 19 percent lighter, respectively. This saves more than 15 tonnes of aluminum per year, or the equivalent of 160 tonnes of CO2. Reinforcements at other points compensate for the reduced wall thickness. The challenge was that the assembly inside could not change too much, because the electronics remain the same and need sufficient space.
“We developed the eco-design for the new housing using numerical simulations. This saved us a lot of time and testing,” says Andre Brygadin, an expert in casting processes at Endress+Hauser Flow. “The external certification and the pressure test for explosion protection took the most time.” There were also adaptations to the manufacturing process, as he again explains: “High-pressure aluminum casting is faster and more precise than low-pressure casting. Parts emerge from the mold close to their final quality and barely need any finishing.” The housings are supplied complete with powder coating, which removes a step from Endress+Hauser’s supply chain and makes customers’ supply chains correspondingly shorter. The new housings are currently being introduced.
Published 12.02.2025, last updated 17.02.2025.
Dive into the world of the process industry through new exciting stories every month with our «changes» newsletter!
Subscribe to newsletter