Hot stuff
Utilities are essential to the operation of industrial plants. The problem is that lots of process energy vanishes unused. To do something about that, you need to make the right adjustments – using the right measuring technology.
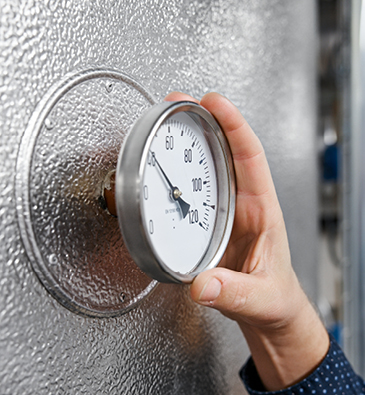
OPTIMIZATION
When Oliver Seifert talks about utilities, he likes to use the acronym WAGES, which stands for water, air, gas, electricity and steam. He thinks it’s a fitting term. “Utilities are like service providers,” says Seifert, a vortex flowmeter and steam management expert at Endress+Hauser. “They keep a plant’s core processes running.” Taking a closer look at them is worthwhile for any business looking to improve sustainability. “Since utilities are among the biggest consumers of energy in the industrial sector, the potential for decarbonization is huge – but often still overlooked,” Seifert adds.
The most effective lever is process heat, usually generated from gas, coal or oil. In Europe, that heat accounts for two-thirds of total industrial energy consumption, with a quarter of this estimated to be process steam. To reduce their emissions, plant operators can switch steam generation to non-fossil technologies such as electric boilers or industrial heat pumps, which reclaim waste heat. But that often requires significant investment, and the technical feasibility needs to be proven first. “In existing plants, it’s usually just easier to increase energy efficiency,” Seifert says. Installing precise, state-of-theart measuring technology in crucial places helps cut costs and enhances safety.
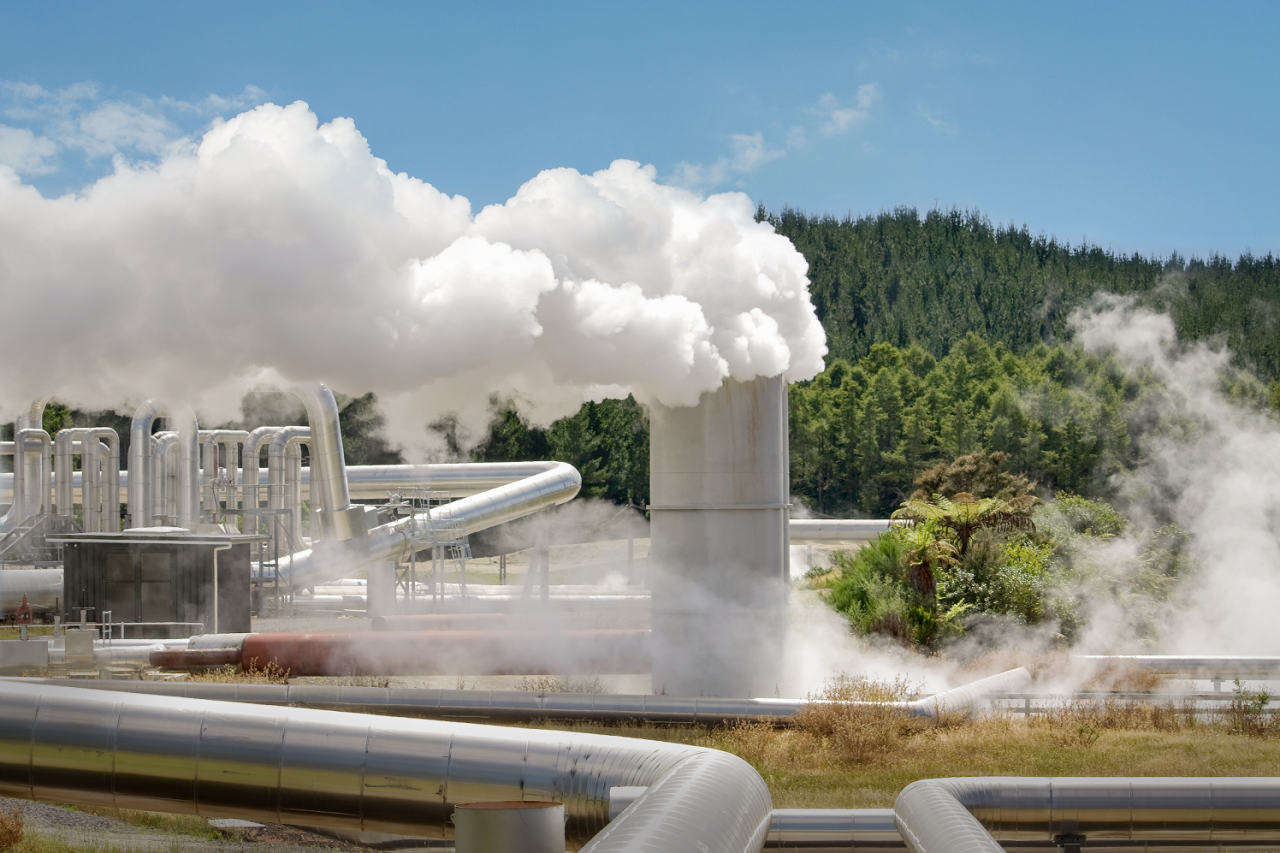
Systematic savings: steam generation, distribution and utilization can be readily optimized in existing plants.
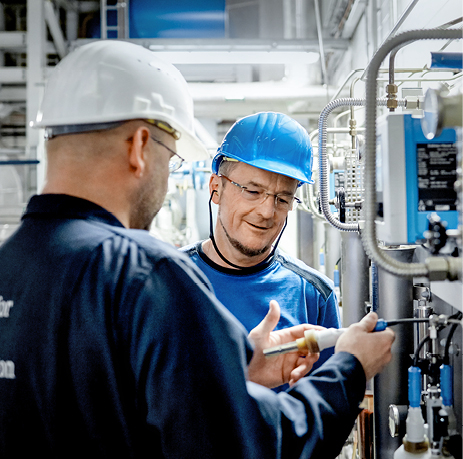
40%
of the fossil energy consumed by the process industry goes to generating steam in boilers.
ELIMINATING WET STEAM
A pivotal factor here is steam quality. “One hundred percent dry, saturated steam provides optimum efficiency,” Seifert explains. But that steam can condense on the way from the boiler house to consumers due to poorly lagged pipes, faulty steam traps or pressure and temperature fluctuations. That causes wet steam to form. Its moisture results in energy losses and, in many cases, dangerous water hammer. “Endress+Hauser Prowirl 200 is the world’s first vortex flowmeter that precisely measures steam quality in pipes and alerts you if wet steam is detected,” Seifert says. That allows operators to take fast action if necessary.
The quality of feed water also matters. “If it’s not right, you’ll get corrosion or deposits in the boiler, which will impair efficiency and reduce its life span,” Seifert explains. Many plant operators still take manual samples for lab analysis of specific parameters. But they only do so every few days. Endress+Hauser has developed a compact, plug-and-play analysis system especially for industrial steam generators. It continuously takes samples, cools them and measures their pH, conductivity and dissolved oxygen. “With its sophisticated design, our solution does the job with only a fraction of the sample quantity that conventional systems require,” Seifert says. That brings a corresponding reduction in energy and cooling water consumption.
Plant operators can further improve efficiency by replacing all of a boiler’s standard measuring technology with modern instruments. “Now we are able to monitor the boiler’s specific energy consumption and efficiency, then use those insights to minimize fuel consumption,” Seifert adds. Much hinges on the precise measurement of flow, pressure and temperature, which is another area where instruments such as the Prowirl 200 vortex flowmeter come into their own. While the presence of wet steam can cause measurement errors of typically five percent or more in other devices, the Prowirl 200 continues to deliver high-precision data. Users can leverage the solution’s full potential by collecting, evaluating and duly analyzing that data, Seifert says. “Thorough energy monitoring can reduce energy consumption in steam processes by up to 15 percent.”
Published 04.03.2024, last updated 11.03.2024.
Dive into the world of the process industry through new exciting stories every month with our «changes» newsletter!
Subscribe to newsletter