Every millimeter matters
How much oil is in the storage tank? In international trade, only calibrated measuring devices can deliver an acceptable answer. Calibration can be done laboriously on site or directly at the factory, as Endress+Hauser does. And this is all thanks to a unique calibration rig.
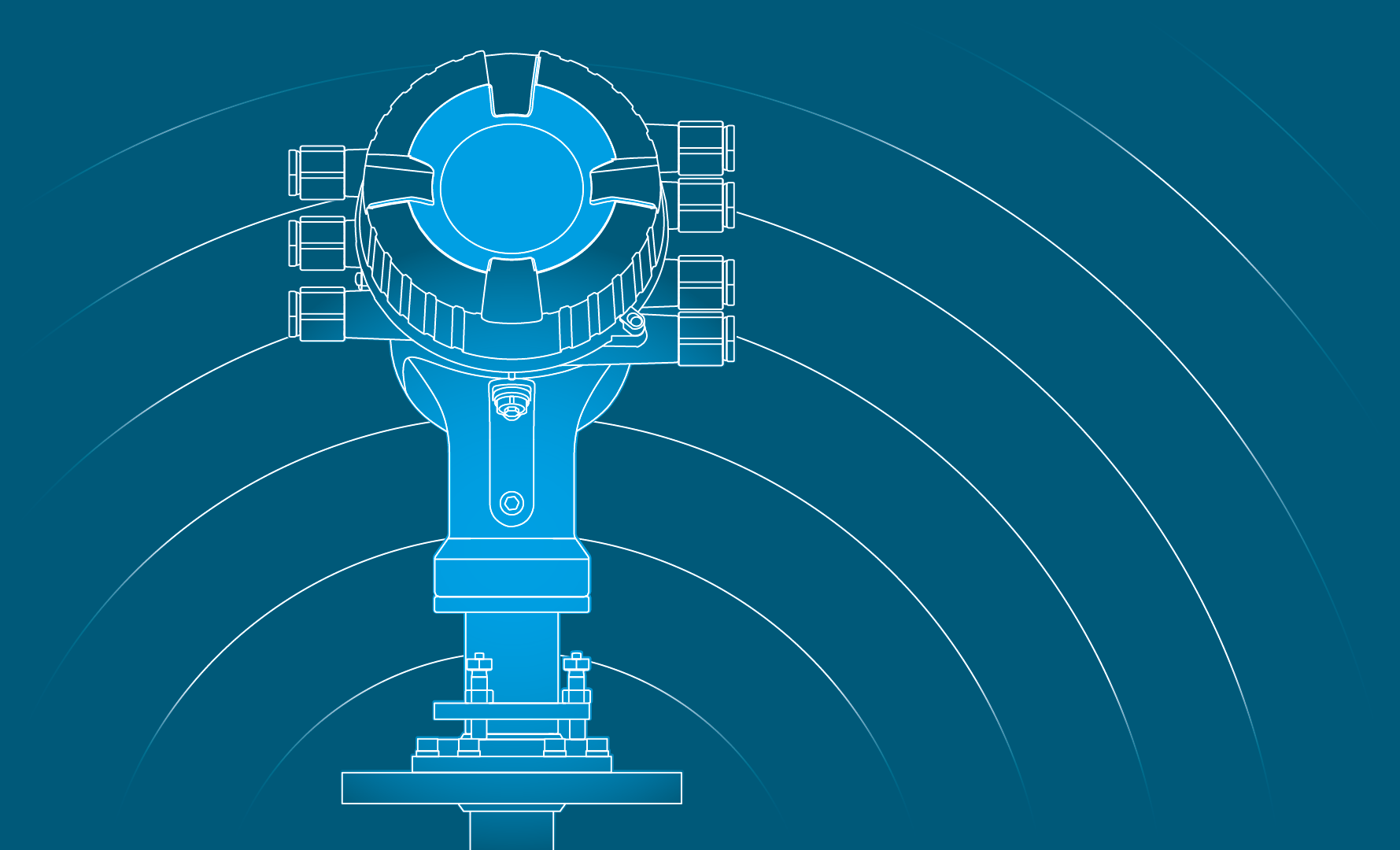
Oil and gas surpass all other commodities in terms of the volume that gets moved around. Every day, some 90 million barrels (14.4 million tonnes) of crude oil and natural gas are extracted, filled, stored temporarily and transported onward around the world. “In large storage tanks, every incorrectly measured millimeter of fill level could make a difference of several thousand euros straightaway,” Daniel Hoy from Endress+Hauser Level+Pressure explains. That is why measuring devices on large oil tanks must be calibrated verifiably according to internationally recognized standards such as OIML R85 or API 3.1B.
There are two options for verifiable calibration: In the first and most frequent one, a verification officer stands on the tank and measures the fill level with a measuring tape. The results are compared to those from the level sensor installed on the tank. The maximum permissible discrepancy is four millimeters. Obtaining various benchmarks involves emptying or filling tanks – expensive procedures that often take several days. Customers can save all this time and effort by choosing the second option, factory calibration. This requires a complex calibration rig, like the one Endress+Hauser has developed at the competence center for level and pressure measurement in Maulburg. “We precisely calibrate every radar sensor ordered for tank gauging on the rig. With multiple measuring positions along its 50-meter length, that takes at most an hour and a half,” says Daniel Hoy. The calibration rig stands in an elaborate purpose-built room and is the only one worldwide able to calibrate radar level sensors for tanks and stilling wells to an NMI-certified standard. The devices are allowed to be out by no more than one millimeter, as stipulated by the generally accepted OIML R85 recommendation.
Endress+Hauser built the rig in response to industry developments: In the USA and in Europe especially, space at ports is becoming scarcer and so their storage tanks are being built taller. Gas tanks 50 meters high are not unusual. The diagram shows a simplified birds-eye view of how factory calibration of the radar sensors works.
50m
is the maximum calibration distance. Thus the rig covers many tank sizes.
0.5mm
within the measurement range of up to 50 meters is the maximum measurement discrepancy of the device under test after calibration.
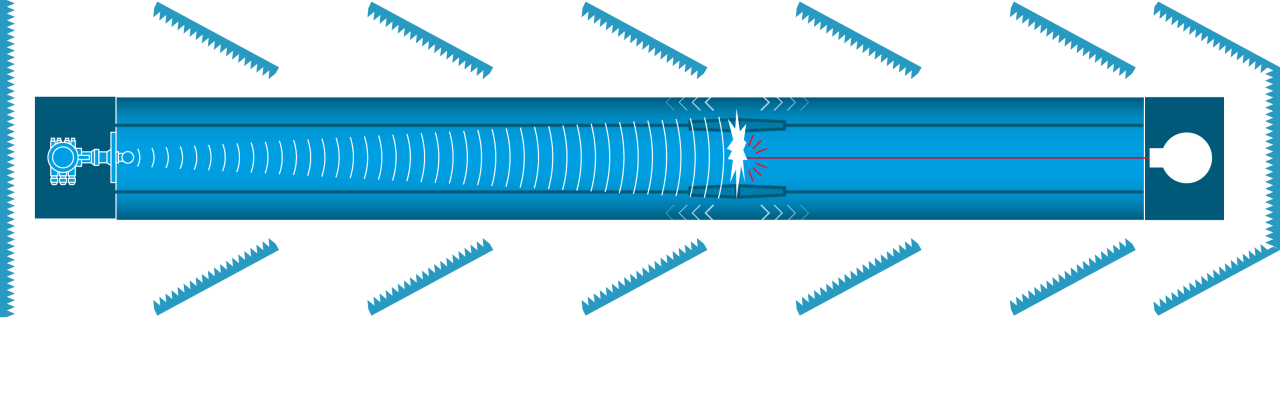
Published 04.03.2025, last updated 09.03.2025.
Dive into the world of the process industry through new exciting stories every month with our «changes» newsletter!
Subscribe to newsletter