An electrifying market
Electromobility is an indispensable building block of the energy transition. So it’s no surprise that the lithium-ion battery market is booming. But with this come myriad challenges all along the value chain.
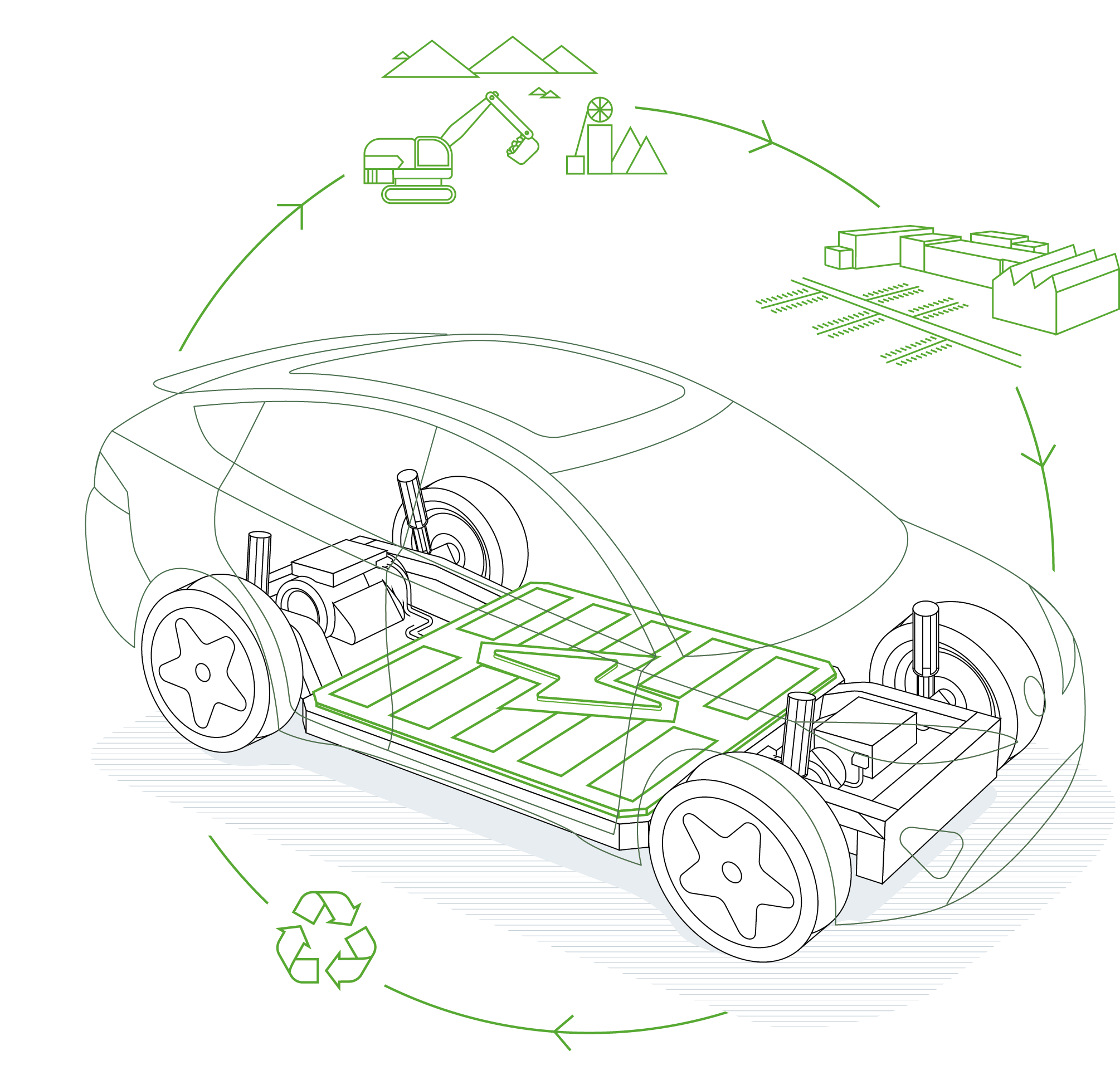
With electromobility booming across Europe, Asia and America, it’s not just battery manufacturers and automobile companies looking to seize an opportunity. Companies including BASF, Umicore and Johnson Matthey are also striving for market share while investing billions in battery manufacturing. Analysts predict that electromobility could be one of the biggest growth drivers for the chemical industry in the coming years.
As this change plays out, global markets are also on the move. Government subsidies, Asian investors and fast-growing startups are right now laying the foundation for activities that could help Europe establish itself as the world’s number two manufacturing region for batteries in less than 10 years. Nevertheless, old and new players alike face major challenges. Compliance with environmental, social and corporate governance standards is a key factor for industry to pave the way for tomorrow’s mobility.
150
million e-vehicles are expected globally by 2030.
EFFICIENT RAW MATERIALS EXTRACTION
Lithium compounds are at present extracted from high-yield brine lakes or a seldom-occurring pyroxene mineral called spodumene (lithium aluminum inosilicate), primarily in South America, Australia and China. Sufficient quantities of this key battery element can still be found today: estimated lithium resources stand at around 40 million tonnes, which equates to more than 210 million tonnes of lithium carbonate equivalent. Experts nevertheless anticipate a shortage no later than 2025, considering the complexity and high cost of extracting this raw material. With brine lake groundwater, for example, the lithium-rich brine has to be pumped into evaporation basins, concentrated and then cleaned. The evaporation process increases the lithium concentration from 2,000 ppm or so to as much as 6 percent in the end brine. It’s then processed further at chemical plants into lithium carbonate with 99.9 percent purity. “Advanced process solutions for flow, level, pressure and temperature measurement help at every step to efficiently extract battery-grade raw material,” says Andrew Reese, Global Mining, Minerals & Metals Industry Manager at Endress+Hauser.
QUALITY IN THE RIGHT MIXTURE
Raw material purity and composition are critical in battery manufacturing. The main requirement for the cathode and anode material is to be as free from water as possible. With the other constituents the requirements vary, because different lithium compounds impart different characteristics to the end product. In the tradeoff between power density, energy density, safety and service life, as well as availability and costs, there are compounds with strengths in certain departments but weaknesses elsewhere. This is why the industry utilizes so-called NMC mixed oxides – blends of nickel, manganese and cobalt oxides – which count among the top materials used to store electricity in lithium-ion batteries for e-bikes and e-vehicles.
Raw material purity and composition are critical in battery manufacturing. The main requirement for the cathode and anode material is to be as free from water as possible. With the other constituents the requirements vary, because different lithium compounds impart different characteristics to the end product. In the tradeoff between power density, energy density, safety and service life, as well as availability and costs, there are compounds with strengths in certain departments but weaknesses elsewhere. This is why the industry utilizes so-called NMC mixed oxides – blends of nickel, manganese and cobalt oxides – which count among the top materials used to store electricity in lithium-ion batteries for e-bikes and e-vehicles.
For a battery to have particular properties, the NMC composition must be precisely known. Then there is the fact that the materials pass through numerous process steps on their journey from extraction to end product. Every transfer requires checks on the state of the material. “It takes advanced analysis instruments to satisfactorily resolve these challenges,” says Philipp Conen, Global Industry Manager for Chemicals at Endress+Hauser. Raman analyzers supply all of the real-time, inline measurements needed to guarantee the properties and quality of lithium-ion batteries.
CLOSING THE LOOP
The accelerating proliferation of e-vehicles will also rapidly grow the stockpile of exhausted batteries. So companies will increasingly turn to recycling as a way of recovering raw materials from battery cells
to address growing demand, conserve resources and make e-mobility more sustainable.
There are currently two primary recycling methods. One is cryogenic cleavage, which involves cooling the aged cells to minus 196 degrees Celsius with liquid nitrogen and then crushing them. Following that, a reaction with sodium hydroxide releases hydrogen that is burned off in a controlled manner. Plastics, metals and lithium salts can then be separated out for further processing. Hydrometallurgical methods employ wet chemical processes to separate out the metals. “Endress+Hauser instruments ensure safe battery recycling processes and help make them sustainable. Our analysis measurement technology is also at work here treating the wastewater,” says Philipp Conen.
Published 18.07.2022, last updated 14.09.2022.
Dive into the world of the process industry through new exciting stories every month with our «changes» newsletter!
Subscribe to newsletter