A clean operation
Within just two years, chemical company Chemours built a new plant for climate-friendly refrigerants in Texas – from initial planning to commissioning. Close collaboration ensured the project ran quickly and smoothly.
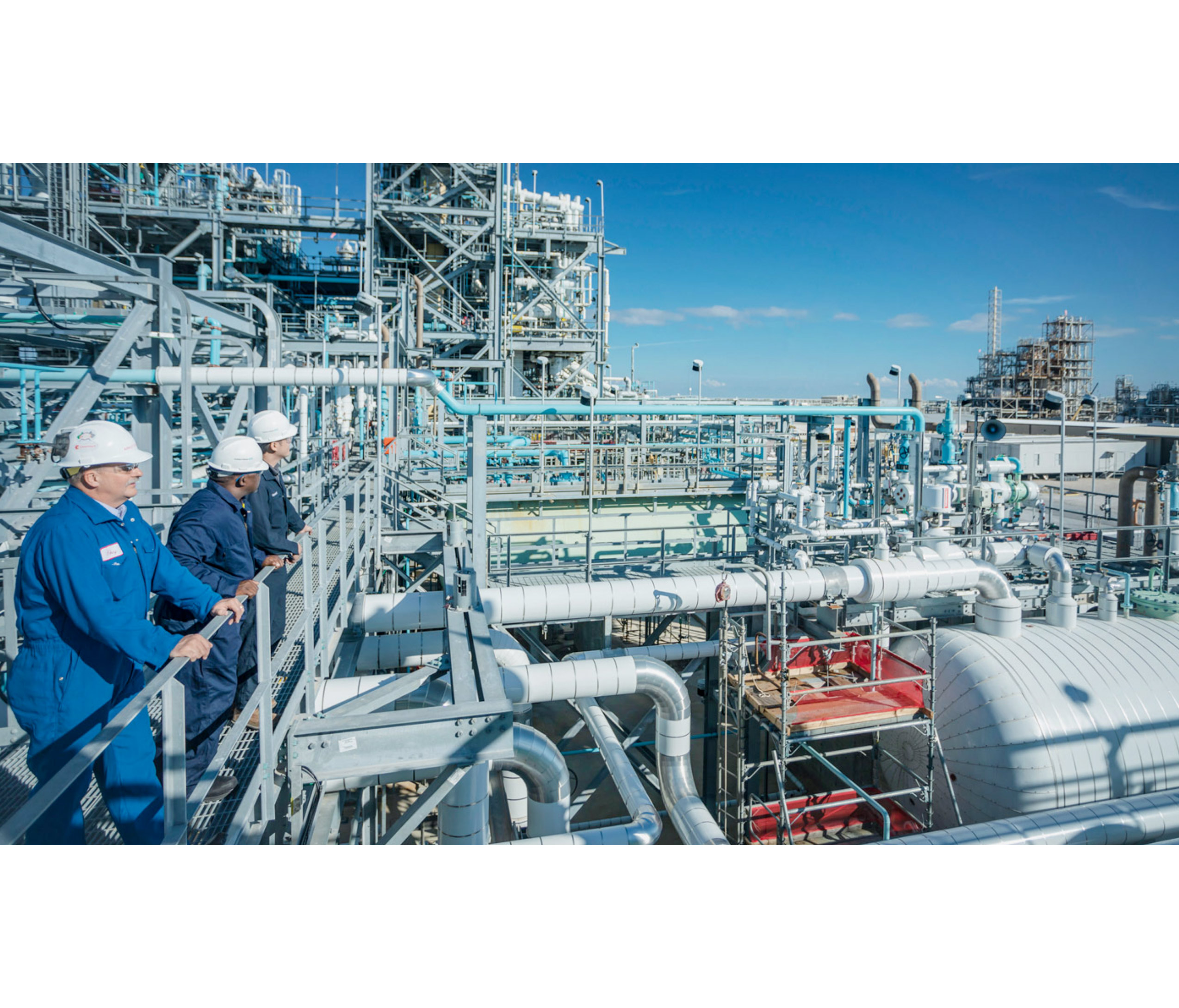
The roads to Ingleside are bounded on either side by cotton fields as far as the eye can see. It can be oppressively hot in southern Texas. Between May and September, average temperatures soar above 30 degrees Celsius (86 degrees Fahrenheit). And then the humid air from the Gulf of Mexico sweeps in. It may just be a coincidence that chemical company Chemours produces refrigerants in this region, just a stone’s throw from the port city Corpus Christi, but anyone who travels around in a car here will certainly value the comfort of an air conditioning system.
But refrigerants used widely for many years needed to be improved relative to their environmental footprint. A new refrigerant marketed by Chemours under the trade name Opteon boasts significantly lower global warming and ozone depletion potential than legacy refrigerants. With the new plant in Ingleside, the company tripled its production capacity in one fell swoop, putting it in a position to address the growing demand from manufacturers around the world who are striving to make vehicle, residential and commercial air conditioning systems more eco-friendly.

Willis Haviland Carrier (1876–1950) is considered the inventor of modern air conditioning systems
Market pressure
Opteon is a key product for Chemours, one that serves as a main pillar of the company’s sustainability strategy. “We knew that if we produced HFO-1234yf, we would sell it,” explains Robert K Endres while sitting in his office on the grounds of the plant. The electrical engineer was one of the first members of the project team, responsible for power distribution, process control, safety systems and process instrumentation. But hardly anyone knows him under this name. Instead, everyone calls him by his first-name initials, which is why his business card is adorned with Arkey.
Chemours invested 300 million US dollars in the new production facility. Rapid construction of the plant was a top priority. There was little more than two years between the decision to build the plant and its commissioning. “In our world, that’s really fast,” emphasizes Arkey Endres. As with every project, his job was to keep an eye on time, quality and costs. “However, our main focus in this project was clearly on the timeline and the quality issues.”
Arkey Endres incorporated process engineering requirements into the early stages of the project. As if it wasn’t enough to build a world-scale plant within an unusually short period of time, Chemours is producing the compound in Ingleside for the first time using a modified process. The chemical reactions are complex, and the process contains moving parts, all of which places high demands on the materials and technologies. The company had also made a long-term investment. As Arkey Endres puts it, “The plant is supposed to run for 50 years, not just five.” For that reason, Chemours opted for the higher-performance technology, the higher-quality material. “But we wanted added value for our money.”
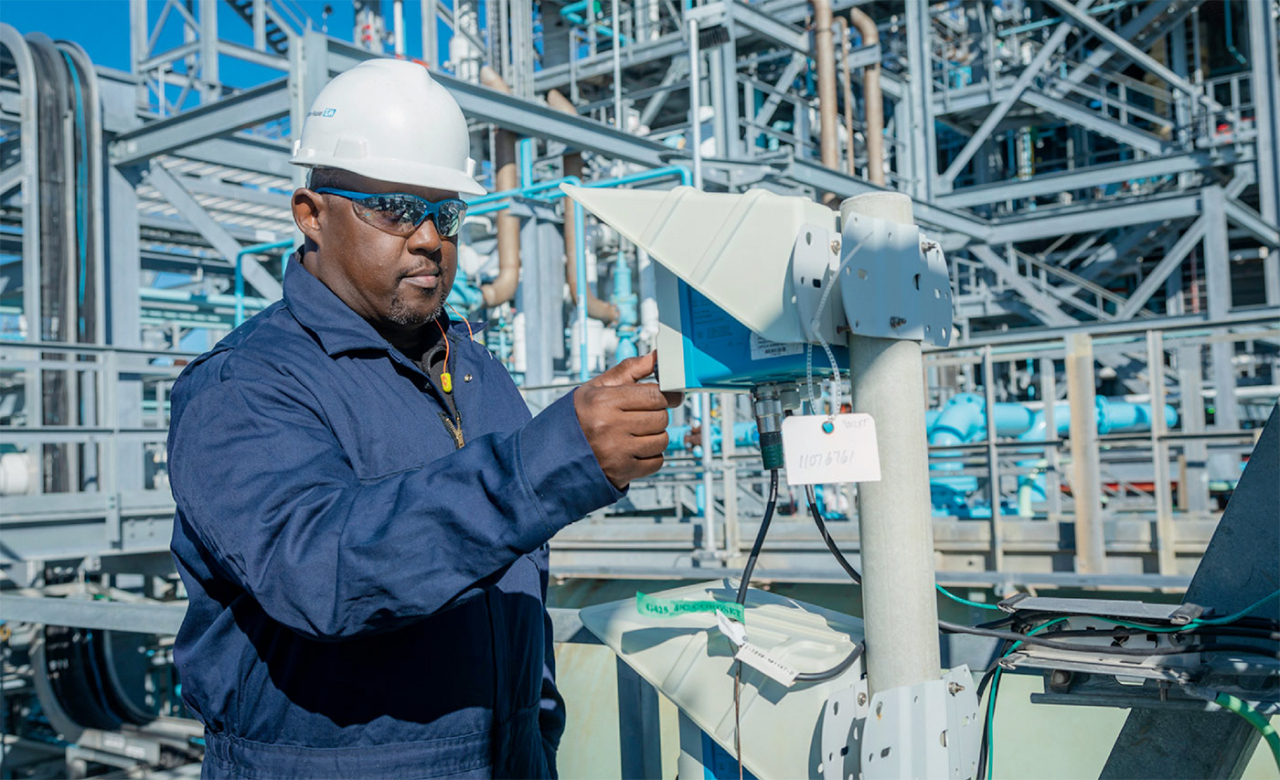
Ready at the push of a button: Patrick White led the Endress+Hauser project team.
Close support
The added value that was offered was a critical factor in the decision to award the instrumentation contract to Endress+Hauser. “We suggested embedding one of our engineers at an early stage,” explains Patrick White, who led Endress+Hauser’s project acquisition and execution team. As Strategic Account Manager, for years he was the point of contact for DuPont, and then later for Chemours. He currently serves as the Group’s Head of Strategic Account Management for the Chemical Industry.
Embedded engineers have long been common practice in many sections of a new production plant – “but not when measurement technology is involved,” as Patrick White points out. “That’s why we need our customers’ trust.” But a long and solid working relationship helps, which was the case with Chemours. “Endress+Hauser has been on our supplier list for more than 10 years,” says Arkey Endres. “That’s quite an achievement, because it never just happens by itself. Our suppliers have to work for that time and again.”
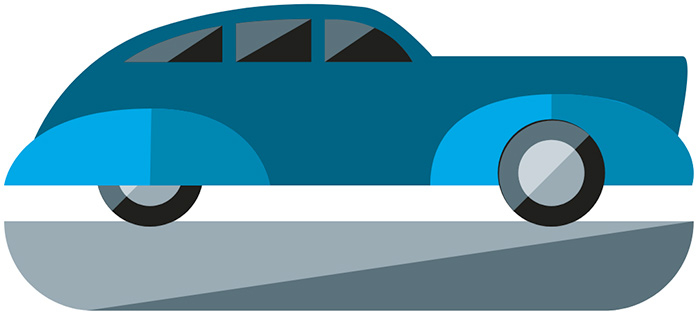
In 1938, US manufacturer Nash introduced the world’s first automotive air conditioning to the market
High-tech and know-how
The new Chemours Opteon production facility contains more than 2,000 Endress+Hauser devices. Apart from instruments for measuring flow, level, pressure and temperature, Endress+Hauser also supplied the liquid analysis technology, which had been mainly provided by a competitor in the past. “Since we’re talking about critical measurements here, Chemours was persuaded by our digital Memosens technology,” says Howard Siew, Chemical Industry Manager, Endress+Hauser USA.
Endress+Hauser has gained experience with embedded engineers through a wide range of large-scale projects. “Embedded engineers bring their instrumentation skills and knowledge into the important planning phases and they maintain contact with the core of the project team,” explains Howard Siew of the concept. In the case of the new Opteon plant, the Endress+Hauser engineer worked at an engineering, procurement and construction company on the US East Coast. He identified the right measurement technology for each task, provided recommendations based on experience with similar applications and configured the instruments accordingly.
“Without the support of Endress+Hauser, operation of the new plant would have been delayed.”
Arkey Endres
Manufacturing Technology Fellow at Chemours
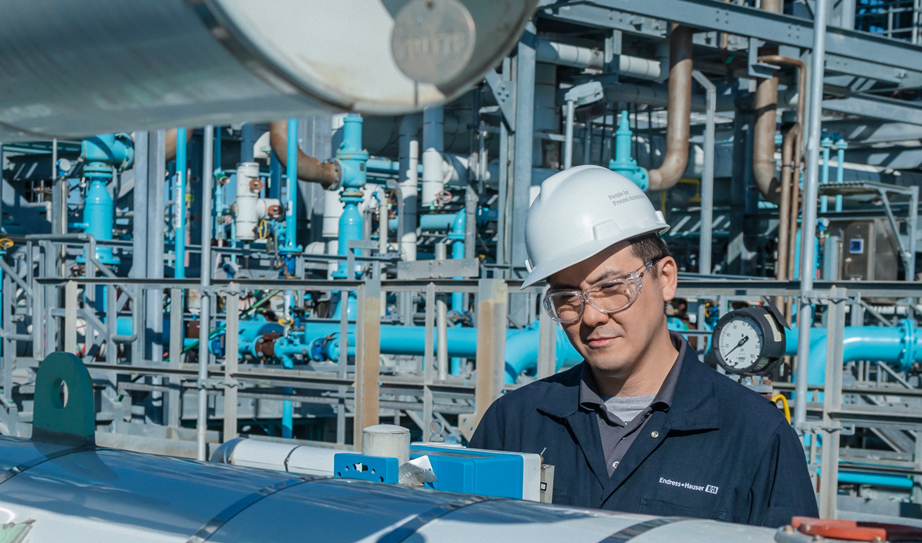
Technology and expertise: Howard Siew knows the needs of the chemical industry.
Smooth teamwork
Apart from the expertise, Arkey Endres was also impressed by Endress+Hauser’s presence. “Right at the beginning, I said: I know you have other customers. But in this project, you have to act as if you only have us.” Project managers oversaw every phase and coordinated the work of all parties involved on the East Coast and in the Gulf Coast region, including the representatives Vector Controls and Automation Group and Eastern Controls. “The customer,” says Patrick White, “didn’t realize that so many people and teams were involved.”
“The excellent and close collaboration took a lot of pressure off us,” emphasizes Arkey Endres. “And that during a time in which other things demanded our attention.” Because a supplier unexpectedly dropped out, the production of a primary product was integrated into the plant at short notice. “All at once, the project volume increased by 20 percent,” says the Chemours engineer. Endress+Hauser also provided the instrumentation and support.
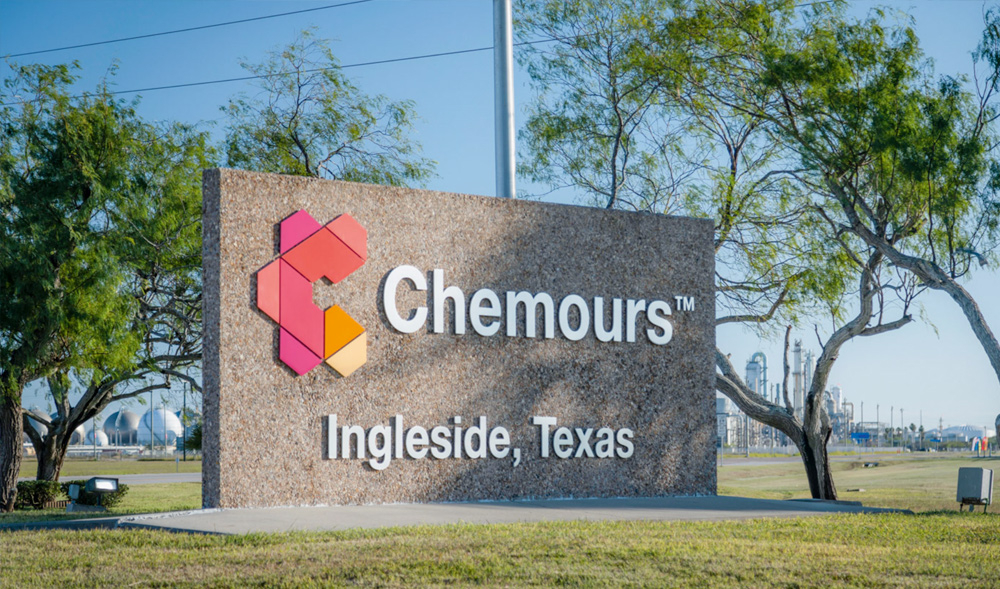
Established site: Chemours has been manufacturing in Ingleside, Texas, since 1971.
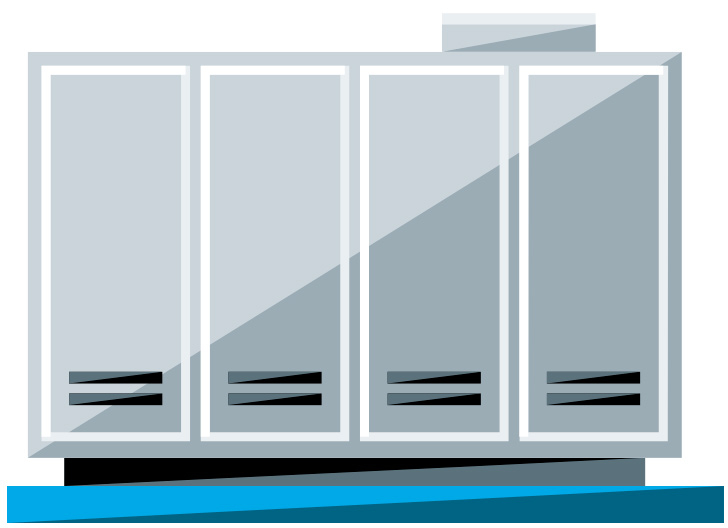
Today, there are 3.6 billion cooling devices and systems in operation around the world, a number expected to rise to 14 billion by 2050
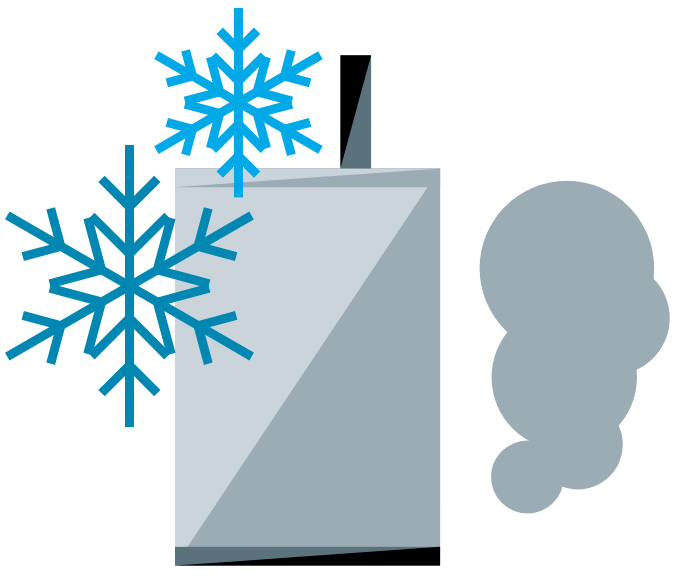
The global warming potential (GWP) of typical legacy hydrofluorocarbons refrigerants is 1,500 to 4,000 times higher than that of CO2
Valuable support
The overall package included the inspection of all instruments at Endress+Hauser’s facilities in Greenwood, Indiana. Every single device was checked to ensure that it met specifications, functioned correctly and was properly configured. “This step saved us an enormous amount of time during commissioning,” says Arkey Endres with conviction. Service technicians helped with the commissioning of the instruments and the system integration. In addition, Chemours’ plant personnel were trained by Endress+Hauser in a Process Training Unit (PTU) located in Houston, which offered the same communication protocol installed at Ingleside.
Arkey Endres is sure of one thing: “Without the comprehensive support of Endress+Hauser – the embedded engineer, the inspection of the instruments, the training program – operation of the new plant would probably have been delayed. All of this support was extremely valuable to us. Even if I can’t put the benefits into numbers – if I had to do another project like this, my recommendation would be: get an embedded engineer to work with us!”
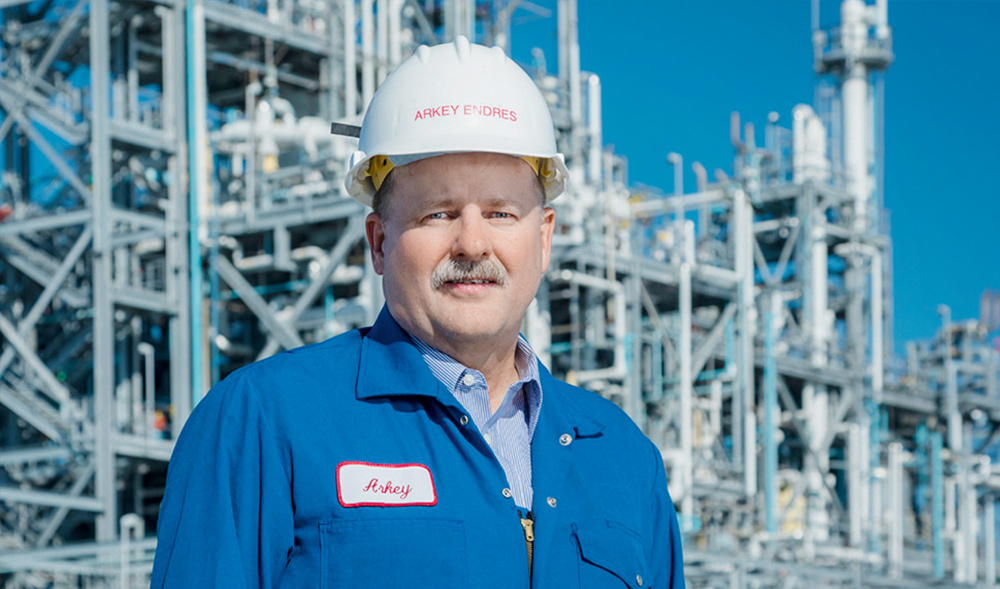
Mission accomplished: Arkey Endres and his team completed the project on time.
Published 01.05.2020, last updated 20.06.2022.
Dive into the world of the process industry through new exciting stories every month with our «changes» newsletter!
Subscribe to newsletter