Auf Schatzsuche
Daten spielen in der digitalen Transformation der verfahrenstechnischen Industrie eine entscheidende Rolle. Doch noch immer finden sie nur selten den Weg aus Geräten, Maschinen und Anlagen hinaus. Jetzt ebnen ihnen intelligente Feldinstrumente, digitale Schnittstellen und cloudbasierte Analysewerkzeuge den Weg. Die Chancen sind gewaltig – vor allem, wenn sich physische Sensorwelt und Künstliche Intelligenz miteinander verbinden.
Wer in diesen Tagen die großen Industriemessen durchstreift, wähnt sich bisweilen in einer anderen Welt. Selbst Aussteller, die unlängst noch tonnenweise Stahl auf ihren Messeständen stehen hatten, treten plötzlich auf wie Tech-Unternehmen. Die Aufmerksamkeit gilt ganz den Angeboten zur Digitalisierung der Produktion. Die schöne, neue Welt der Industrie 4.0: Hier ist sie schon real. Wer allerdings anderntags eine x-beliebige verfahrenstechnische Anlage besucht, ganz gleich, wo auf der Welt sie steht und was sie herstellt, wird wahrscheinlich wenig von einer vierten industriellen Revolution zu sehen bekommen. Noch immer dominiert analoge Signalübertragung die Prozessindustrie; selbst modernste Messgeräte nutzen meist nur die 4…20 mA-Stromschleife, um das Leitsystem mit einem Messwert zu versorgen.
< 5%
der in der Produktion verfügbaren
Daten werden internationalen Studien
zufolge heute genutzt.
„ Die Digitalisierung verfahrenstechnischer Anlagen kommt mehr und mehr aus der Ecke der Pilot-Installationen heraus. Wir stehen an einem Wendepunkt.“
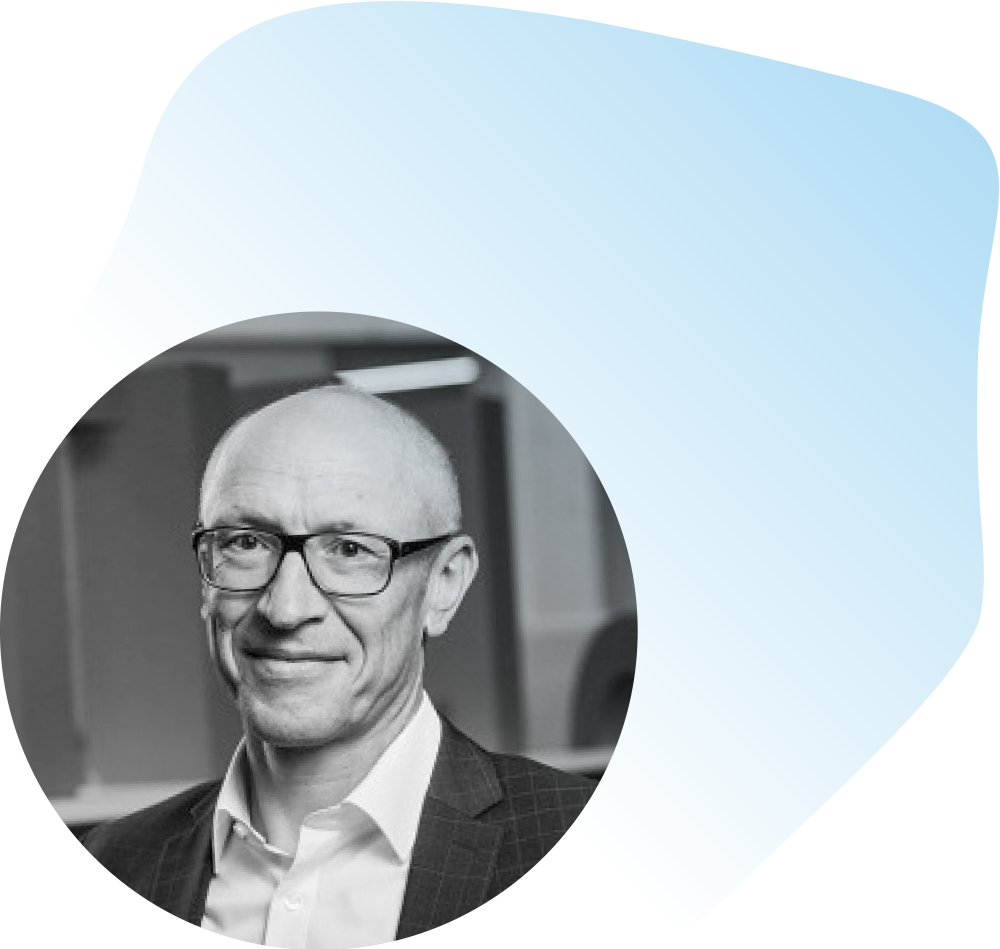
Rolf Birkhofer,
Geschäftsführer Endress+Hauser Digital Solutions
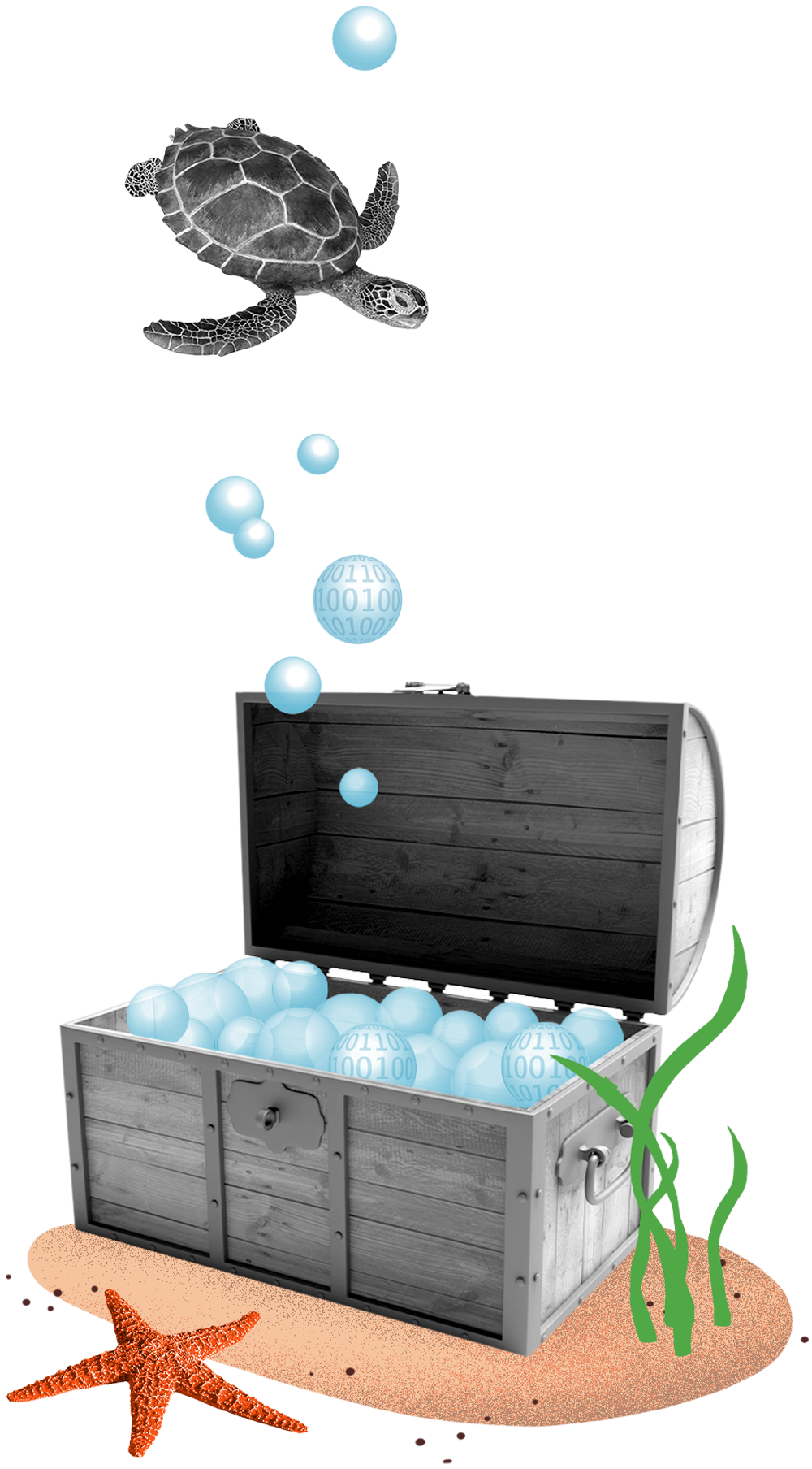
„Internationale Studien gehen davon aus, dass derzeit nur etwa fünf Prozent der in der Produktion verfügbaren Daten ausgewertet werden“, sagt Dr. Rolf Birkhofer, Geschäftsführer von Endress+Hauser Digital Solutions. „Diese Zahl deckt sich ziemlich genau mit unseren Erfahrungen. Obwohl Endress+Hauser Messgeräte seit vielen Jahren digital kommunizieren können, macht der überwiegende Teil unserer Kunden bislang keinen Gebrauch von dieser Option.“ Für diese Zögerlichkeit gibt es viele Gründe. Etwa die jahrzehntelangen Lebenszyklen von Prozessanlagen und Feldinstrumenten. Die Vielzahl an Ausrüstern, deren Geräte in einer Anlage verbaut sind. Oder auch die strengen Sicherheitsanforderungen und Regularien, denen viele Branchen unterliegen. Wer in einem solchen Umfeld Kunden vom Einsatz neuer Technologien überzeugen will, muss gewichtige Argumente in die Waagschale werfen.
BRANCHE AM WENDEPUNKT
Und doch ist in der Branche etwas in Bewegung geraten, berichtet Rolf Birkhofer. Neue Generationen intelligenter Messgeräte liefern eine Fülle an Daten über den eigentlichen Messwert hinaus, die Rückschlüsse auf Sensor und Prozess erlauben. Es gibt Technologien, die einen zweiten Kanal öffnen für eine schnelle und sichere Übertragung dieser Daten aus dem Feld bis hinauf auf die Unternehmensebene, ohne die Prozesssteuerung zu beeinflussen. Und viele Projekte haben bereits bewiesen, wie sich diese Daten in nützliche Informationen und wertvolles Wissen umwandeln lassen. „Die Digitalisierung verfahrenstechnischer Anlagen kommt mehr und mehr aus der Ecke der Pilot-Installationen und Klein-Projekte heraus. Wir stehen an einem Wendepunkt“, ist Rolf Birkhofer überzeugt. Den Anlagenbetreibern geht es um Effizienz, Sicherheit oder Qualität. Sie sind getrieben vom Wettbewerbsdruck und auch vom Fachkräftemangel. Entsprechend groß ist die Bandbreite der Anwendungen. Schon auf Ebene einzelner Messstellen kann das Auswerten von Daten maßgeblichen Nutzen schaffen. Doch den wahren Wert entfalten die Daten aus Gerät und Prozess erst, wenn sie zentral an einem Ort verfügbar sind – sei es für Cloud-Anwendungen oder Edge-Computing. Das Einsammeln und Verarbeiten der Daten wird dadurch skalierbar; es muss nicht mehr für jede Anwendung eine eigene Software geschrieben werden. Hinzu kommt die Möglichkeit, die Felddaten in Echtzeit mit weiteren Daten zu verknüpfen – zum Beispiel mit Wetterdaten oder Daten aus dem ERP-System.
VIRTUELLE UND PHYSISCHE WELT
Besonders spannend wird es, wenn unterschiedliche Datenquellen mittels Künstlicher Intelligenz verknüpft werden. „Big-Data-Anwendungen können in Sekundenbruchteilen hochkomplexe Erkenntnisse erlangen, wenn sie den richtigen Daten-Input erhalten“, erklärt Florian Falger, Market Manager im Innovation Lab von Endress+Hauser Level+Pressure. Das Team arbeitet unter anderem daran, mit speziellen Algorithmen und Künstlicher Intelligenz die Wartungsintervalle von Messgeräten, aber auch von ganzen Anlagenbereichen präzise zu bestimmen – eine Grundlage für das große Ziel vieler Unternehmen in der Prozessindustrie: vorausschauende Instandhaltung. „Die großen Anlagen etwa der chemischen Industrie laufen rund um die Uhr. Selbst geplante Wartungsarbeiten sind eine teure Sache“, weiß Florian Falger. „Predictive Maintenance würde helfen, notwendige Stillstände möglichst kurz zu halten, ungeplante Ausfälle zu vermeiden und Aufwände und Kosten zu senken.“
„Process Mining zeigt Optimierungsmöglichkeiten auf, weil wir anhand der digitalen Spuren tief in die einzelnen Prozessabläufe hineinschauen können.“
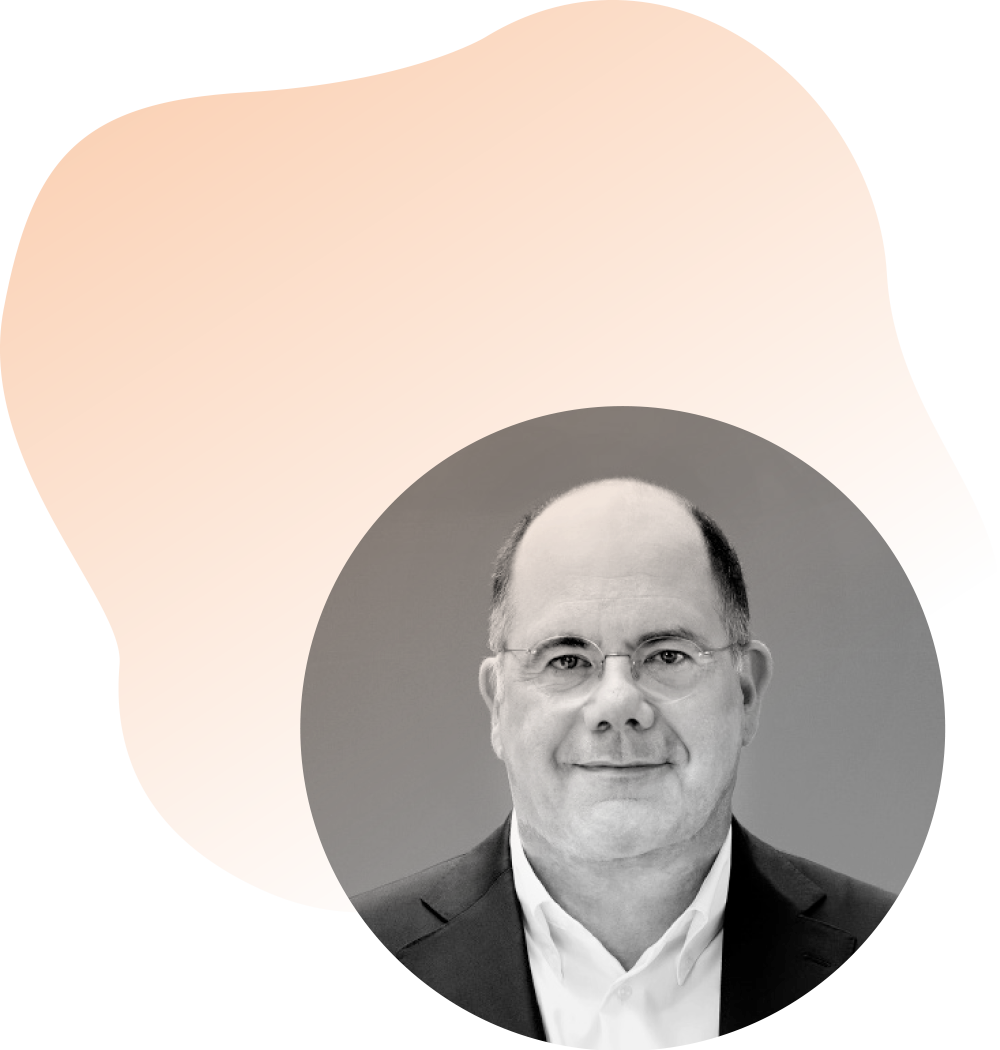
Stefan Sigg,
Vorstand der Software AG
Ein weiteres Anwendungsfeld liegt in der tiefen Analyse von Prozessdaten, um die Qualität der hergestellten Produkte zu verbessern oder den Prozess effizienter zu gestalten. „In der Fertigung hat der Einsatz von Process-Mining- Software noch viel ungenutztes Potenzial“, sagt Dr. Stefan Sigg. Er ist Vorstandsmitglied und Chief Product Officer der Software AG, eines der größten europäischen Softwarehäuser. Beim Process Mining werden Geschäfts- und Produktionsprozesse aus den Daten rekonstruiert und die verschiedenen Prozessinstanzen auf Ausreißer hin analysiert. Das führt immer wieder zu Aha-Erlebnissen – wenn zwar in den meisten Fällen die Prozesse genauso laufen, wie es vorgesehen ist, einzelne Prozessinstanzen jedoch einen ganz anderen Weg nehmen als gedacht. „Solche Prozessinstanzen verschwenden möglicherweise Geld, Zeit oder Energie“, führt Stefan Sigg aus. „Process Mining zeigt Optimierungsmöglichkeiten auf, weil wir anhand der digitalen Spuren tief in die einzelnen Prozessabläufe hineinschauen können.“
KNACKPUNKT INTEROPERABILITÄT
Damit sich Lösungen wie jene der Software AG umsetzen lassen, müssen freilich die Daten aus industriellen und kommerziellen Prozessen in auswertbarer Form vorliegen und leicht und sicher ausgetauscht werden können. Das ist das Ziel der Open Industry 4.0 Alliance. Fast 100 Anbieter von IT, Software, Fabrik- und Prozessautomatisierung haben sich mittlerweile in der Allianz zusammengefunden, um die Interoperabilität ihrer Geräte und Lösungen in Industrie-4.0-Anwendungen sicherzustellen. „Betreiber nutzen innerhalb einer Anlage, ja sogar für das gleiche Messprinzip, Feldgeräte unterschiedlicher Anbieter. Und sie erwarten, dass sich alle diese Geräte einfach anbinden und vernetzen lassen“, erklärt Hans-Jürgen Huber, der Endress+Hauser in der Open Industry 4.0 Alliance vertritt. Dort wird an einer Referenzarchitektur gearbeitet, die bestehende Standards nutzt und einheitlich einsetzt. „Am Ende sollen die Anlagenbetreiber mit unserer Lösung die Daten aller Geräte nutzen können.“ Dass es bis zu internationalen, gar globalen Standards noch ein weiter Weg ist, ist Hans-Jürgen Huber bewusst. Dennoch zeigt der Experte für das industrielle Internet der Dinge sich optimistisch: „Bei Schraubgewinden hat es Jahrzehnte gedauert, Industrienormen zu definieren. Die Entwicklung einheitlicher Standards in der Datenwelt wird deutlich schneller vonstattengehen.“ Nicht zuletzt, weil der Druck auf die verfahrenstechnische Industrie groß ist und weiter wächst, angetrieben durch Klima- und Umweltschutz, Energiewende und Elektrifizierung. Für Rolf Birkhofer steht deshalb fest: „Es ist keine Frage ob, sondern nur wann die Datenschätze aus den Anwendungen unserer Kunden gehoben werden. Was digitalisierbar ist, wird digitalisiert werden.“
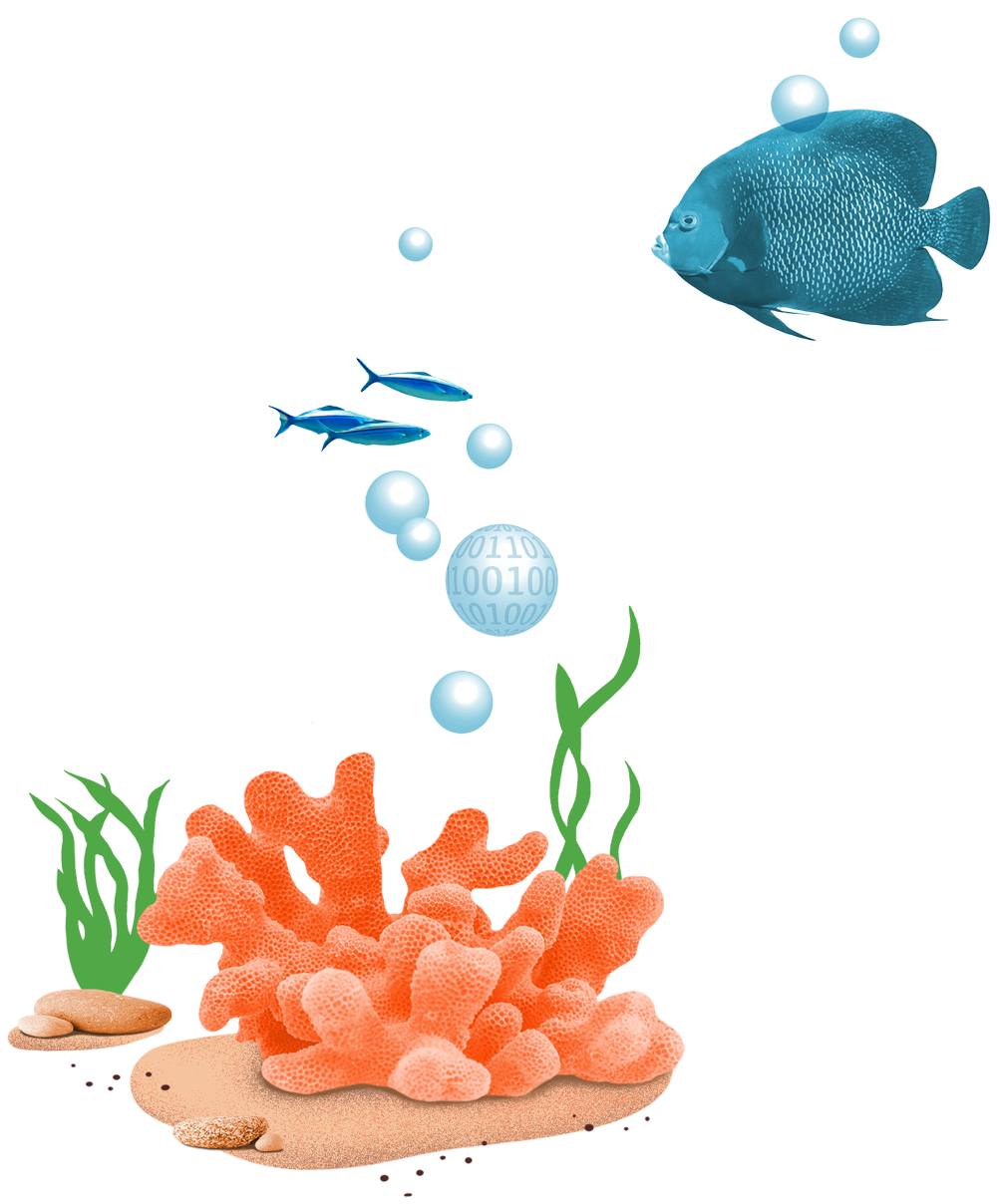
Veröffentlicht am 12.10.2022, zuletzt aktualisiert am 16.01.2023.
Tauchen Sie mit dem Newsletter von «changes» jeden Monat durch neue spannende Geschichten in die Welt der Prozessindustrie ein!
Newsletter abonnieren