Alle für einen
Wasserstoff gilt als Schlüssel zur Energiewende und Klimaneutralität ganzer Industrien. Entlang der gesamten Wertschöpfungskette arbeiten Unternehmen an Technologien und Applikationen, um dem neuen Energieträger zum Durchbruch zu verhelfen. Drei Beispiele.
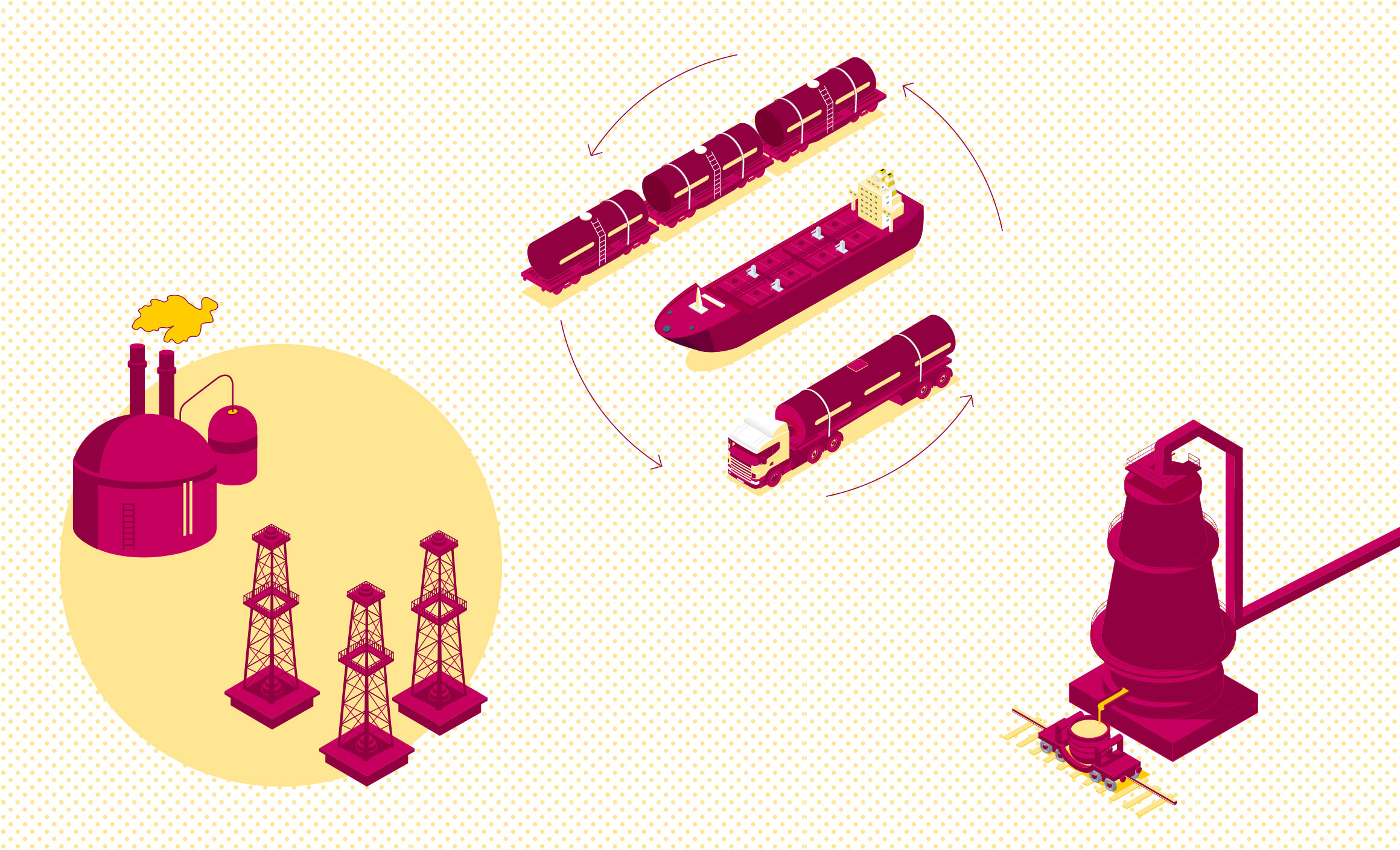

1. Plasmalyse erschließt neue Wasserstoffquellen
Bei der Herstellung von klimaneutralem Wasserstoff steht im Augenblick Wasser (H2O) als Rohstoff im Fokus. Per Elektrolyse wird es mit Ökostrom in Wasserstoff (H2) und Sauerstoff (O) gespalten. Allerdings kommt Wasserstoff nicht nur in Wasser vor. Er ist auch Teil etlicher Kohlenwasserstoff- und Stickstoffverbindungen in Abwässern, Gülle oder Gasen. Das Berliner Unternehmen Graforce möchte ihn aus solchen Reststoffen herausholen: Es hat ein Verfahren zur Plasma-Elektrolyse („Plasmalyse“) entwickelt, bei dem mit erneuerbarer Energie ein hochfrequentes Plasmafeld erzeugt wird. Dieses spaltet dann in Schmutzwasser enthaltene Ammoniak-Moleküle (NH3) oder Methan-Moleküle (CH4) aus Erd- oder Biogas in ihre Komponenten. „H2 ist in Wasser fester gebunden als in anderen chemischen Verbindungen. Deshalb benötigt die Methan-Plasmalyse im Vergleich zur Wasserelektrolyse nur ein Fünftel der elektrischen Energie, um die gleiche Menge an Wasserstoff zu erzeugen“, erläutert Dr. Jens Hanke, Geschäftsführer von Graforce. Das senkt die Herstellungskosten erheblich. Beim Einsatz von Methan entsteht durch die Plasmalyse zudem auch fester Kohlenstoff, der zum Beispiel in der Bau- oder Stahlindustrie genutzt werden kann; wird Biomethan verwendet, kommt es sogar zu negativen CO2-Emissionen, da hier das CO2 dem natürlichen Kreislauf entzogen wird. Bei Erdgas als Ausgangsstoff könnte die Öl- und Gasindustrie die Technologie auch nutzen, um dessen Abfacklung zu vermeiden und damit ihre Klimaziele zu erreichen. Die modularen Anlagen von Graforce sind bereits marktreif. Endress+Hauser liefert die Messtechnik für die Methan-Plasmalyse. „Pluspunkte sind unser großes Portfolio, unser Anwendungswissen, die online verfügbare technische Dokumentation – und die Betreuung vor Ort, die wir überall auf der Welt anbieten können“, erklärt Mathias Christ, technischer Vertriebsmitarbeiter von Endress+Hauser in Berlin.
2. Innovative Träger vereinfachen die Logistik
Grüner Wasserstoff lässt sich häufig nicht dort wirtschaftlich produzieren, wo er benötigt wird. Doch wie soll er transportiert werden? Im Gasnetz ist der Wasserstoff nur eingeschränkt dem Erdgas beimischbar. Für die Logistik per Schiff muss das hochentzündliche Gas bei –250 °C verflüssigt werden; Kühlung und Kompression kosten viel Energie. Eine neue Lösung bieten nun flüssige organische Wasserstoffträger (Liquid Organic Hydrogen Carriers – LOHCs): Das sind ungesättigte, meist aromatische Kohlenwasserstoffverbindungen, die durch eine katalytische Reaktion in der Lage sind, Wasserstoff aufzunehmen. So gebunden, kann das H2 ganz einfach unter Umgebungsbedingungen ohne Druck- oder Kryobehälter gelagert und bewegt werden. Für den Transport lässt sich die bestehende Logistik-Infrastruktur für Flüssigbrennstoffe wie Tankschiffe, Tankwagen und Eisenbahn-Kesselwagen nutzen. Am Verbrauchsort wird der Wasserstoff schließlich wieder aus dem Flüssigträger freigesetzt. „Messtechnik ist sowohl für die Hydrierung zu Beginn als auch die Dehydrierung nach dem Transport unerlässlich: Sie hilft, die chemischen Reaktionen zu überwachen und zu kontrollieren“, sagt Jens Hundrieser, europäischer Branchenmanager Energie bei Endress+Hauser. „Prozessphotometer machen zudem durch eine Inline-Farbmessung eine Qualitätskontrolle und Reinheitsüberwachung von LOHCs möglich.“


3. Koksgas macht Hochöfen transformationsfit
Die Zukunft der Stahlproduktion liegt in der Nutzung von Wasserstoff. Er soll künftig in neuen Produktionsverfahren wie der Direktreduktion zum Einsatz kommen und damit die klassische kohlenstoffbasierte Hochofenroute ersetzen. Aufgrund der langen Investitionszyklen für Hochöfen und weil für die Direktreduktion sehr viel grüner Wasserstoff zur Verfügung stehen muss, braucht es jedoch Etappen-Technologien auf dem Weg zum klimaneutralen Stahl. „Eine Möglichkeit besteht darin, Koksgas in die Hochöfen einzudüsen“, sagt Jens Hundrieser. Koksgas besteht zu 55 Prozent aus Wasserstoff, dieser ersetzt dann im Prozess Kohle als Reduktionsmittel und Energieträger. Der Vorteil: Hersteller können auf diese Weise ihre Emissionen sofort senken und schaffen gleichzeitig die Voraussetzung, um ihre Hochöfen künftig mit grünem H2 zu betreiben. In Deutschland nutzen Dillinger und Saarstahl bereits seit 2020 die neue Technik; die Eindüsungssysteme stammen vom Anlagenbauer Paul Wurth. Aufgrund der langjährigen, partnerschaftlichen Kundenbeziehungen haben beide Unternehmen ihre Anlagen mit Endress+Hauser Messtechnik ausgerüstet, darunter 200 Cerabar-Drucksensoren.
Veröffentlicht am 31.01.2024, zuletzt aktualisiert am 12.02.2024.
Tauchen Sie mit dem Newsletter von «changes» jeden Monat durch neue spannende Geschichten in die Welt der Prozessindustrie ein!
Newsletter abonnieren